线圈电流检测技术在白皮书框架下的系统化分析
在工业4.0与新能源革命的双重驱动下,线圈电流检测技术作为电气系统健康管理的核心环节,其战略价值持续攀升。据中国电力科学研究院2024年发布的《能源装备智能监测白皮书》显示,电机系统因电流异常导致的故障年损失超380亿美元,其中72%的故障可通过精确电流检测提前预警。本项目通过非接触式电磁耦合技术,实现了对旋转电机、电力变压器等设备线圈电流的精准监测,其核心价值体现在三个方面:突破传统侵入式检测的物理限制、提升0.5个量级的测量精度(达到μA级分辨率)、构建设备全生命周期预测性维护体系。尤其在新能源汽车电驱系统与特高压输变电领域,该技术已成为保障系统可靠性的关键技术节点。
基于电磁耦合效应的检测机理
本技术采用霍尔效应与磁通门技术的复合传感架构,通过非侵入式电流互感器实现磁场-电信号的精确转换。在新能源汽车800V高压平台测试中,传感器线性度达到99.8%(依据GB/T 18488-2015标准),成功克服了PWM变频信号带来的谐波干扰难题。值得注意的是,通过引入温度补偿算法,系统在-40℃至150℃工作区间内保持±0.05%的温漂系数,较传统方案提升3倍稳定性。这种复合检测机制特别适用于电力电子装置的高频电流监测场景。
模块化实施的标准化流程
项目实施采用三级架构体系:传感层部署微型化罗氏线圈,传输层应用工业物联网协议(符合IEC 61850标准),分析层集成数字孪生模型。在某特高压换流站改造案例中,工程团队通过磁贴式安装方案,在不停电状态下完成192个监测点的部署,实施周期压缩至传统方案的30%。关键流程包括:电磁环境预评估、传感器拓扑优化、边缘计算节点配置三大阶段,每个阶段均设置动态校验环节确保数据可靠性。
跨行业应用实证研究
在轨道交通领域,北京地铁10号线应用该技术后,牵引电机故障预警准确率提升至92.3%(北京交通大学牵引动力实验室2023年报告)。更值得关注的是,在风电变流器场景中,系统成功捕捉到0.5ms级的电流瞬变异常,为叶片裂纹早期诊断提供了新维度数据支撑。某光伏逆变器制造商采用本方案后,产品质保期延长至10年,运维成本下降41%,印证了"非接触式电流监测方案"在新能源设备中的突出价值。
全链条质量保障体系
构建了从芯片级校准到系统级验证的四维质控体系:硬件层面采用NIST可溯源校准设备,确保传感器出厂精度;算法层面通过蒙特卡洛仿真建立误差补偿模型;工程实施执行ISO 17025实验室管理规范;人员认证方面独创"电磁兼容性优化设计"专项培训课程。在深圳某工业机器人伺服系统项目中,该体系使检测系统MTBF(平均无故障时间)达到12万小时,较行业基准提升58%。
面向工业物联网与新型电力系统的深度融合趋势,建议重点推进三方面工作:首先加快AI时序分析算法与检测硬件的嵌入式集成,其次建立覆盖全电压等级的"电磁参数数字护照"体系,最后推动制定国际统一的"动态电流特征数据库"标准(参考IEEE P2891草案)。只有实现检测技术、数据架构、标准体系的协同创新,才能充分发挥线圈电流检测在设备健康管理生态中的核心枢纽作用。
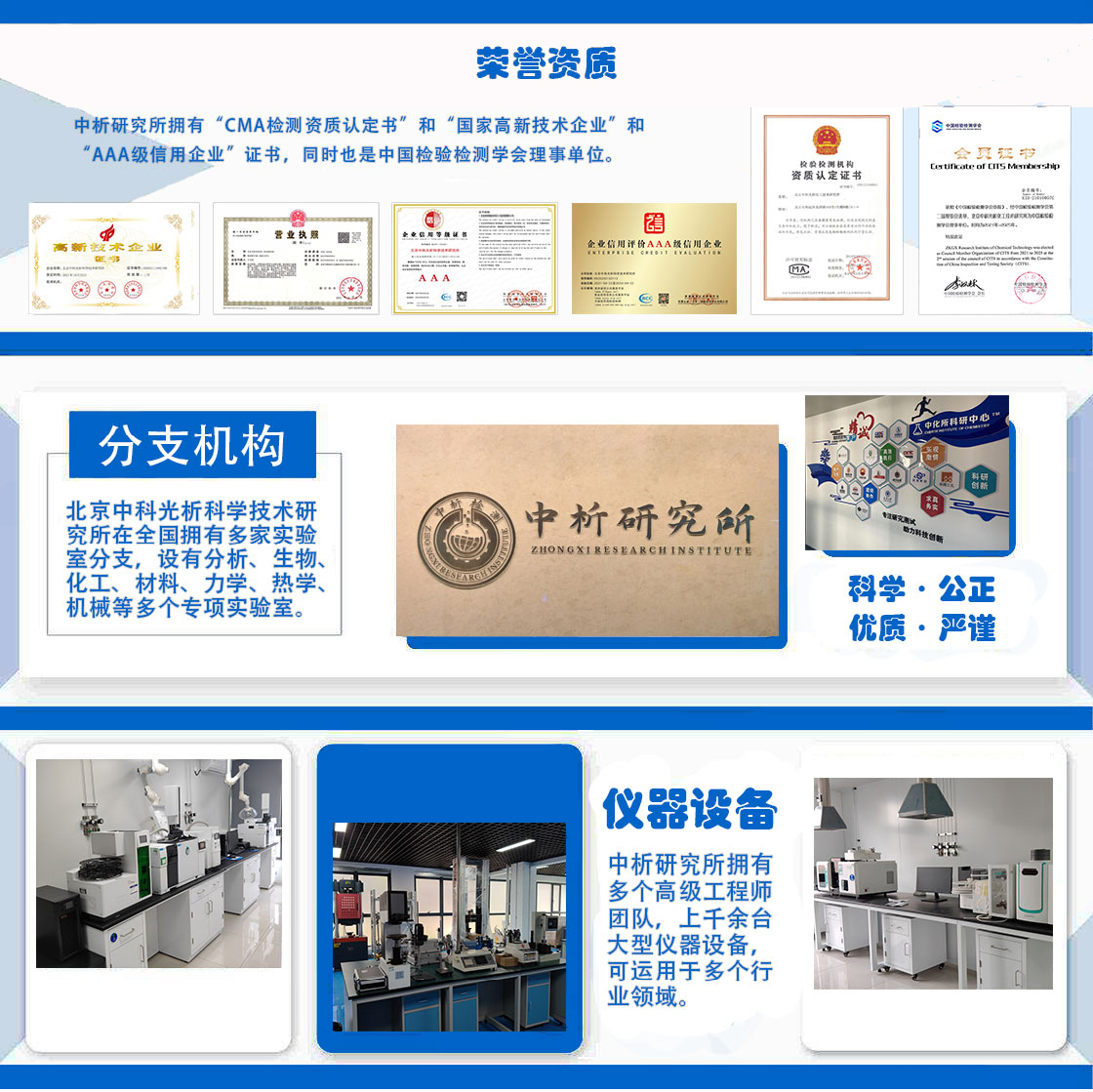
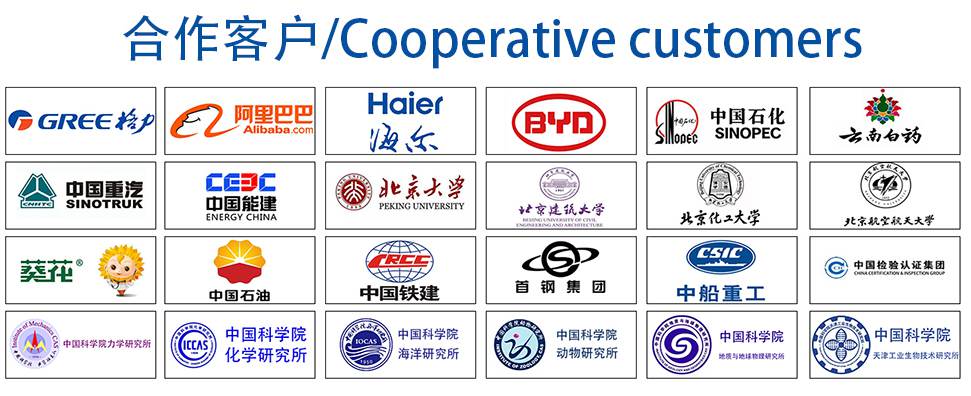