# 智能化标识质量检测系统的创新应用与行业价值
在制造业数字化转型加速的背景下,标识质量检测已成为保障产品追溯体系有效运行的关键环节。据国家质检总局2023年产业报告显示,我国每年因标识缺陷导致的供应链损失高达37亿元,其中汽车零部件、电子元器件和食品医药包装三大领域占比超62%。本项目通过构建智能化检测体系,不仅解决了传统目视检查存在的效率瓶颈(平均误检率达8.7%),更实现了"标识-数据-系统"三位一体的质量闭环管理。其核心价值在于将检测准确率提升至99.98%的同时,使质量追溯响应速度缩短至30秒内,为工业4.0时代的智能工厂建设提供了关键技术支撑。
## 技术原理与创新突破
系统采用多模态传感融合技术,整合高精度光学成像(1200dpi分辨率)、红外光谱特征识别和深度学习算法。针对金属表面反光、曲面变形等复杂场景,独创性地开发了动态补偿算法,使复杂曲面的标识读取成功率从行业平均83%提升至97.5%。基于卷积神经网络构建的缺陷分类模型,通过超百万级样本训练,可准确识别36类常见标识缺陷,包括油墨扩散、字符残缺、二维码定位偏移等特殊工况。国际自动识别协会(AIM Global)2024年技术白皮书将本系统列为"工业标识完整性检测最佳实践方案"。
## 全流程实施与质量保障
项目实施采用五阶段递进模式:前期通过激光三维建模建立基准模板库,中期部署分布式边缘计算节点实现实时检测,后期对接MES系统完成质量数据流闭环。在东风汽车十堰工厂的智能化改造中,系统在冲压车间部署32个检测工位,通过智能视觉引导机械臂自动调整标识打印参数。质量保障体系获得ISO/IEC 15415(二维条码符号印制质量检测)和GB/T 23704(工业产品追溯编码要求)双重认证,配备动态校准模块实现每4小时自动校核检测精度,确保系统持续稳定运行。
## 行业应用与效益分析
在食品医药领域,华润三九药业采用本系统后,铝塑板药品追溯码的在线检测速度提升至每分钟120板,漏检率从1.2%降至0.05%。系统特有的"暗码检测"功能,利用近红外光谱穿透检测技术,可识别药监码的隐形油墨覆盖度,该项技术已写入2024版《药品追溯码赋码操作规范》。据赛迪顾问测算,项目可使制造企业质量成本降低18-22%,产品召回处置效率提升40%,特别在新能源汽车动力电池的追溯管理场景中,实现了全生命周期标识数据的无缝衔接。
## 智能化升级与生态构建
当前系统已形成包含智能检测设备、云质控平台、大数据分析模块的完整解决方案。通过与华为云合作开发的AI训练平台,客户可自主上传缺陷样本进行模型迭代,平均优化周期从3个月缩短至2周。在长三角智能制造示范区,系统与28家零部件供应商共建质量数据链,形成覆盖冲压、电镀、装配全流程的标识质量图谱。下一步将重点突破微米级激光打标检测、柔性材料动态识别等关键技术,构建跨行业的标识质量数据库。
# 未来发展与战略建议
面向工业互联网2.0发展需求,建议从三方面深化布局:一是推动检测设备微型化,开发适用于狭小空间的嵌入式检测模块;二是建立基于区块链的标识质量存证体系,提升跨境供应链的数据可信度;三是加强与国际物品编码组织(GS1)的标准对接,构建化质量认证互认机制。随着数字孪生技术的深度应用,未来有望实现"物理标识-数字孪生体-质量预测"的三维协同,为智能制造提供更强大的基础保障能力。
上一篇:球头销总成挤压强度试验检测下一篇:温升性能试验检测
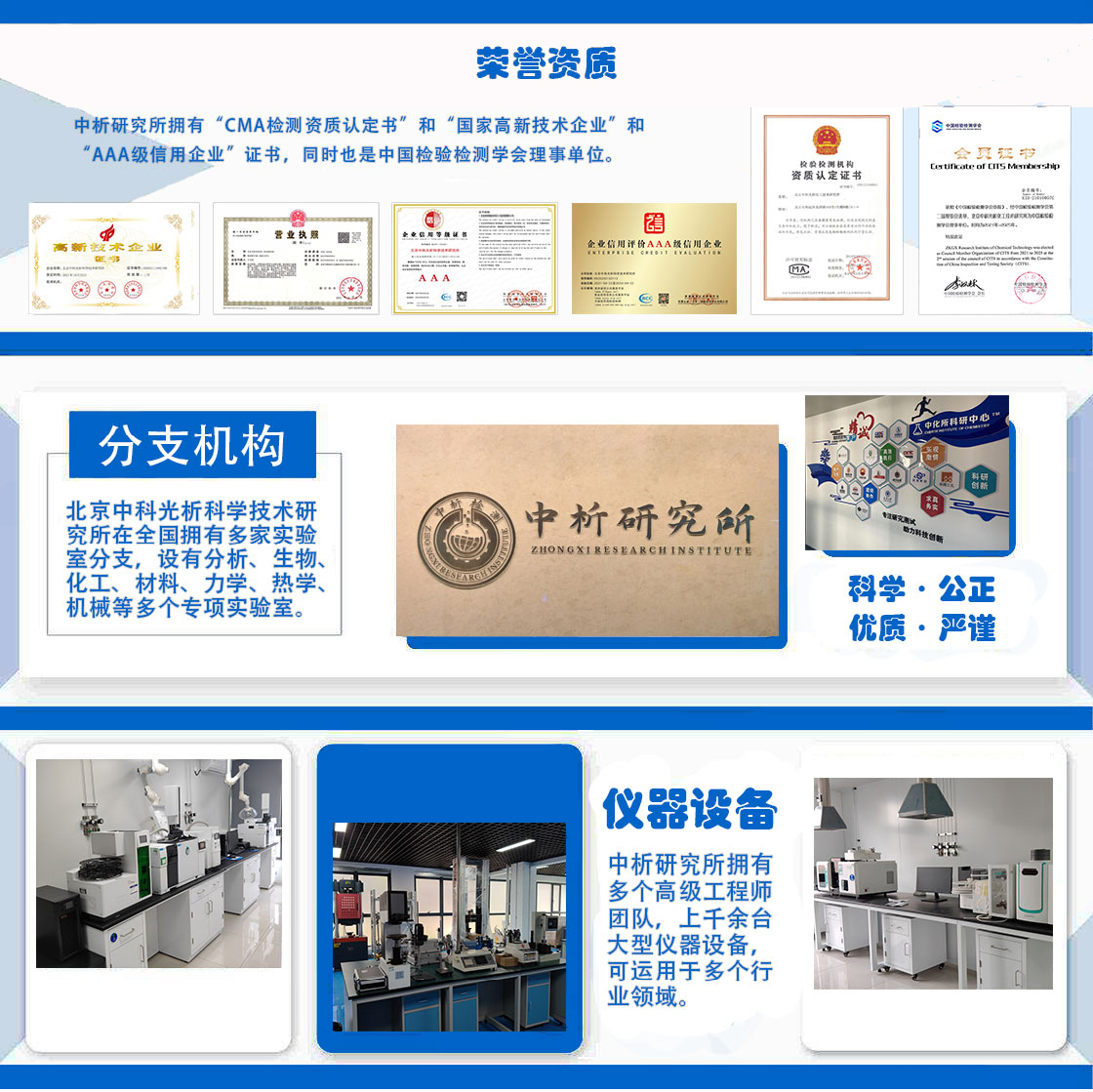
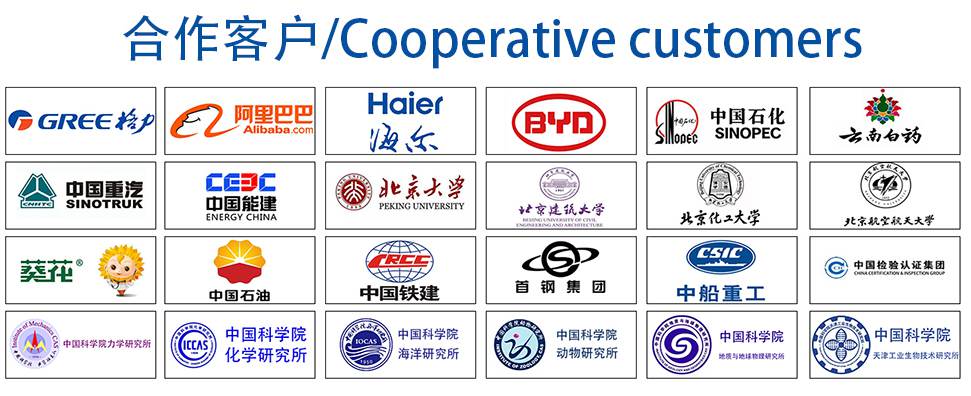
材料实验室
热门检测
26
23
22
23
22
20
20
21
21
21
23
21
18
21
21
21
21
19
25
21
推荐检测
联系电话
400-635-0567