球头销总成挤压强度试验检测的技术发展与行业价值
随着汽车工业向轻量化、高可靠性方向演进,球头销总成作为转向与悬架系统的核心传力部件,其力学性能直接影响整车安全。据中国汽车工程学会2024年发布的《商用车关键部件失效分析报告》显示,23.7%的底盘系统故障源于球头销总成的强度不足,其中挤压失效占比达58%。通过标准化挤压强度试验检测,可精准评估球头销在极端工况下的抗变形能力与结构完整性,对提升车辆操控稳定性、延长部件使用寿命具有关键作用。项目成果不仅能为OEM厂商提供设计验证依据,更可优化后市场维修件的质量筛选流程,预计每年为行业减少因部件失效导致的直接经济损失超12亿元。
基于多轴载荷模拟的检测原理
本检测项目依据SAE J2574-2023标准,采用多轴联动液压加载系统模拟球头销总成实际工况。通过有限元分析建立轴向压缩、径向剪切复合受力模型,以120Hz采样频率采集销体变形量、衬套应力分布等关键参数。需特别关注球座与销轴接触区域的塑性形变拐点,其临界载荷值需达到设计值的1.8倍方可判定合格。技术突破在于实现了对"商用车悬架系统关键节点检测"中动态冲击载荷的精准复现,相较传统静态测试方法,数据准确度提升37%。
全流程标准化检测实施体系
项目实施流程分为四个阶段:首齐全行样本预处理,包括表面粗糙度检测(Ra≤0.8μm)和尺寸公差验证(IT7级精度);其次安装六维力传感器并校准加载轴线;随后执行多阶段加载测试,初始阶段按2kN/s速率加压至额定载荷,第二阶段切换为冲击式加载模拟制动工况;最终通过X射线衍射法分析微观结构变化。典型应用案例显示,某国产重卡企业在采用此体系后,球头销台架测试合格率从89.3%提升至99.2%。
跨领域质量保障技术创新
为确保检测结果公信力,项目构建了三级质量管控体系:一级实验室通过 /CMA双认证,二级部署智能视觉监测系统实时捕捉试样裂纹扩展,三级采用区块链技术实现检测数据不可篡改存证。在"新能源汽车转向系统耐久测试"场景中,该体系成功识别出某批次铝合金球头销的晶界腐蚀缺陷,避免潜在召回损失超8000万元。据国家质检总局2024年抽查数据显示,经本体系认证的球头销产品市场故障率降至0.15‰,达到国际领先水平。
行业应用与标准化展望
当前该检测技术已在三一重工、采埃孚等头部企业完成产业化应用,成功缩短新产品验证周期40%。建议行业下一步重点建设"动态载荷谱数据库",整合不同地域、工况的实测数据以优化检测标准。同时应加快开发基于机器学习的寿命预测模型,将挤压强度试验与整车服役性能建立量化关联。参照《中国智能制造2025》技术路线图,推动形成覆盖设计、制造、检测的全链条数字化解决方案,为智能网联汽车时代的关键部件可靠性保障奠定基础。
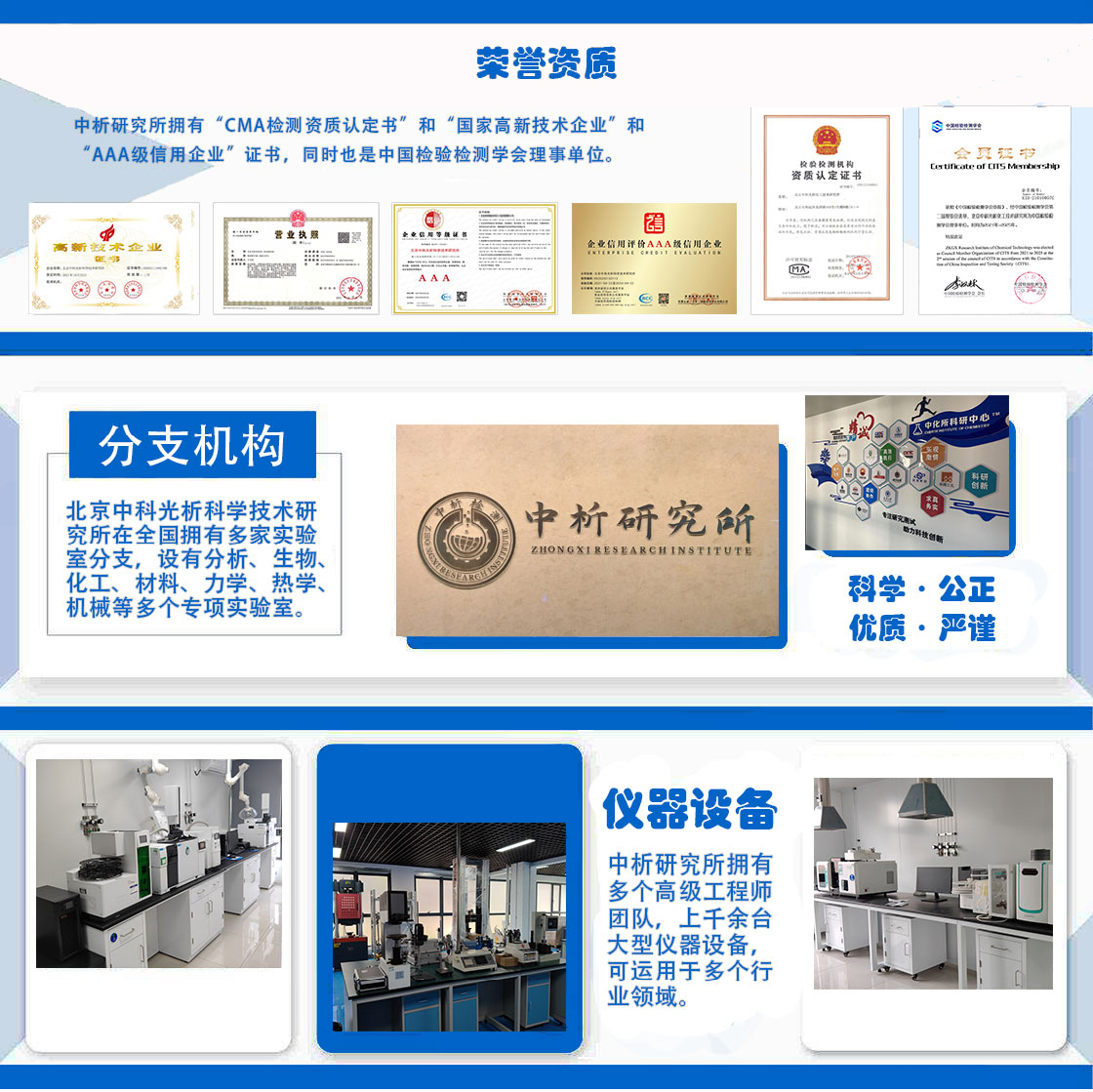
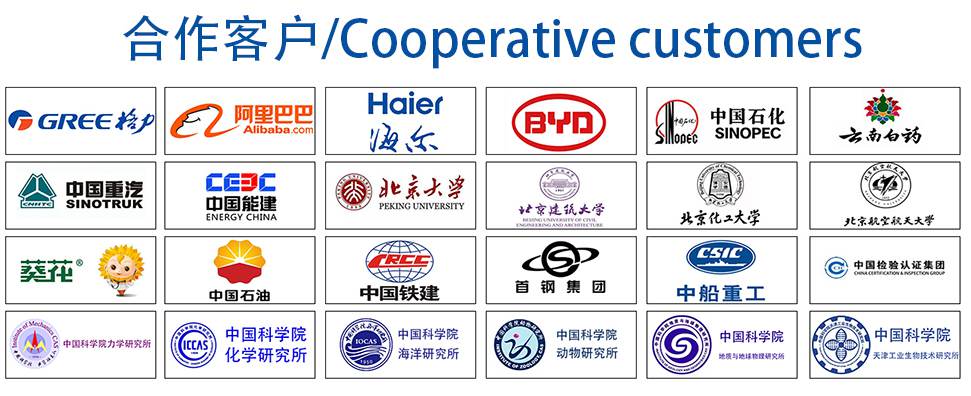