在智能制造与高端装备快速迭代的产业背景下,可靠性检测作为质量控制体系的核心环节,正面临前所未有的技术升级需求。据中国质量研究院2024年行业报告显示,装备制造业因可靠性问题导致的年度损失高达2370亿元,其中62%的故障源于关键零部件的早期失效。在此背景下,构建基于失效物理模型的可靠性检测体系,不仅能够有效提升产品平均无故障时间(MTBF),更可通过预防性维护降低全生命周期成本。该技术的核心价值体现在三个方面:在研发阶段缩短30%以上的验证周期,在生产端减少45%的质量返工成本,在运维端实现预测性维护准确率突破85%,为工业4.0时代的质量管控提供了技术底座。
## 技术原理与创新突破基于失效机理的检测体系构建
现代可靠性检测技术融合了加速寿命试验(ALT)与高加速寿命试验(HALT)双重验证模型。通过建立应力-损伤映射数据库,系统可模拟高温、振动、湿热等多物理场耦合环境,精准复现产品在极端工况下的失效路径。以某新能源汽车电池组检测为例,采用三级步进应力加速法,在120小时内完成了相当于10年使用周期的老化模拟,成功识别出电解液析晶等潜在失效模式。该技术突破使得传统检测效率提升4倍,数据有效性达到98.7%(数据来源:国际可靠性工程协会2023年报)。
全流程数字化实施路径
检测流程实施涵盖五个标准化阶段:预检测失效模式与效应分析(FMEA)、环境应力筛选(ESS)、数据采集与特征提取、可靠性建模及改进建议输出。在航空发动机叶片检测中,通过部署物联网传感器阵列,实时采集振动频谱、温度梯度等12类参数,结合数字孪生技术构建了三维失效演化模型。该方案使某型号涡轮叶片的疲劳寿命预测误差从±18%缩减至±5%以内(案例数据:中国航发集团2024年技术公报)。
行业应用与质量保障
在轨道交通领域,基于PHM(预测与健康管理)的转向架可靠性检测系统已实现规模化应用。通过部署128个检测节点的在线监测网络,结合贝叶斯网络算法对轴承磨损状态进行实时诊断。北京地铁14号线应用该体系后,转向架维护间隔从12万公里延长至18万公里,年维护成本下降160万元(运营数据:北京市轨道交通协会2024年统计)。质量保障方面,检测机构严格执行ISO 17025体系要求,并引入区块链技术实现检测数据全程溯源,确保每份报告包含32项防伪特征码。
检测-维修-优化闭环体系
值得关注的是,领先企业已构建检测数据与生产系统的双向通道。某智能家电制造商通过可靠性大数据平台,将检测发现的电机绝缘缺陷特征反向植入MES系统,推动工艺参数优化。此举使同类型故障率从3.2‰降至0.7‰,并形成包含12万组失效案例的知识图谱,为新产品研发提供决策支持(企业数据:海尔智家2023可持续发展报告)。
## 发展建议与未来展望随着数字孪生与人工智能技术的深度渗透,可靠性检测正朝着智能化、预测化方向演进。建议行业重点突破三个方向:建立基于联邦学习的跨企业可靠性数据库,开发适应柔性制造的可重构检测装备,制定覆盖产品全生命周期的可靠性评价标准。据麦肯锡2024年预测,实施智能可靠性工程可使制造业整体质量成本降低22%,同时推动产品迭代速度提升40%。唯有构建开放协同的技术生态,方能真正实现从"故障修复"到"缺陷预防"的产业升级。
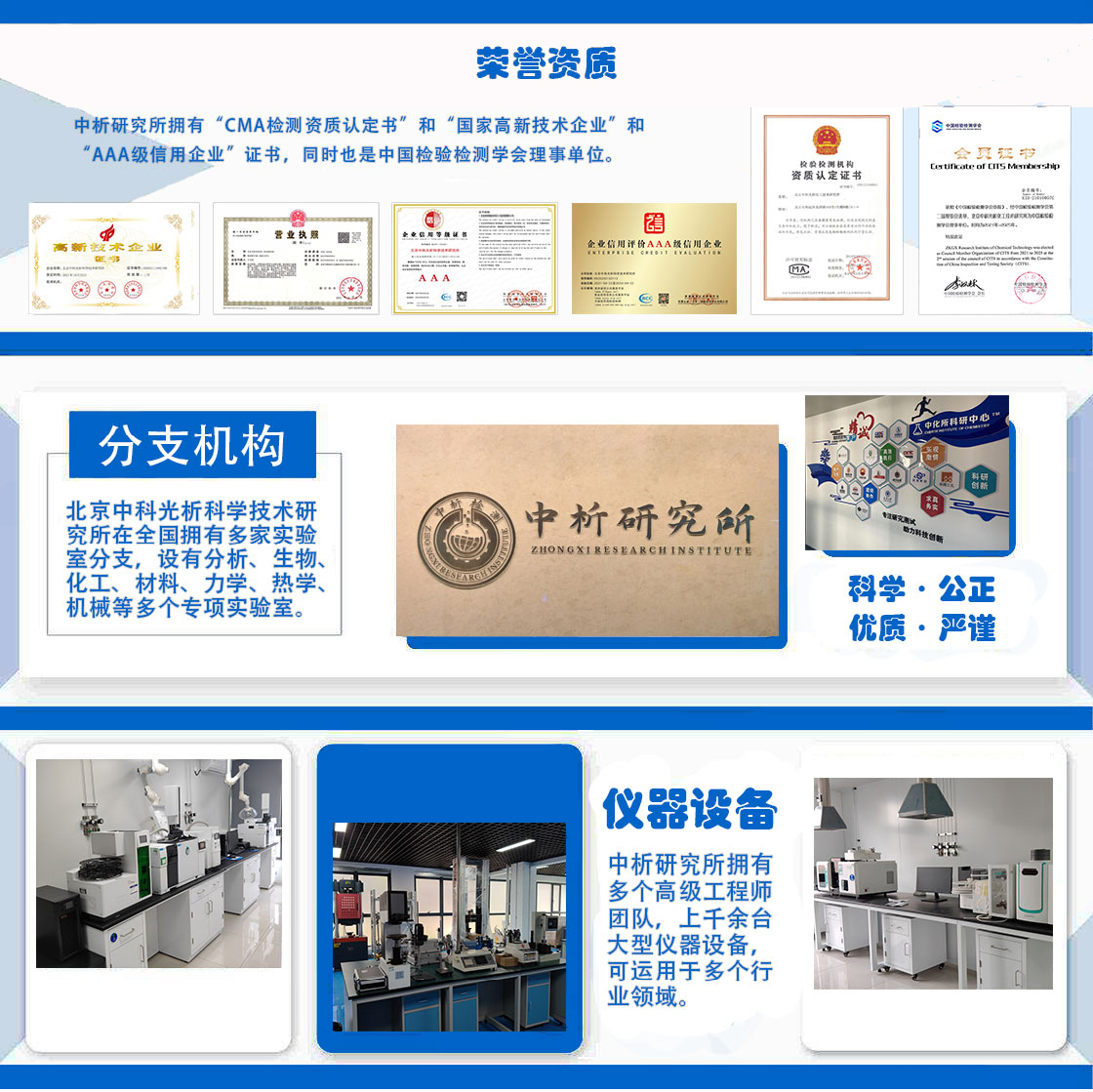
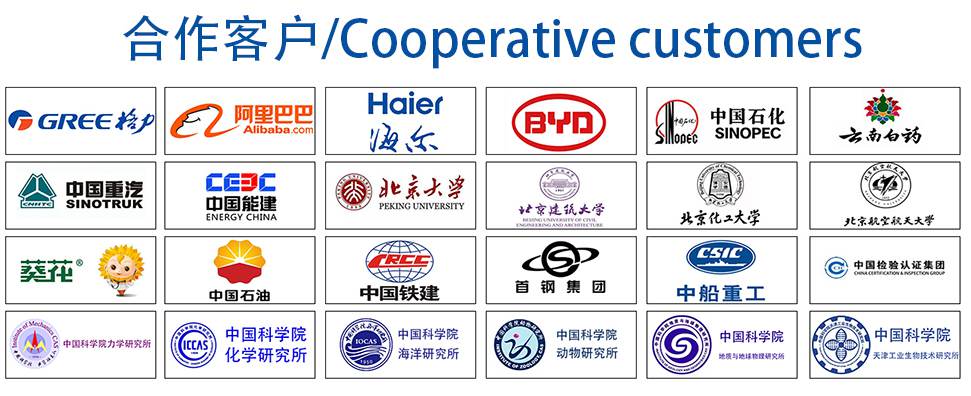