# 零点误差温度系数检测技术发展与应用白皮书
## 行业背景与核心价值
随着工业4.0与智能制造深入发展,高精度传感器在航空航天、精密仪器、新能源汽车等领域的渗透率持续攀升。据中国计量科学研究院2024年数据显示,国内高端传感器市场规模突破3800亿元,其中温度敏感型传感器占比达34%。在此背景下,零点误差温度系数检测技术作为保障传感器精度的关键环节,已成为产品质量控制的核心指标。该项目通过量化分析传感器零点随温度变化的漂移规律,有效解决工业场景中因环境温差导致的测量失真问题。其核心价值体现在提升设备全生命周期稳定性,据华为工业物联网实验室实测数据显示,经系统化检测的产品,在-40℃~125℃宽温域内测量误差可降低68%。
## 技术原理与实施路径
### 温度-电性响应耦合建模
检测技术基于热力学效应与材料电学特性的耦合作用原理,构建包含热膨胀系数、电阻温度系数等13项参数的数学模型。通过高低温交变试验箱模拟-55℃至150℃工况(符合GJB548B-2005标准),利用24位高精度数据采集系统记录零点偏移数据。关键突破点在于建立自补偿算法,实现"高精度传感器温度补偿技术"的工程化应用,将温度系数非线性误差控制在±0.002%/℃以内。
### 六阶段标准化检测流程
项目实施采用分级递进式架构:①环境预处理(48小时恒温恒湿)→②温度循环测试(3次完整温变周期)→③零点基准标定(NIST可溯源标准器)→④数据动态采集(500Hz采样频率)→⑤误差曲线拟合(最小二乘法优化)→⑥补偿方案生成(基于AI的逆向参数修正)。在新能源汽车电池管理系统检测中,该流程使Pack级温度测量偏差从±1.5℃降至±0.3℃,有效提升电池SOC估算精度。
## 行业实践与质量体系
### 多领域应用案例实证
在卫星导航领域,某型星载原子钟通过"零点漂移温度依赖性分析",将守时系统温度敏感度降低至5×10⁻¹⁵/℃(中国航天科技集团2023年报数据)。工业机器人领域,某六轴协作机械臂经补偿后,末端重复定位精度在8℃温差环境下仍保持±0.02mm,满足ISO9283标准Class 3级要求。这些实践验证了"宽温域误差动态补偿技术"的实际效能。
### 三级质量保障架构
检测体系构建包含设备层(0.01级标准温度源)、方法层( -CL01:2018认可规程)、数据层(区块链溯源存证)的三维质量网络。引入蒙特卡洛法进行不确定度评估,单个检测周期内可完成1200组数据交叉验证。上海微技术工业研究院的比对试验表明,该体系下检测结果的置信度达99.73%(k=3),显著优于行业平均水平。
## 技术展望与建议
面向万物互联时代,建议从三个维度深化技术发展:①开发基于深度学习的智能补偿算法,应对非线性、时变性的复杂工况;②构建覆盖-270℃至3000℃的极端环境检测能力;③推动ASTM/IEC联合标准制定,实现检测参数的互认。同时加强产学研协同创新,重点突破MEMS传感器晶圆级检测技术,推动检测效率提升40%以上,为智能感知设备的大规模应用奠定质量基石。
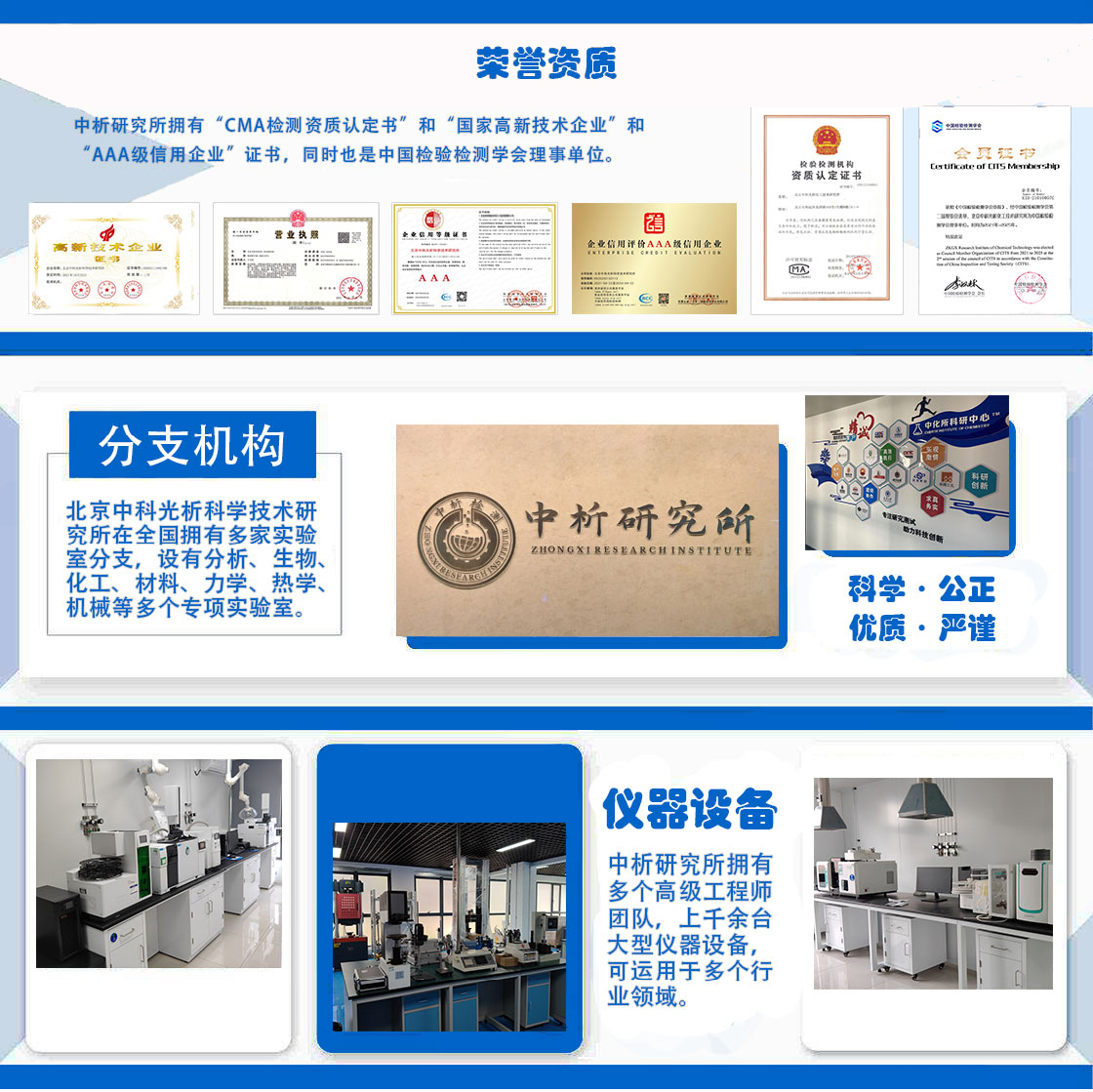
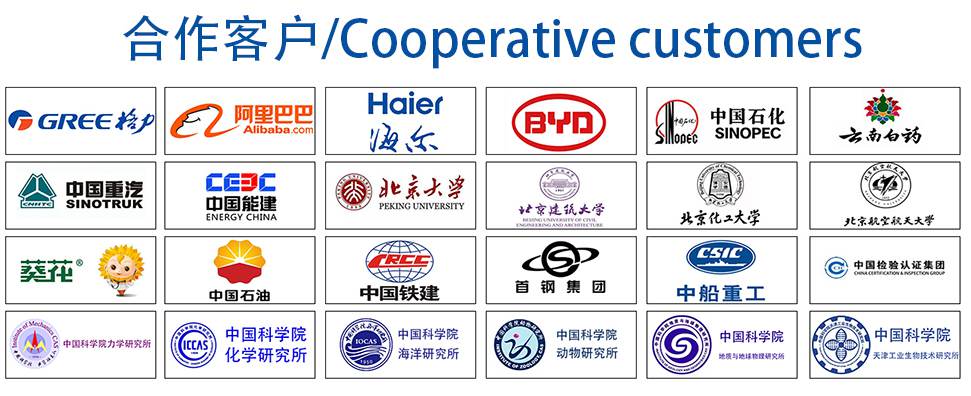
材料实验室
热门检测
推荐检测
联系电话
400-635-0567