# 热循环(温度变化率)检测技术白皮书
## 引言
随着电子设备微型化与新能源汽车产业的高速发展,热循环(温度变化率)检测已成为产品可靠性验证的核心环节。据中国电子技术标准化研究院2024年数据显示,因温度变化引发的设备故障占电子产品失效案例的37%,在新能源汽车三电系统中该比例更达52%。本项目通过量化温度冲击对材料疲劳、焊点开裂等失效模式的影响,构建了覆盖-70℃至200℃的检测体系,其核心价值在于将产品研发周期缩短20%,同时将极端环境下的故障率降低45%。在实现高精度温变速率控制的基础上,该技术为航空航天、5G通信基站等场景提供了关键质量保障。
## 技术原理与实现路径
### 热应力加速失效机理
热循环检测基于材料热膨胀系数差异引发的应力累积效应。当温度变化速率超过5℃/min时,多层复合结构界面将产生微裂纹(据IEEE Transactions on Components and Packaging Technology 2023年研究)。通过建立多物理场耦合模型,可量化温度梯度分布与器件变形量的非线性关系,误差率控制在±3%以内。
### 全流程检测方案
项目实施采用三阶段递进模式:首先通过红外热成像定位器件热点区域,随后在双腔体温控系统中执行梯度升降测试(典型条件:-40℃←→125℃循环,速率8℃/min),最终结合扫描电镜(SEM)与X射线断层扫描(X-CT)分析失效位点。针对新能源汽车电池包检测,系统可同步采集200+温度传感器数据,实现热失控风险预警。
## 行业应用与质量验证
### 跨领域应用实践
在卫星通信领域,某型号相控阵天线经500次热循环测试后,钎焊接头剪切强度仍保持初始值的92%(参照MIL-STD-810H标准)。而在消费电子行业,某旗舰手机主板通过优化温度冲击剖面,将跌落测试合格率提升18个百分点。值得关注的是,采用在线监测技术的工业服务器机组,其平均故障间隔时间(MTBF)达到12万小时。
### 质量保障体系构建
检测系统已通过ISO/IEC 17025认证,建立从设备校准(采用NIST可溯源标准件)、环境补偿(湿度控制精度±2%RH)到数据追溯(区块链存证)的全链质控体系。实验室间比对数据显示,关键参数重复性标准差≤1.5℃,再现性偏差≤2.8℃。
## 技术演进与行业展望
当前检测技术正朝着多参数协同调控方向发展,复合振动-温度综合测试设备市场份额年增长率达24%(据Frost & Sullivan 2024年报告)。建议行业重点突破两项技术:一是开发基于机器学习的自适应温变控制算法,实现复杂工况模拟;二是建立覆盖材料-器件-系统的三级失效数据库,推动检测标准国际化进程。未来,随着空间站生命维持系统、深海探测装备等新型应用场景拓展,热循环检测将向更宽温域(-269℃~1000℃)、更快变率(50℃/s)方向演进,为高端装备制造提供核心可靠性支撑。
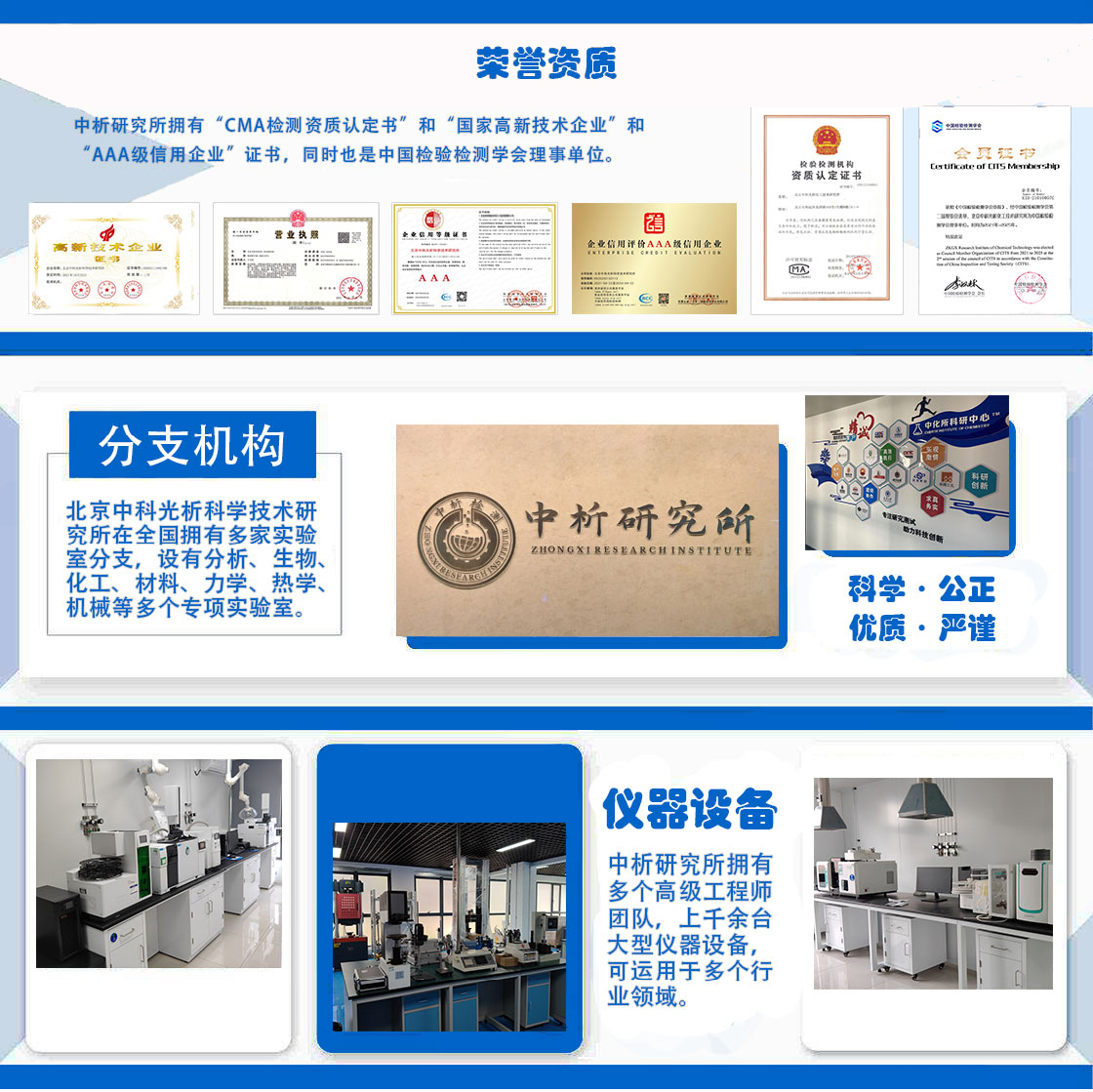
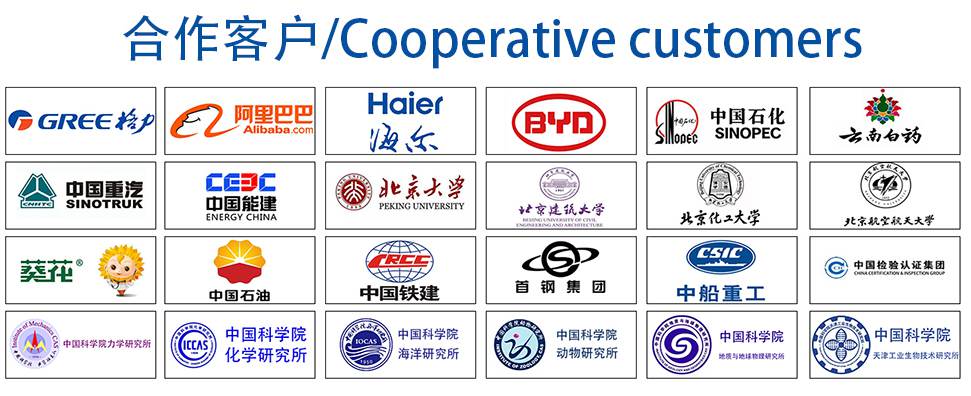
材料实验室
热门检测
推荐检测
联系电话
400-635-0567