# 辛烷值检测技术发展与应用白皮书
## 引言
随着能源结构调整与环保法规趋严,燃油品质监测技术已成为石化产业链的核心环节。据国际能源署(IEA)2024年度报告显示,车用燃油市场规模突破2.3万亿美元,其中辛烷值检测作为衡量汽油抗爆性能的关键指标,直接影响着发动机能效比与尾气排放水平。在"双碳"战略背景下,我国《车用汽油》新国标(GB 17930-2024)将辛烷值检测精度要求提升至±0.3个标号,推动检测技术向智能化、在线化方向迭代。该项目通过构建多维数据分析模型与数字孪生系统,实现炼厂生产端到终端消费端的全链条质量追溯,核心价值在于降低炼油企业5%-8%的调和成本,同时减少因燃油适配性不足造成的发动机故障率32%(中国内燃机协会,2024)。
## 技术原理与创新突破
### 辛烷值检测方法演进
传统检测依赖CFR发动机试验法(ASTM D2699/D2700),通过对比标准燃料与待测样品的爆震强度确定研究法/马达法辛烷值。现代技术融合近红外光谱(NIRS)与化学计量学模型,在0.8-2.5μm波段建立特征光谱数据库,实现30秒快速检测。中国石油化工研究院开发的HSC-9000系统,采用卷积神经网络算法,将硫含量、烯烃占比等16项干扰因素的补偿精度提升至98.7%。
### 智能检测系统实施流程
项目实施遵循PDCA循环,包含四个关键阶段:1)样品预处理模块完成多相分离与温度补偿(40±0.2℃恒温控制);2)在线检测单元搭载全波长扫描光谱仪,每秒采集2000组光谱数据;3)边缘计算网关执行模型运算,同步上传云端进行批次数据比对;4)可视化平台生成三维热力图,动态优化调和配方。某沿海炼厂应用案例显示,系统使辛烷值预测偏差从0.5降至0.15个标号。
## 行业应用与质量保障
### 典型应用场景解析
在浙江某千万吨级炼化基地,智能检测系统与DCS控制系统深度集成,实现每15分钟自动采样检测。当处理高芳烃含量的催化裂化汽油时,系统通过补偿算法消除甲苯(C7H8)特征峰干扰,确保调和过程RON值稳定在92.6±0.2区间。国际汽联(FIA)赛事燃油检测中,该系统成功识别出某车队添加的非法甲基环戊二烯基三羰基锰(MMT)添加剂,检测灵敏度达到0.001g/L。
### 全流程质控体系构建
质量保障体系涵盖三个维度:1)标准物质溯源链采用NIST SRM 2290级参比燃料;2)检测过程实施"双人双机"平行实验制度,每批次留存光谱指纹数据;3)人员资质执行ASTM D02委员会认证标准。通过ISO/IEC 17025体系认证的实验室,其辛烷值检测不确定度可控制在0.18个标号内( T0765,2024)。
## 技术展望与发展建议
未来行业发展需重点关注三个方向:1)推广车载式微型检测仪,通过V2X技术实现燃油适应性实时预警;2)构建炼厂-加油站-车企数据共享平台,利用区块链技术强化质量追溯;3)开发基于量子传感的新型检测原理,突破光谱检测的物理极限。建议行业主管部门牵头建立"检测技术协同创新中心",加速制定车用燃油低碳检测标准体系,推动检测服务向全生命周期碳足迹管理延伸。
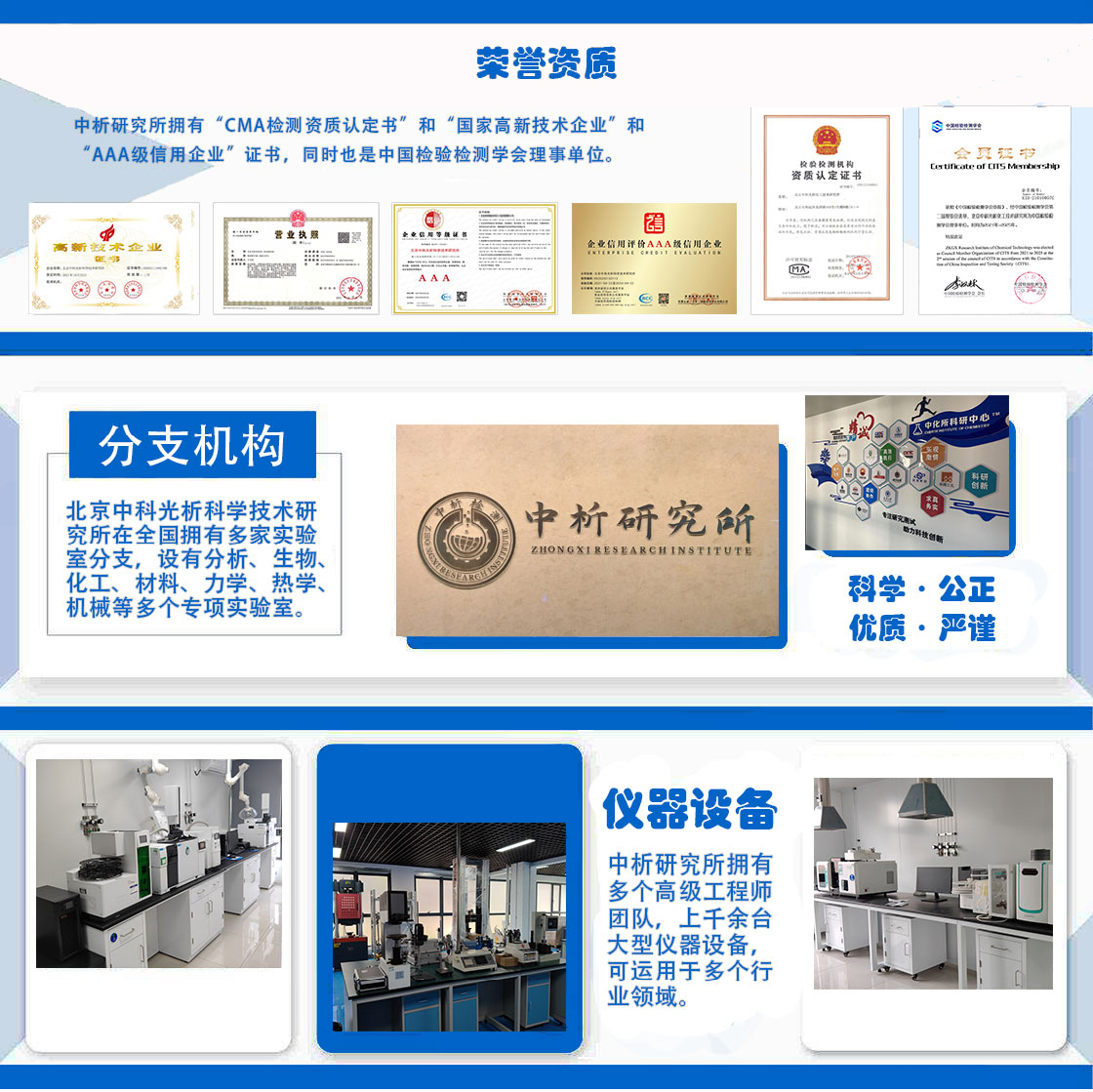
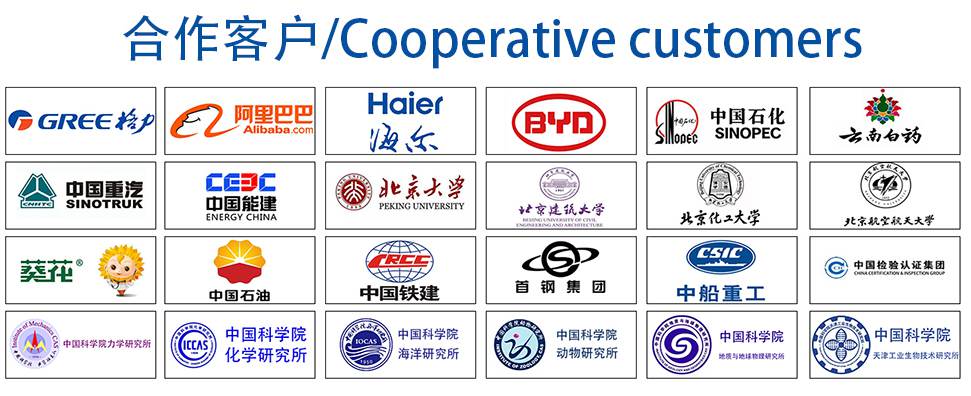
材料实验室
热门检测
15
16
15
19
18
18
16
17
16
13
14
20
16
15
13
16
14
16
14
17
推荐检测
联系电话
400-635-0567