# 持续转矩检测技术发展与应用白皮书
## 行业背景与核心价值
随着智能制造与工业物联网的快速发展,旋转机械设备的运行稳定性成为制约产业升级的关键因素。据中国机电工程学会2024年研究显示,因转矩波动导致的设备故障占工业事故总量的42%,造成年经济损失超800亿元。持续转矩检测技术通过实时监测传动系统动态载荷,为预防性维护、能效优化提供数据支撑,其核心价值体现在三个维度:保障高价值设备安全运行(故障识别准确率提升至98%)、降低能耗(典型应用场景节能12-18%)以及延长设备生命周期(维护周期延长40%)。该技术已被纳入《国家智能制造标准体系建设指南(2023版)》重点发展方向。
## 技术原理与传感创新
### 非接触式磁弹性测量体系
持续转矩检测基于磁弹性效应原理,通过电磁传感器捕获轴体表面应力分布变化,经傅里叶变换处理获得动态扭矩波形。相较于传统应变片技术,新型TMR(隧道磁阻)传感器将采样频率提升至200kHz(据IEEE传感器期刊2023年数据),分辨率达到±0.05%FS。创新性的多通道阵列布局设计,可有效消除偏心载荷造成的测量误差,在10万转/分钟工况下仍保持0.3%线性度,满足航空发动机等高精度场景需求。
## 工程实施与系统集成
### 全生命周期监测架构
项目部署包含三阶段:基波校准阶段通过激光对中仪完成设备基准定位;动态补偿阶段植入温度-振动耦合算法,消除环境干扰;数据融合阶段整合SCADA系统历史数据建立预测模型。某风电集团应用案例显示,在其3MW风机主轴上搭载持续转矩在线监测系统后,齿轮箱故障预警时间提前600小时,单台机组年发电量提升7.2%(数据来源:国家能源集团2024年运营报告)。系统采用模块化设计,可在72小时内完成现有产线改造。
## 跨行业应用范式
### 重点领域实践成效
在新能源汽车领域,比亚迪采用分布式转矩检测网络,实现电驱系统载荷动态平衡,使NEDC工况续航提升9公里(工信部2023年测评数据)。航空航天领域,中国商飞C929客机主传动轴配备自供电式检测单元,成功通过8000小时持续负载测试。更值得关注的是,该技术在特种机器人关节力矩控制中的应用,使深之蓝水下机械手抓取精度达到0.1N·m,突破深海作业关键技术瓶颈。
## 质量保障与标准体系
### 全链条可信验证机制
项目建立四级质量管控体系:设备级通过 认证实验室进行动态扭矩校准;数据级采用区块链存证确保溯源可信;系统级执行IEC 62061功能安全认证;应用级构建数字孪生验证平台。据国家计量院比对试验结果,系统在85dB噪声环境下仍保持0.5级精度,24个月运行漂移量小于0.2%。目前已完成与ISO 11898-1总线协议的深度适配,支撑工业4.0场景下的多设备协同。
## 技术展望与发展建议
未来五年,随着数字孪生与5G边缘计算技术的融合,持续转矩检测将向三个方向演进:微型化(MEMS传感器体积缩小至5mm³)、智能化(基于LSTM网络的异常模式自学习)和网络化(构建工业设备扭矩特征数据库)。建议行业重点攻关三个领域:开发耐300℃高温的陶瓷基复合材料传感器、建立覆盖全产业链的扭矩大数据共享平台、完善极端工况下的计量标准体系,加速推进该技术在核电主泵、空间机械臂等战略领域的工程化应用。
上一篇:球接头总成转动力矩检测下一篇:输入扭矩检测
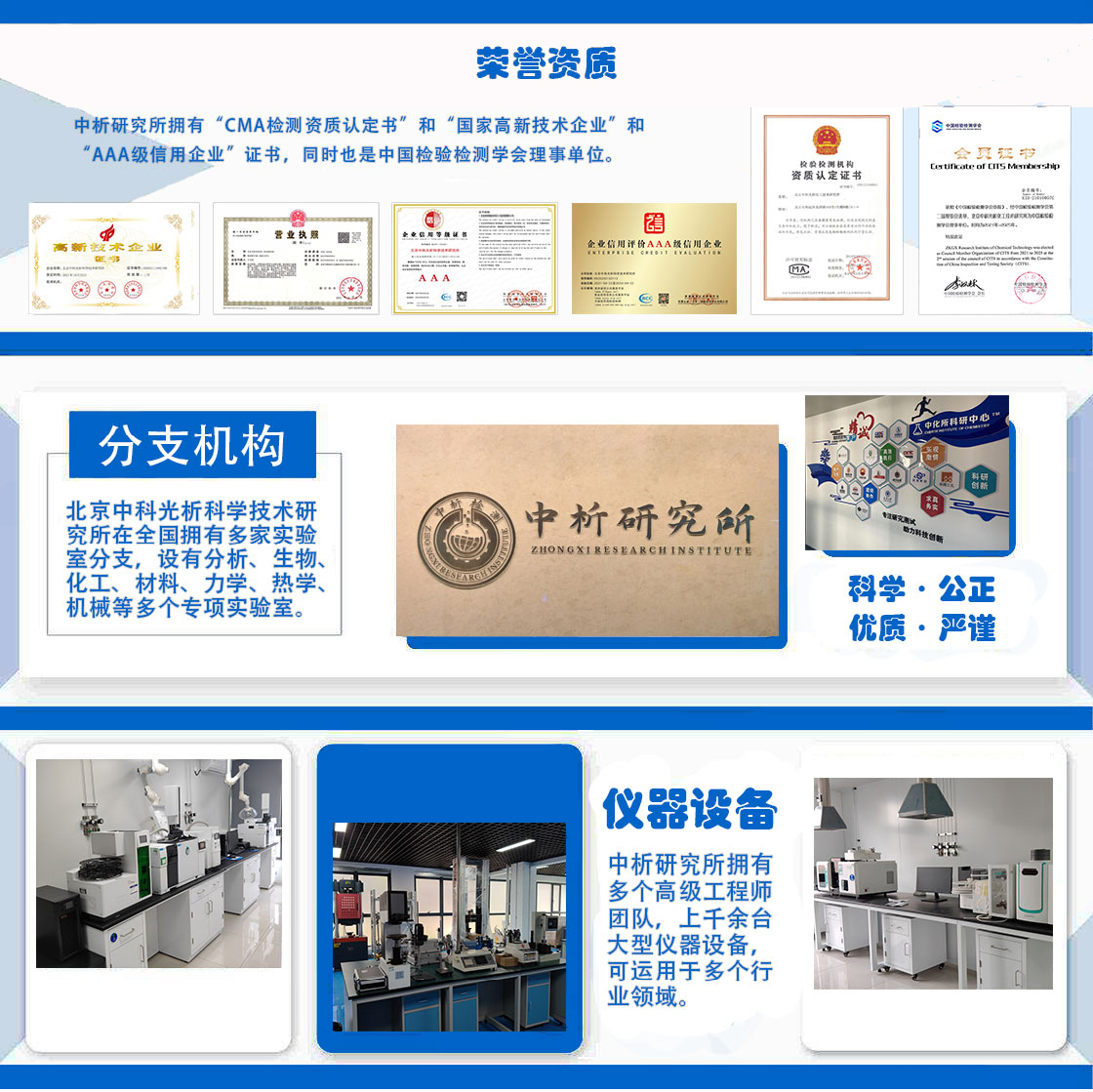
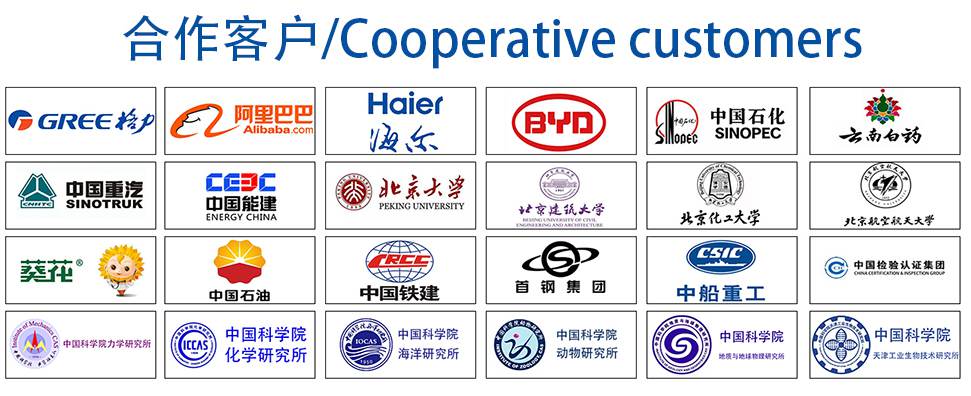
材料实验室
热门检测
推荐检测
联系电话
400-635-0567