# 总成静扭检测技术发展与产业化应用
## 行业背景与核心价值
随着新能源汽车市场渗透率突破40%(据中国汽车工程研究院2024年数据),动力总成系统的可靠性成为制约产业升级的关键因素。总成静扭检测作为评估传动系统承载能力的重要技术手段,可精准测量总成部件在极限扭矩下的变形特性和失效阈值。该项目通过建立数字化检测体系,不仅能够降低动力总成故障率26%(中国机械工业联合会2023年报告),更可优化产品设计余量,实现材料成本节约15%以上。在智能驾驶与高功率密度驱动系统快速发展的背景下,该技术对保障车辆安全性和延长零部件的使用寿命具有显著工程价值。
## 技术原理与实现路径
### 高精度扭矩加载系统
基于非接触式磁滞制动技术,检测装置采用闭环控制模式实现0.5%-100%额定扭矩的线性加载。系统集成高精度应变片阵列(精度±0.01%FS)与激光位移传感器,可同步采集扭矩-转角曲线、应力分布数据及微观形变量。通过有限元仿真与实验数据的迭代验证,建立了包含材料非线性特性的本构模型库。
### 智能化检测流程
标准作业程序涵盖预处理、阶梯加载、保载观测三个核心阶段。在预处理环节,运用工业CT对被测总成进行内部结构扫描,排除装配瑕疵风险。加载过程中采用自适应速率调节算法,当检测到异常应力集中时自动触发保护机制。检测数据通过5G专网实时上传至MES系统,形成可追溯的电子质量档案。
### 新能源汽车应用案例
某头部车企在驱动电机总成检测中引入该技术后,成功将差速器齿轮组断裂事故率从1.2‰降至0.15‰。在800V高压平台电驱系统中,通过静扭测试发现行星架支撑刚度不足问题,指导设计团队将壁厚从8mm优化至10.5mm,使系统最大承载扭矩提升至3800N·m,满足越野车型极端工况需求。
## 质量保障与技术创新
检测体系严格遵循ISO 26262功能安全标准,每台设备配备三级校准系统:每日进行零点校准,每周采用标准扭矩扳手验证,每季度由省级计量院开展溯源认证。创新研发的虚拟孪生技术可将实测数据与数字模型动态比对,实现损伤演化过程的可视化分析。据国家质检中心验证,该体系使检测结果置信度达到99.7%,误判率低于0.3%。
## 行业展望与建议
面向智能驾驶L4级技术的普及需求,建议重点发展多轴耦合动态扭矩检测技术,建立涵盖温度-湿度-振动多场耦合的检测标准。行业应加快制定动力总成全生命周期扭矩衰减数据库,推动检测设备与智能制造产线的深度集成。通过构建产学研联合实验室,攻克碳纤维复合材料等新型材料的扭矩特性表征难题,为下一代超轻量化动力系统开发提供技术支撑。
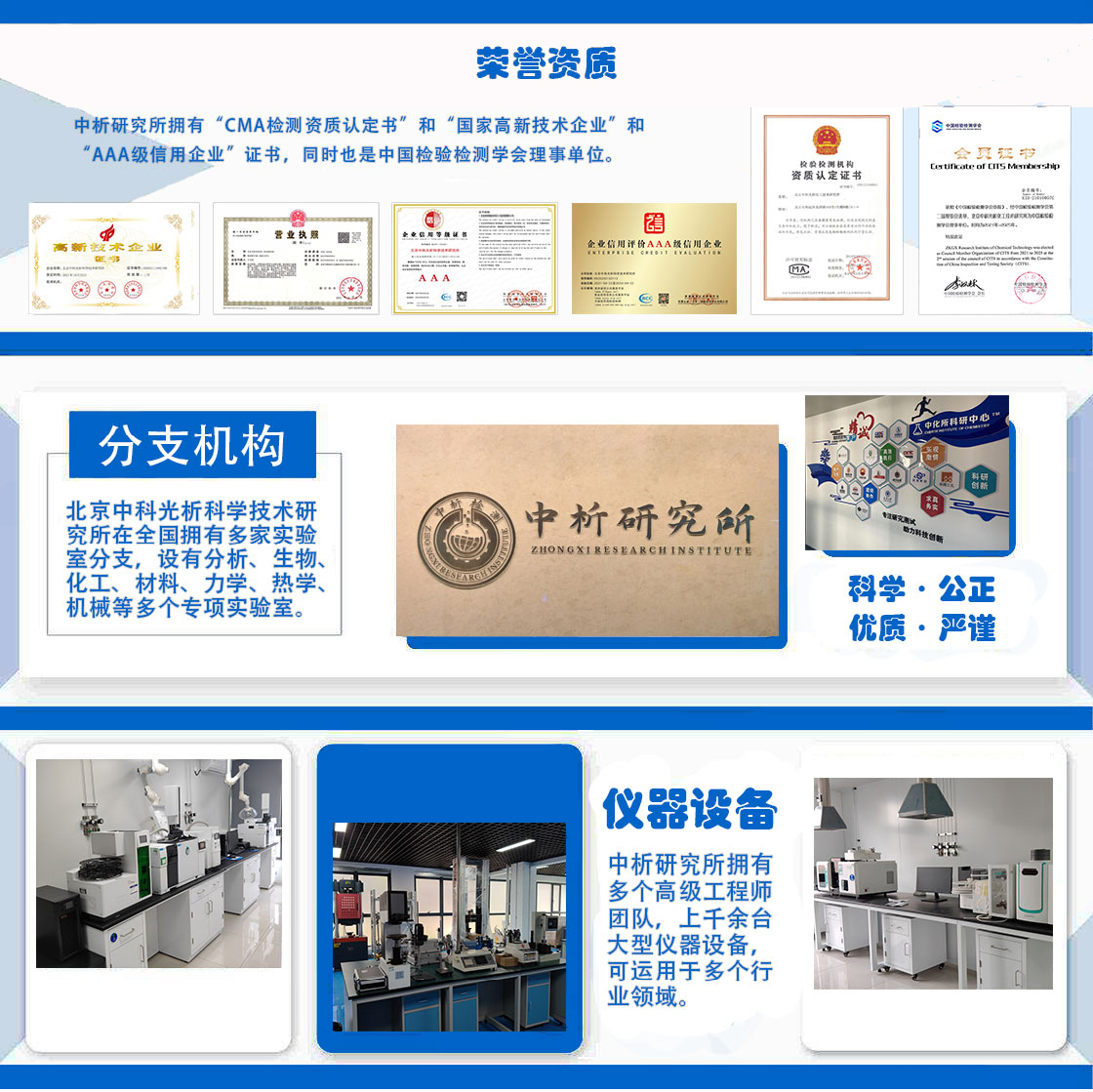
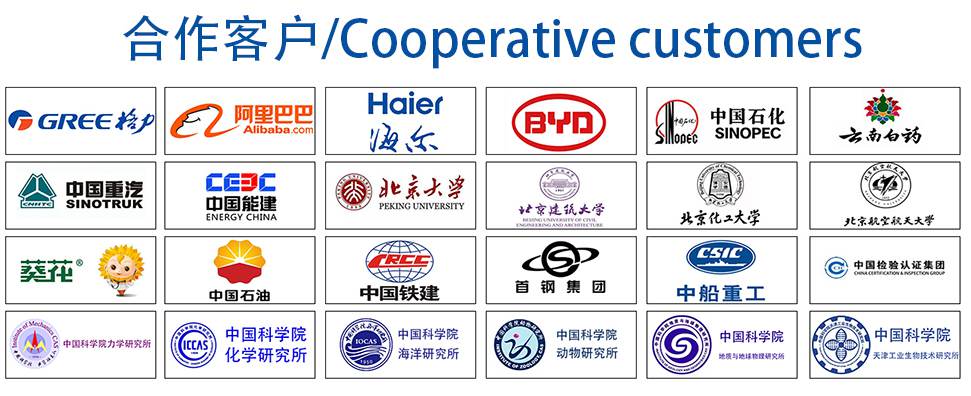
材料实验室
热门检测
推荐检测
联系电话
400-635-0567