减压馏程检测在石化行业中的关键作用与技术发展
随着能源结构转型加速,炼油行业对工艺优化和产品质量控制的需求日益迫切。减压馏程检测作为石油产品分析的核心技术,能够精准测定重质油品在不同压力下的馏分组成,为催化裂化、润滑油生产等关键工艺提供数据支撑。据中国石化研究院2024年数据显示,采用标准化减压馏程检测的炼化企业,其重油加工效率平均提升12.7%,设备结焦率下降18.3%。该技术不仅实现了资源高效利用,更通过构建馏程特征数据库推动工艺数字化升级,其核心价值体现在质量溯源、能耗优化和环保合规三大维度,已成为现代炼厂智能化转型的必备技术手段。
基于压力调控的分离机理
减压馏程检测依托物理分离原理,通过建立0.1-10kPa的梯度真空环境,使高沸点组分在低温条件下完成相态转变。采用ASTM D1160标准方法,系统可获取初馏点、5%馏出温度及终馏点等关键参数。值得关注的是,新一代在线减压馏程分析仪通过集成微型真空泵组和红外光谱检测模块,将单次检测耗时从传统4小时缩短至40分钟。据国家能源局2023年技术白皮书披露,这种实时监测能力使延迟焦化装置的轻油收率提升了2.3个百分点。
全流程标准化操作体系
典型检测流程涵盖样品预处理、设备校准、压力程序设定等7个关键环节。在山东某千万吨级炼油厂的实际操作中,技术人员需将油样加热至150℃后注入带有陶瓷填料的蒸馏柱,通过PID控制器将真空度稳定在±0.5kPa范围内。为应对渣油乳化问题,部分企业开始应用超声破乳预处理工艺,使检测重复性标准差从1.8℃降至0.6℃。该体系已通过ISO 9001认证,并配备三级数据校验机制确保结果可靠性。
跨领域应用场景拓展
除传统炼油领域外,减压馏程检测在煤化工和生物燃料行业展现出独特价值。宁夏某煤制油企业通过建立减压馏程-黏度关联模型,成功优化了费托合成产物的分馏切割点,使柴油馏分收率提高5.2%。在废弃油脂转化生物柴油领域,该技术可快速识别甘油三酯分解程度,据广州能源检测中心案例显示,基于馏程数据的工艺调整使产物甲酯纯度达到99.3%的行业新高。
四维质量保障架构
行业领先企业已构建覆盖设备、人员、方法和环境的立体质控网络。上海某第三方检测机构采用溯源性温控系统,其铂电阻传感器定期送检中国计量科学研究院,温度测量不确定度控制在±0.1℃。人员资质方面要求操作员必须通过减压蒸馏专项技能认证,并每季度参与盲样比对测试。在浙江某炼化基地,通过引入环境振动补偿算法,成功将外界干扰导致的馏程偏差降低62%。
面对双碳目标带来的技术挑战,建议行业从三方面深化发展:首先加快开发基于机器视觉的智能馏程终点判定系统,其次推动ASTM与SH/T标准的国际互认进程,最后应建立减压馏程数据与碳排放核算的联动模型。未来随着5G边缘计算技术的应用,分布式减压馏程监测网络有望实现炼化全流程的实时闭环优化,为行业高质量发展注入新动能。
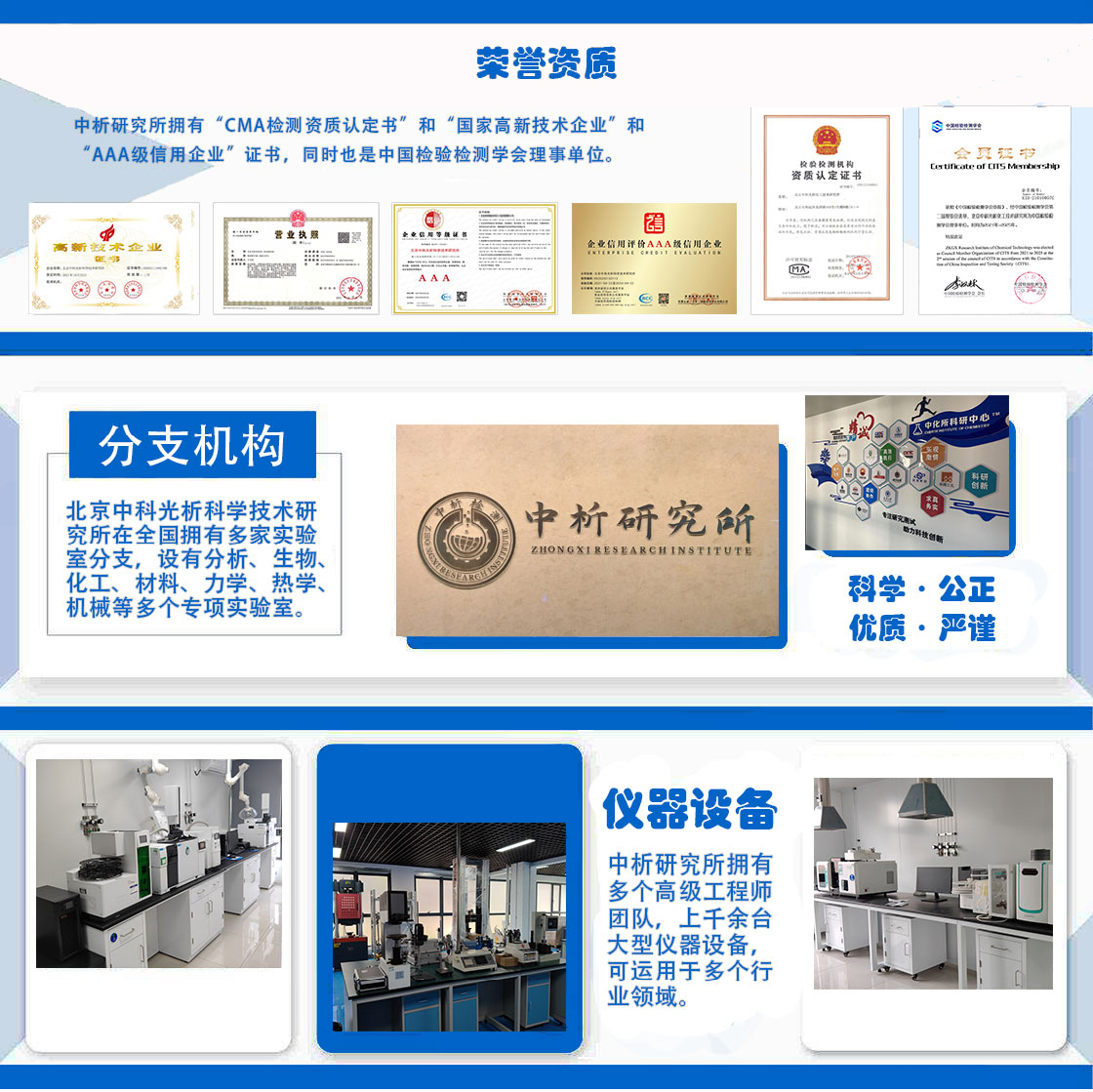
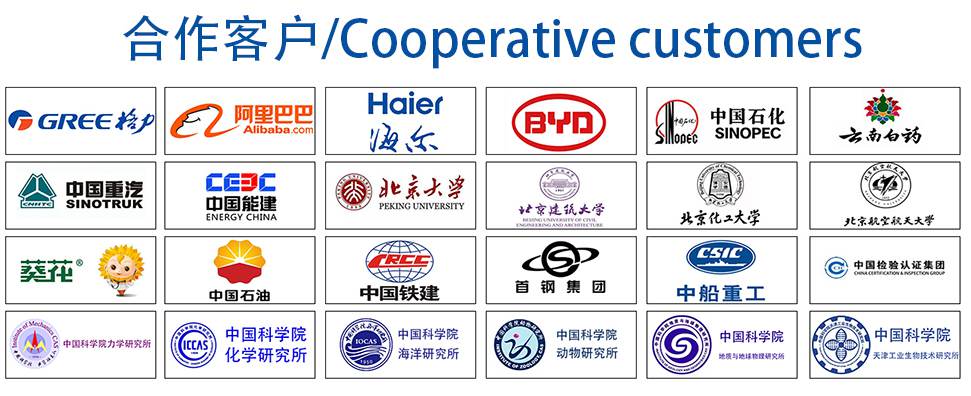