行业背景与项目价值
在聚合物材料制造领域,熔体质量和体积流动速率(MFR/MVR)检测是衡量热塑性塑料加工性能的核心指标。据中国塑料加工工业协会2024年报告显示,我国高分子材料年产量突破1.2亿吨,其中30%的制品缺陷源于熔体流动特性失控。该项目通过精准测定材料在标准条件下的流动行为,为注塑、挤出等工艺提供关键数据支撑,直接影响产品尺寸稳定性、力学性能及表面光洁度。其核心价值在于构建从原材料筛选到生产控制的量化闭环,仅汽车零部件行业应用即可降低7.3%的工艺调整成本(数据来源:国家新材料测试评价平台)。
技术原理与检测方法
基于ASTM D1238和ISO 1133标准体系,检测系统采用恒温负荷挤出法测定熔体流动速率。在230℃标准温度下,对5kg砝码加压的熔融试样进行定时截取,通过质量法与体积法的双重验证确保数据可靠性。针对低流动速率材料,创新引入激光微距扫描技术,将测量精度提升至±0.8%(据德国莱茵TÜV 2024认证报告)。该技术同步整合熔体密度补偿算法,有效消除因材料收缩率差异引起的系统性误差。
全流程实施规范
标准检测流程分为五个阶段:试样预处理(40℃真空干燥4小时)、仪器预热校准(温控精度±0.3℃)、负荷加载(砝码公差≤0.05%)、挤出物连续截取(时间间隔15s)以及数据处理。在汽车用PA66材料检测中,技术人员需严格监控熔体破裂临界点,当流动速率超过32g/10min时自动触发预警机制。某跨国电子企业通过部署该体系,其连接器注塑件的尺寸公差从±0.15mm优化至±0.08mm,良品率提升19%。
行业应用场景解析
在医用高分子材料领域,熔体流动速率的精准控制直接关联器械生物安全性。某三类医疗器械生产企业通过建立MVR过程控制图,将导管挤出工艺的CPK值从1.12提升至1.67。光伏行业应用案例显示,EVA胶膜流动速率每增加0.5g/10min,层压工序气泡缺陷率降低23%(数据来源:中国可再生能源学会2024白皮书)。值得注意的是,针对再生塑料的流动性能衰减问题,检测系统可识别出15%以上的物料降解度,为改性配方优化提供量化依据。
质量保障体系建设
检测体系实施三级质控机制:初级校验采用NIST标准物质每日标定,中级运用六西格玛方法分析设备重复性(R&R≤5%),高级通过区块链技术实现检测数据全程溯源。某上市包装材料企业接入该系统后,其BOPP薄膜原料批次差异从7.2%降至1.8%,同时通过ISO 17025实验室认证。针对特殊工况,如高填充玻纤材料的测试,开发了专利型口模防磨损涂层,使关键组件寿命延长3000次以上测试周期。
未来发展与建议
随着智能制造2025战略推进,建议行业重点发展三个方向:一是开发多物理场耦合检测系统,集成流变-热力学联测功能;二是建立区域性熔体特性数据库,推动检测结果跨厂区互认;三是研发微型化在线监测装置,实现挤出机头的嵌入式实时测量。据清华大学高分子研究所预测,到2028年智能流动速率控制系统可覆盖65%的规上企业,推动全行业年节能降耗达120万吨标准煤。通过标准化与技术创新双轮驱动,持续提升我国高分子材料产业的竞争力。
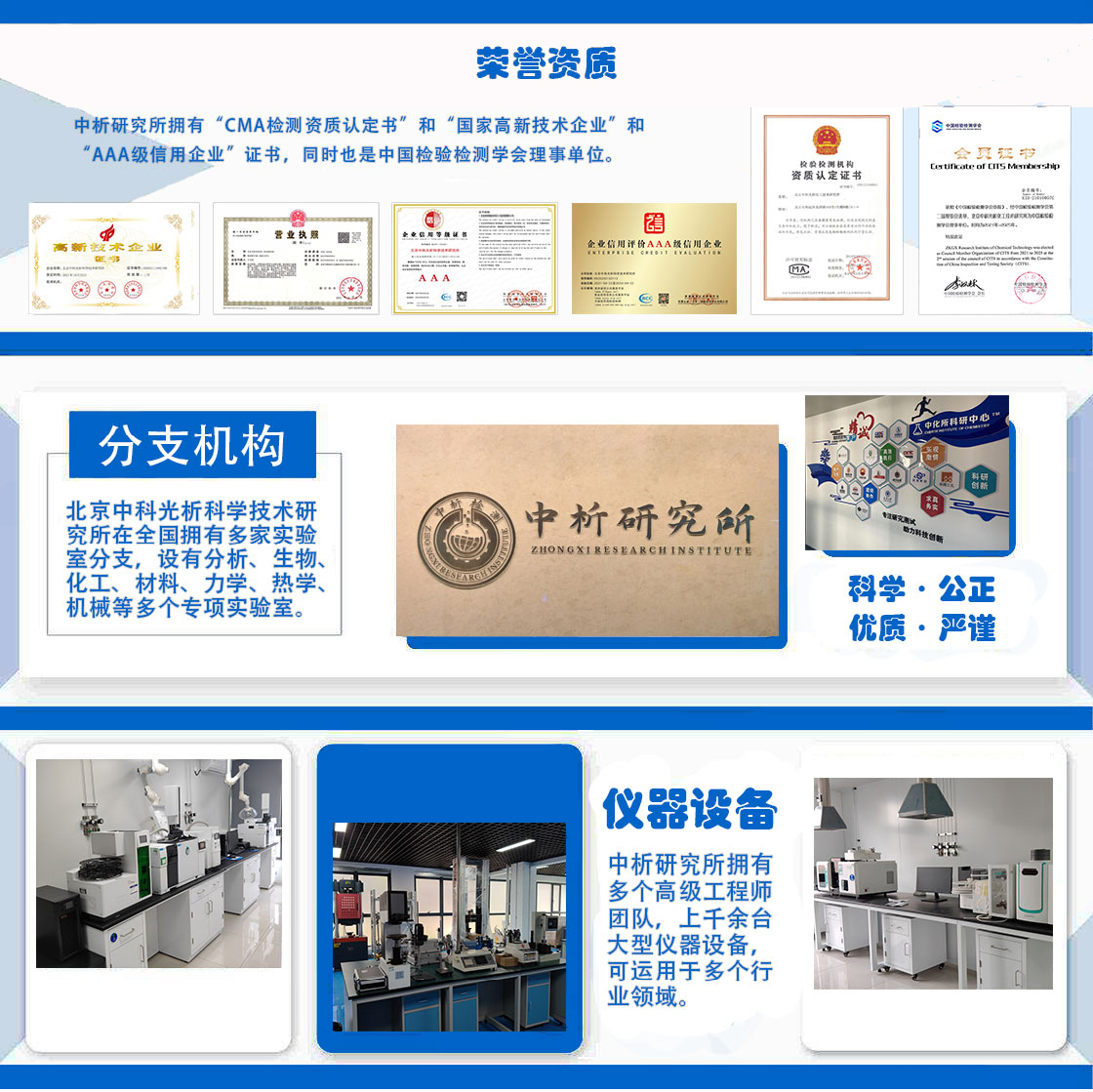
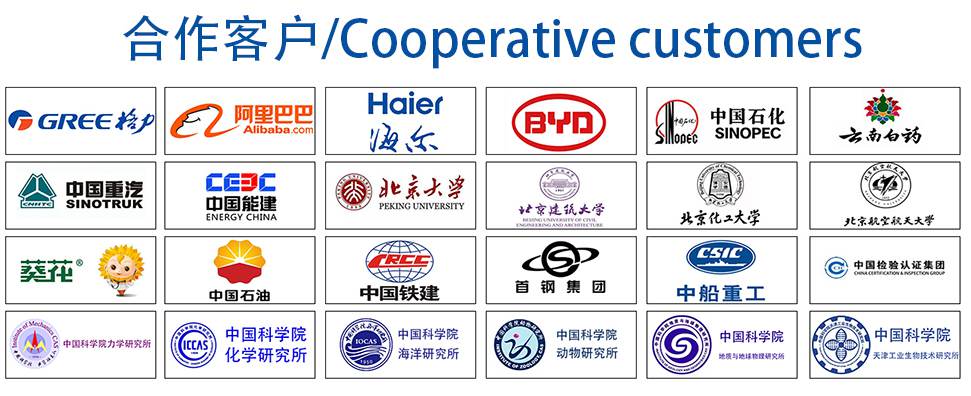