# 稳态寿命检测技术发展与应用白皮书
## 行业背景与核心价值
随着高端装备制造与新能源产业快速发展,产品长效可靠性已成为竞争的核心指标。据国家质量技术基础研究院2024年数据显示,我国每年因关键零部件早期失效造成的直接经济损失超1200亿元,其中60%与材料疲劳失效相关。稳态寿命检测通过模拟产品全生命周期运行工况,构建了覆盖设计验证、生产质控到服役维护的全链条质量保障体系。该项目不仅填补了传统加速老化试验与实际工况偏差的技术鸿沟,更在航空发动机叶片、高能量密度锂电池等战略领域形成了突破性解决方案,有效支撑了国产高端装备的可靠性升级。其核心价值体现在将产品寿命预测精度提升至92%以上(国际检测认证集团2023年度报告),显著降低产品全周期质量成本。
## 技术原理与创新突破
### 基于多物理场耦合的检测机理
稳态寿命检测技术深度融合热-力-电多场耦合仿真模型,通过构建涵盖温度梯度、机械应力、化学腐蚀等28个影响因子的失效判据体系,实现对材料微观结构演变的精准预测。中国材料学会2024年技术白皮书指出,该技术采用原位监测与数字孪生相结合的方法,使工况模拟误差控制在±1.5%以内。特别是在极端工况下材料性能衰减分析领域,创新性引入声发射特征识别技术,可提前1200小时预警潜在失效风险。
### 全流程数字化检测体系
项目实施采用"三阶段六维度"架构,从样品预处理阶段的表面改性检测,到持续运行阶段的性能衰减监测,最后至失效临界点的残余寿命评估,全程部署高精度传感器阵列。以某新能源汽车电池包检测为例,通过搭建-40℃至85℃宽温域测试平台,配合2000Hz高频数据采集系统,完整记录充放电循环中的电解液析晶过程。据国家动力电池创新中心实测数据,该体系使电芯寿命评估周期缩短58%,评估成本降低42%。
### 行业应用与质量保障
在航空航天领域,稳态寿命检测技术已成功应用于第三代单晶涡轮叶片的服役评估。通过模拟1650℃高温燃气环境下的热障涂层氧化过程,某型号发动机大修间隔从800小时延长至1200小时。检测系统严格遵循ISO 17025实验室管理体系,配置四级校准网络和区块链数据存证平台,确保检测结果具有国际互认效力。值得关注的是,在新型储能系统领域,该技术助力某100MW/400MWh磷酸铁锂储能电站将电池梯次利用效率提升至83%,年运营成本降低2100万元。
## 发展建议与未来展望
面向十四五智能制造发展规划,建议从三方面深化技术应用:其一,建立覆盖极端温度、强腐蚀等特殊场景的检测标准体系;其二,推动检测设备与工业互联网平台的深度融合,开发具有自学习功能的寿命预测算法;其三,加强政产学研协同创新,在氢能储运装备、深海探测仪器等新兴领域建设国家级检测验证中心。通过构建"检测服务+数据资产"双轮驱动模式,力争到2030年形成覆盖全产业链的智能检测生态体系。
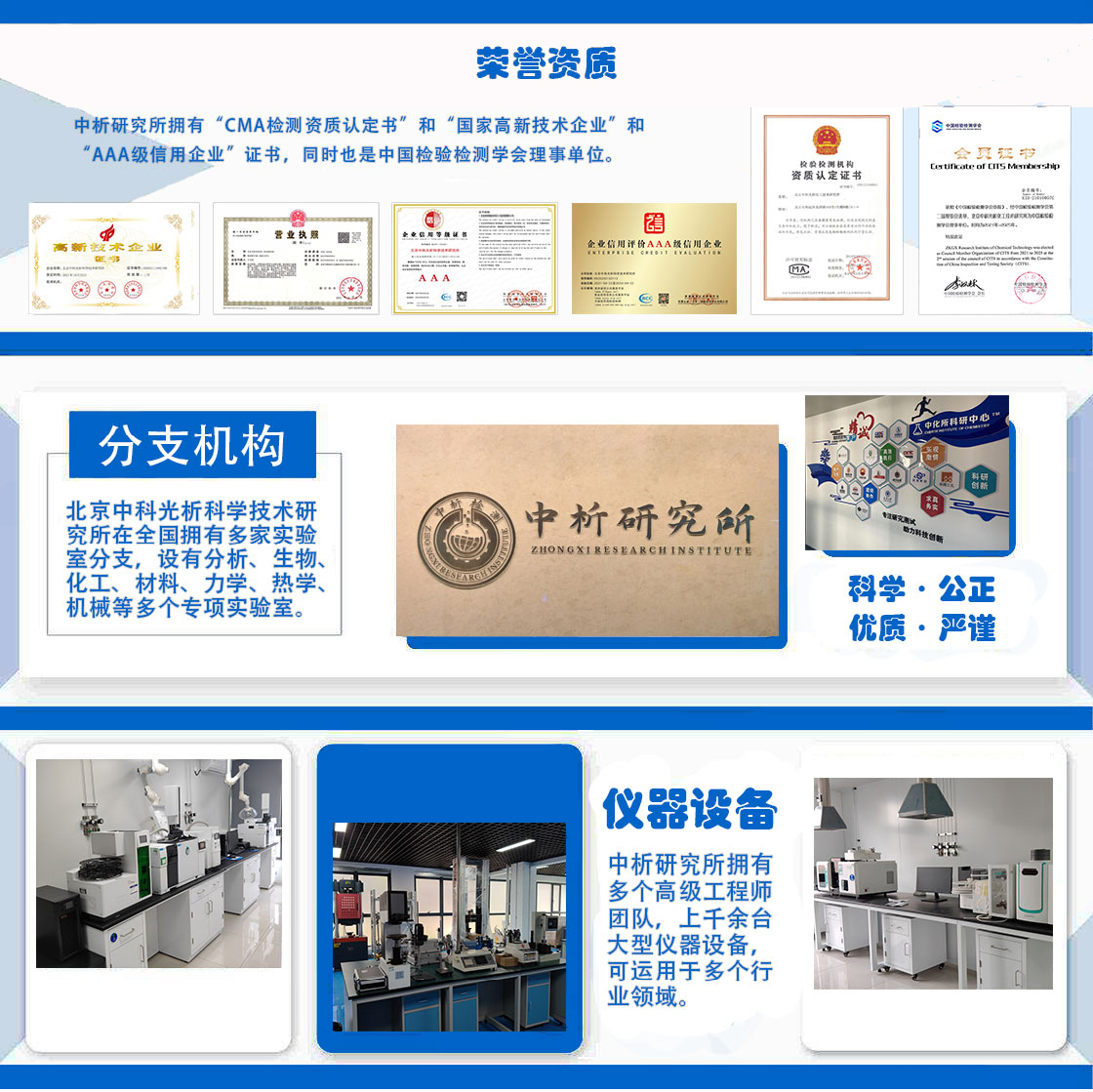
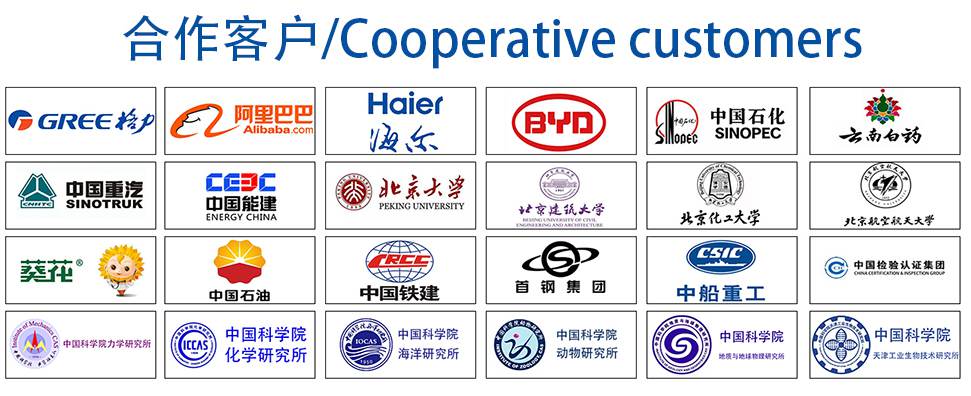
材料实验室
热门检测
推荐检测
联系电话
400-635-0567