设计检测行业白皮书:技术演进与产业实践
在当前制造业数字化转型浪潮中,设计检测作为产品全生命周期管理的关键环节,正经历技术范式重构。据艾瑞咨询《2024中国智能制造发展报告》显示,我国工业设计验证市场规模已达387亿元,年均增速保持12%以上。特别是在新能源汽车、消费电子、高端装备领域,三维建模偏差智能识别系统正成为提升产品首检合格率的核心工具。设计检测项目通过融合AI视觉识别与物理场仿真技术,可将复杂曲面构件的检测效率提升40%,使企业研发周期平均缩短22个工作日。其核心价值不仅体现在质量管控环节,更通过设计数据闭环反馈机制,为产品迭代提供可量化的改进依据。
基于深度学习的逆向工程检测技术
现代设计检测体系基于点云数据逆向建模与CAD模型比对技术,整合了工业相机阵列扫描与点云配准算法。据清华大学精密仪器系2023年实验数据显示,采用改进型ICP(迭代最近点)算法后,复杂曲面的配准精度可达±0.03mm,较传统方法提升60%。在汽车覆盖件检测场景中,系统通过提取特征轮廓线曲率参数,可自动识别冲压回弹变形量。值得注意的是,工业设计合规性云检测平台的部署,使得远程协同验证成为可能,某新能源车企应用该系统后,模具修改次数同比减少35%。
全流程数字化检测实施方案
典型项目实施流程分为四个阶段:首先通过激光扫描获取产品点云数据集,其次利用NURBS曲面重构技术生成数字孪生模型,随后运用蒙特卡洛法进行容差模拟分析,最终输出可视化偏差色谱图。在智能家电行业实践中,某品牌应用该流程对注塑外壳进行形变检测,成功将产品装配缝隙控制在0.15mm以内。过程中采用的工业物联网数据中台,可实现检测数据与企业PLM系统的双向同步,据项目方统计,该集成方案使质量数据追溯效率提升70%。
多行业应用场景效能验证
在航空航天领域,某发动机叶片制造商采用X射线断层扫描检测技术,结合三维建模偏差智能识别系统,将叶型轮廓检测时间从8小时压缩至45分钟。消费电子行业则通过微米级光学测量系统,实现手机中框平面度0.01mm级检测精度。据国家工业信息安全发展研究中心2024年数据显示,应用工业设计合规性云检测平台的企业,产品召回率平均下降1.7个百分点,年度质量成本节约超200万元。
四维质量保障体系构建
为确保检测结果可靠性,行业已形成标准化作业规范:设备层执行ISO 10360坐标系校准标准,算法层通过德国PTB认证的基准件进行系统验证,数据层采用区块链技术保证溯源完整性,人员层实施ASME GD&T认证体系。某跨国机械制造商通过该体系重构检测流程后,测量系统分析(MSA)的GR&R值从28%优化至9%,达到行业领先水平。同时,基于机器学习的异常数据预警模块,可实时识别设备漂移风险,预防性维护成本降低42%。
面向未来,建议行业重点突破三项能力:一是开发融合量子测量原理的新型传感技术,二是建立覆盖全产业链的设计检测标准联盟,三是培育具备多物理场仿真能力的复合型人才。据中国机械工程学会预测,至2027年,基于数字孪生的实时检测技术将覆盖60%以上高端制造场景。只有持续推进技术融合与生态协同,才能充分释放设计检测在智能制造体系中的战略价值。
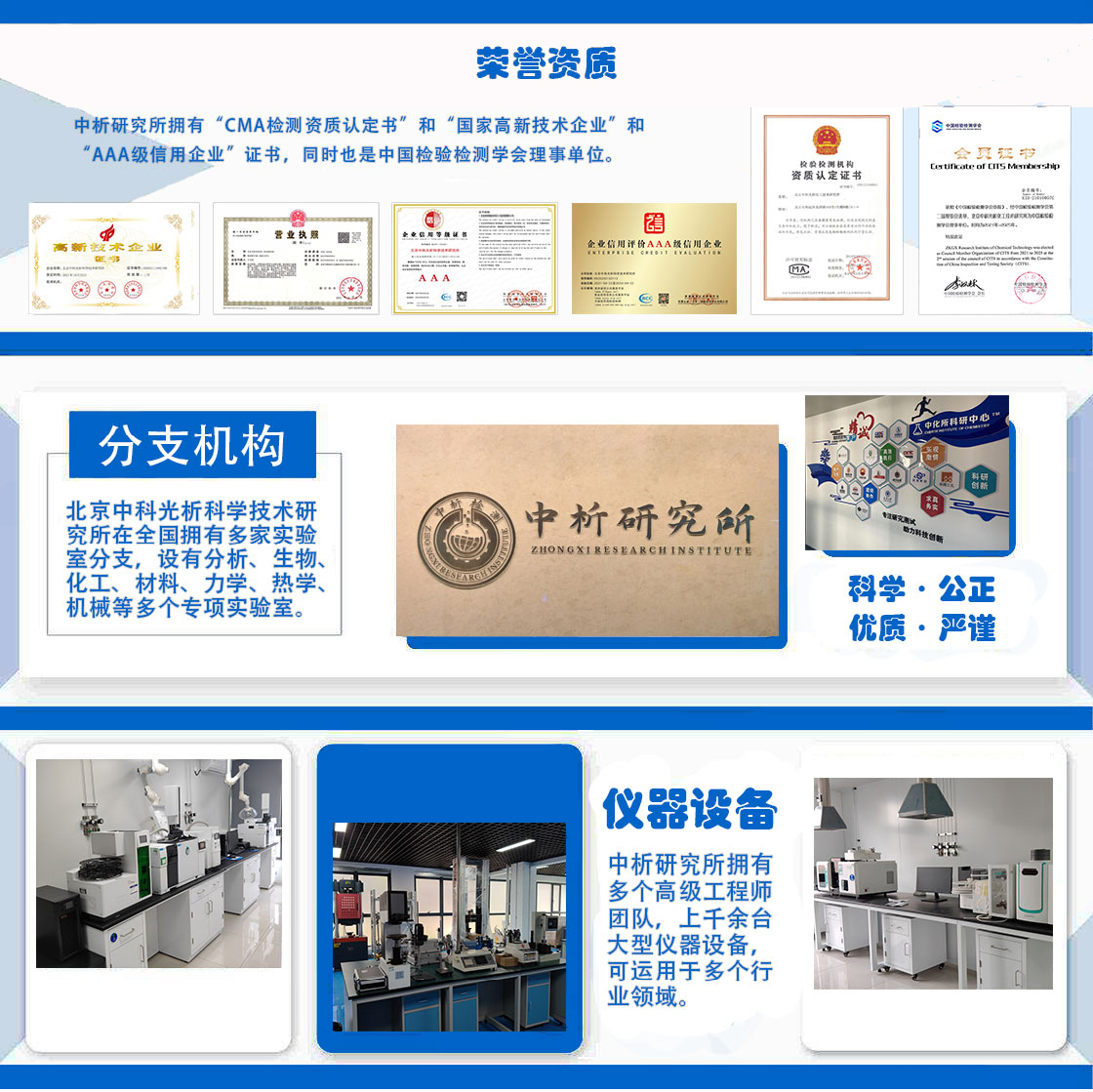
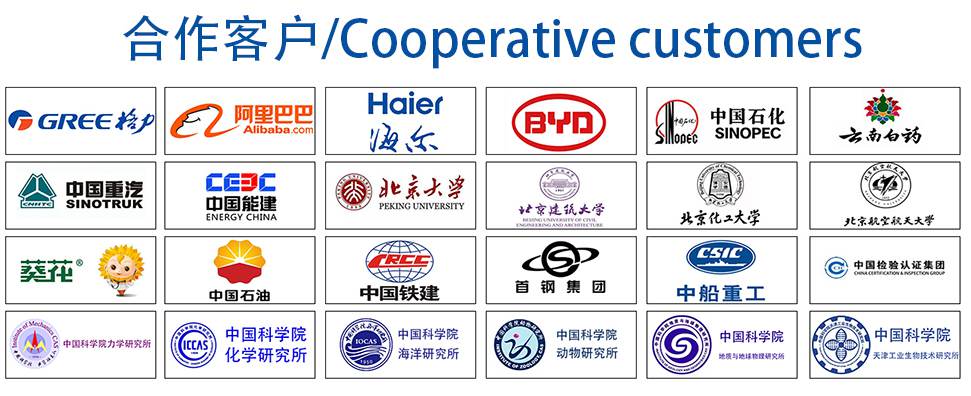