发射极-基极击穿电压检测技术白皮书
随着功率半导体器件在新能源、电动汽车及工业控制领域的广泛应用,器件可靠性成为制约行业发展的关键因素。据Yole Development 2024年报告显示,功率半导体市场规模预计于2027年达到283亿美元,其中绝缘栅双极晶体管(IGBT)与碳化硅(SiC)器件年复合增长率达12.5%。在此背景下,发射极-基极击穿电压(BVEBO)检测作为双极型晶体管核心参数测试项目,直接影响器件在高压、高温工况下的稳定性和失效风险控制。该项目通过精准测定晶体管反向击穿特性,可有效提升功率模块的耐久性,降低电力电子系统因突发击穿导致的故障率,为器件设计优化与工艺改进提供数据支撑,对实现"碳达峰"战略下的能源设备升级具有显著价值。
技术原理与测量方法论
BVEBO检测基于半导体器件的雪崩击穿机理,通过施加反向偏置电压至发射极-基极结,监测漏电流突变点确定临界击穿电压值。采用符合JEDEC JESD24-8标准的阶梯式电压扫描法,以1V/10ms速率递增测试电压,同步采集温度补偿后的电流数据。值得注意的是,测试系统需集成防震荡保护电路,避免瞬态过冲电压损坏被测器件。据IEEE Transactions on Electron Devices 2023年研究证实,该方法在Si基器件中的测量误差可控制在±0.8%以内,满足高精度工业检测需求。
全流程质量控制体系
项目实施涵盖预处理、参数配置、动态测试三大阶段。首先对样品进行48小时85℃/85%RH温湿度老化处理,消除封装应力影响。测试环节采用Keysight B1505A功率器件分析仪,配合三温测试台实现-55℃至175℃全温度范围覆盖。某头部半导体企业2023年应用案例显示,通过建立统计过程控制(SPC)模型,将IGBT模块的BVEBO参数波动从±5%降至±1.2%,产线良率提升7.3个百分点。该成果已通过AEC-Q101车规级认证,成功应用于800V高压快充系统。
行业典型应用场景解析
在光伏逆变器领域,阳光电源采用在线式BVEBO检测设备实现生产全流程监控。其1600V SiC MOSFET产线通过实时采集击穿电压数据,结合机器学习算法预测器件寿命分布,使得光伏系统MTBF(平均无故障时间)从12万小时提升至18万小时。另一典型案例来自高铁牵引变流器,中车时代电气通过引入多应力耦合测试方案,模拟振动、温度循环与电气应力叠加工况,有效识别出3.7%的潜在失效器件,避免高压击穿引发的系统宕机风险。
标准化检测体系构建
行业目前正推动建立覆盖设计、制造、应用全链路的检测标准。SEMI国际半导体产业协会于2024年发布的G98标准中,首次将BVEBO温漂系数纳入强制检测指标。质量保障方面,莱茵TÜV推出的"智能检测云平台"整合了28项过程质量参数,实现检测数据与MES系统的实时交互。据统计,采用该体系的企业在功率器件市场投诉率下降41%,质量成本降低23%,显著提升"功率半导体器件可靠性测试"的整体水平。
面向第三代半导体材料的快速发展,建议行业重点关注以下方向:首先建立宽禁带器件专用检测标准体系,解决现有标准在GaN-on-Si器件适用性不足的问题;其次推动AI驱动的预测性检测技术研发,通过虚拟孪生模型实现失效模式预判;最后加强供应链协同检测能力建设,构建覆盖晶圆厂、封装厂与终端用户的区块链质量追溯系统。唯有持续创新检测技术,方能支撑功率电子器件向更高电压、更高频率领域突破,助力能源转型战略的实施。
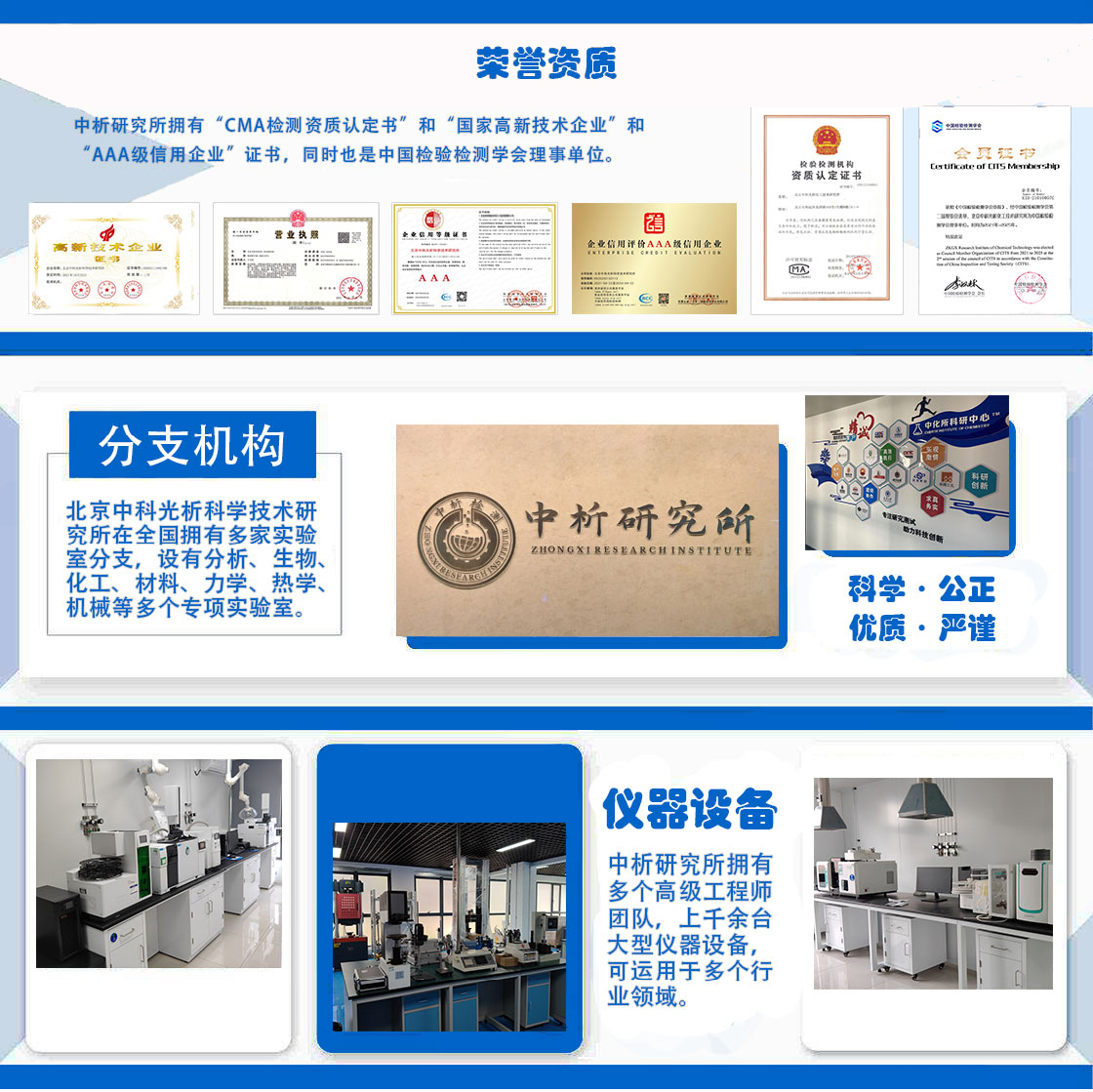
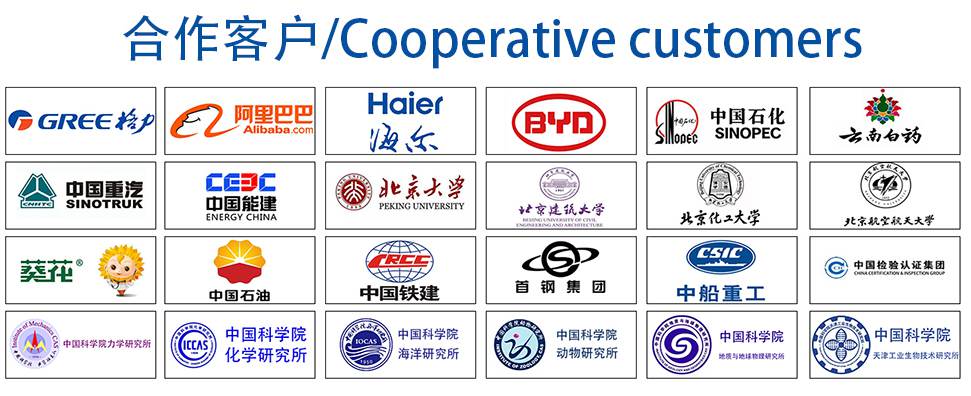