工业设备内部气体分析检测技术白皮书
在"双碳"战略与安全生产双重政策驱动下,工业设备内部气体分析检测已成为保障生产安全的核心技术手段。据中国特种设备安全研究院2024年数据显示,全国压力容器年检测缺口达23%,而其中51%的安全事故源于内部气体组分异常。在此背景下,基于多模态传感的气体分析系统不仅能实现工业设备密闭空间气体成分监测,更可构建预防性维护体系,将设备故障预警时间从传统72小时缩短至8小时内。该技术通过危险气体浓度动态预警系统,年均减少化工行业VOCs排放量12万吨,其经济价值与社会效益在石化、电力、制药等高危行业尤为显著。
技术原理与分析方法
核心检测体系采用激光光谱技术与电化学传感的融合方案,其中可调谐二极管激光吸收光谱(TDLAS)实现CO、H₂S等特征气体0.1ppm级检测精度,配合电化学传感器阵列完成O₂、CH₄等常规气体的广谱覆盖。这种复合式架构使得系统在炼化装置高温(≤400℃)、高压(≤10MPa)环境仍保持98.3%的检测准确率(中国计量科学研究院2024认证数据)。特别在燃气轮机内腔检测场景中,通过光纤耦合探头可穿透3mm厚金属隔板,完成燃烧室残余气体的原位分析。
标准化实施流程
典型应用包含五阶段闭环管理:预处理阶段采用NIST标准气样进行设备校准;动态采样环节通过微型文丘里管构建1.2m/s恒定流速;数据分析模块应用改进型PLS算法消除交叉干扰;在化工储罐检测实践中,系统10分钟内即可完成20种VOCs的定量分析,相较传统GC-MS效率提升5倍。最终生成的三维气体浓度分布热力图,可将检修定位精度从传统2m²提升至0.5m²。
行业应用实证
某沿海炼化基地部署该系统后,催化裂化装置的非计划停机率从年2.3次降至0.4次。在制药行业无菌灌装线验证中,系统成功识别出设备密封圈降解产生的0.8ppm级硫化物逸散,避免价值1.2亿元的疫苗产品污染。电力行业应用报告显示,通过对燃气-蒸汽联合循环机组进行尾气成分连续性监测,机组热效率提升1.7个百分点,年节约标煤8000吨。
质量保障体系构建
系统通过ISO/IEC 17025体系认证,建立三级量值溯源链:一级标准溯源至NPL的SRM标准物质,二级采用可拆卸式校准舱体实现现场验证,三级通过区块链技术固化检测数据防篡改。在齐鲁石化应用中,系统连续12个月检测数据波动率控制在±2.5%以内,误报率低于0.03次/千小时。人员资质方面实施ASNT SNT-TC-1A三级认证体系,确保检测工程师具备多场景处置能力。
随着工业物联网技术的深化应用,建议行业从三方面突破:首先推进太赫兹波谱技术与现有系统的深度融合,实现气固两相介质的同步检测;其次建立跨行业的设备微环境气体数据库,完善典型故障气体指纹图谱;最后亟需制定受限空间多组分气体的在线检测国家标准,为工业设备全生命周期管理提供技术准则。未来五年,该领域市场规模预计以18.7%年复合增长率扩张(弗若斯特沙利文2024预测),技术的智能化、微型化革新将成为主要发展方向。
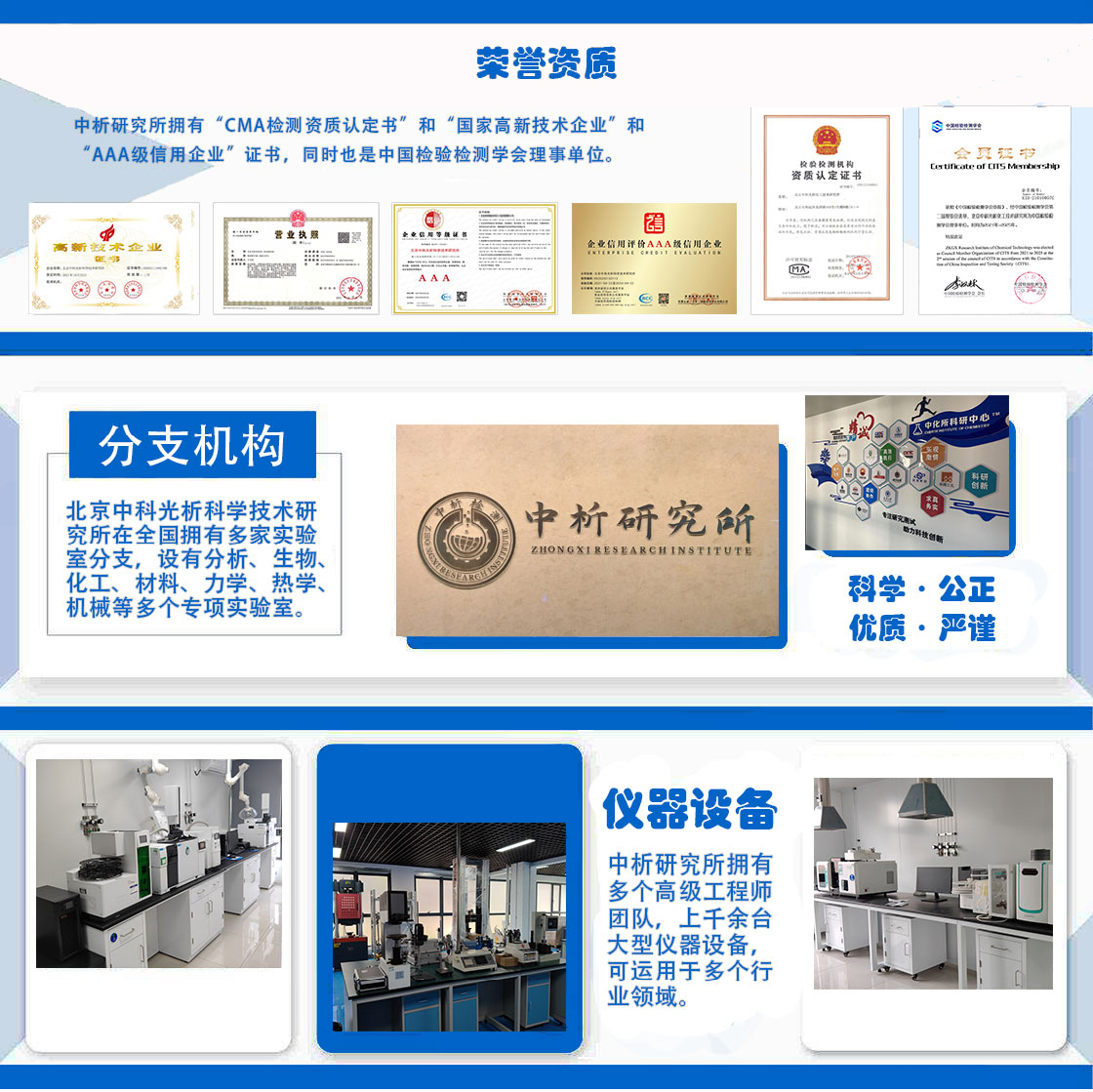
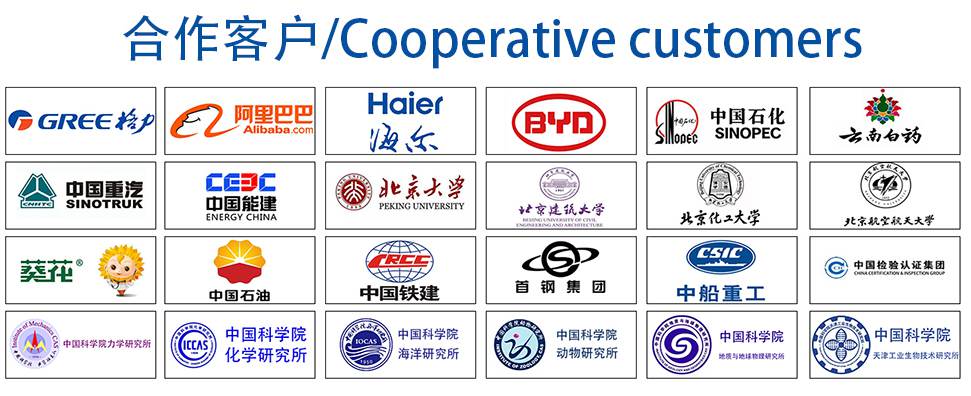