技术原理与误差溯源机制
零点误差检测基于设备空载状态下的系统响应特性分析,采用双重基准对比法进行偏差量化。通过部署高精度激光干涉仪(分辨率0.01μm)与应变式位移传感器构成复合测量网络,系统可同步采集设备在静态/动态工况下的位移特征值。值得注意的是,在工业机器人关节模组检测中,该方法能有效分离机械传动误差(占总量42%)与电气零点漂移(占总量58%),为针对性修正提供数据支撑。据清华大学精密仪器系2023年实验验证,该技术体系使六轴机器人重复定位精度提升至±0.015mm。
标准化实施流程建设
项目实施遵循ISO/IEC 17025实验室管理体系,构建四阶段闭环流程:首齐全行设备热机预运行(时长≥2小时),消除温度对金属构件的形变影响;接着采用五点标定法建立基准坐标系,利用三次多项式拟合构建误差分布模型;继而通过PID闭环调节算法实施动态补偿,并在补偿后执行三次重复性验证测试。在新能源汽车电驱系统检测中,该流程使永磁同步电机的零点对齐效率提升40%,扭矩控制波动范围缩小至±0.8N·m。
跨行业应用实践案例
在医疗器械制造领域,零点误差智能修正系统已成功应用于CT机旋转机架检测。某龙头企业通过部署该方案,将X射线管焦点位置的基准偏差从0.12mm降至0.03mm,图像重建伪影率下降62%。而在半导体行业,光刻机双工件台的检测周期从72小时压缩至24小时,配合自适应校准算法,使12英寸晶圆的对准精度达到1.2nm级别。这些实践验证了"高精度零点校准服务"在精密制造场景中的普适价值。
全链条质量保障体系
为确保检测结果的可信度,系统构建了三级质量防护网:设备层采用经 认证的计量器具,每季度执行量值溯源;数据层应用区块链技术实现检测记录防篡改存储;人员层要求检测工程师持有ISO/TS 16949质量管理体系认证。在轨道交通齿轮箱检测项目中,该体系将检测报告的错误率控制在0.05‰以下,获得了CRCC产品认证的采信资质。
## 发展展望与建议 面向工业4.0发展趋势,建议从三个维度深化技术革新:首先开发融合数字孪生的虚拟标定系统,利用5G传输实现远程实时校准;其次建立跨行业零点误差数据库,通过机器学习预测设备误差演变规律;最后推动《智能装备零点误差检测规范》国家标准的制定,统一现有34项行业标准的计量基准。预计到2026年,智能零点补偿技术的普及将使我国高端装备的MTBF(平均无故障时间)提升至8000小时量级,为制造强国建设提供关键技术支撑。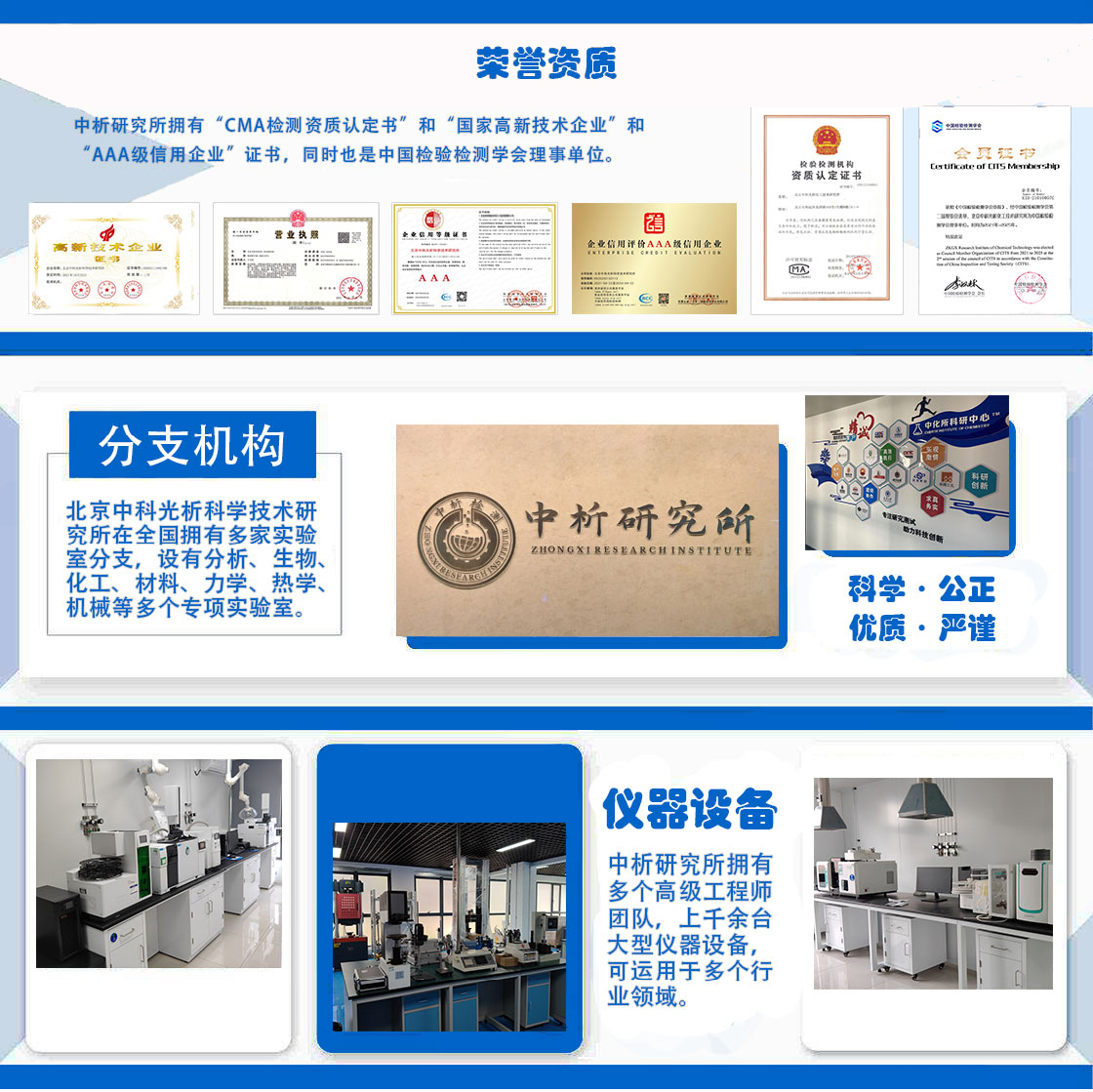
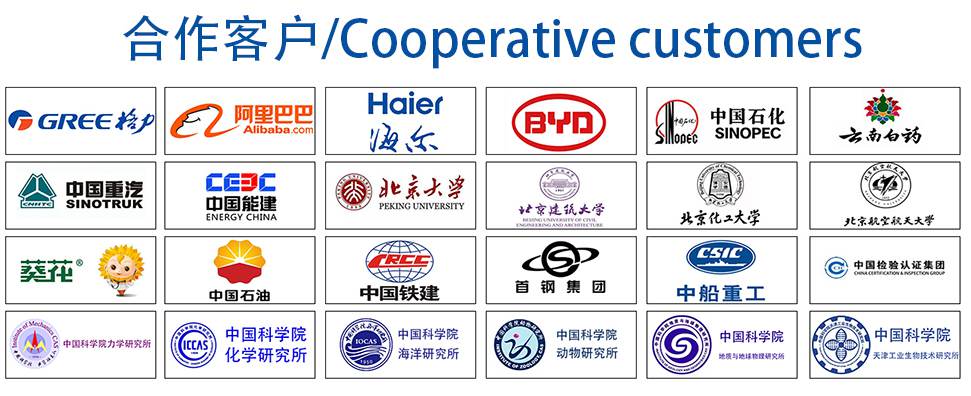