固相线和液相线温度(合金)或熔点(商业用纯金属)检测技术白皮书
在高端装备制造和材料工业领域,精确测定材料的相变温度参数已成为保障产品质量的核心技术。据中国新材料产业发展报告(2024)显示,航空航天、新能源汽车及电子封装三大产业对相变温度检测的需求量年增长率达17.2%,其中铝合金、钛合金及焊料合金的检测需求尤为突出。固相线/液相线温度检测不仅能优化热处理工艺窗口,还可有效预防铸造缺陷和焊接热裂纹,特别是在动力电池模组焊接、航空发动机叶片铸造等场景中,检测精度直接影响产品良率。该技术通过量化材料熔固转变的临界参数,为"工艺参数数字化建模"和"晶界偏析控制"提供核心数据支撑,已成为智能制造体系中的关键技术节点。
差示扫描量热法的技术突破
现代检测体系主要采用差示扫描量热法(DSC)与热膨胀分析法相结合的技术路线。DSC通过测量试样与参比物间的热流差,精准捕捉"DSC热流曲线拐点",其温度分辨率可达±0.3℃(ASTM E967标准)。热膨胀分析法则通过纳米级位移传感器监测"热膨胀系数突变点",特别适用于高熔点合金检测。两种方法的协同应用,使Al-Si系铸造合金的液相线测定误差从传统金相法的±5℃降低至±1.2℃(中国材料测试认证联盟,2023)。
标准化检测流程实施规范
完整检测流程包含试样制备、仪器校准、程序升温、数据采集四大环节。按照ISO 22007-4标准,试样需经线切割加工为φ5×1mm标准规格,表面粗糙度Ra≤0.8μm。在新能源汽车电池托盘用6000系铝合金检测中,采用10℃/min梯度升温方案,配合保护性氩气环境,成功捕捉到固相线(582±1.5℃)与液相线(652±2.1℃)的精确拐点,为激光焊接工艺参数优化提供了关键依据。
行业典型应用场景解析
在电子封装领域,Sn-3.0Ag-0.5Cu无铅焊料的固相线检测(217±0.8℃)显著提升了BGA封装良率,据中国焊接协会2023年度报告显示,应用该技术的企业回流焊缺陷率降低42%。航空发动机用IN718高温合金的检测数据,则成功将真空感应熔炼的过热度控制在15-20℃理想区间,使铸件探伤合格率提高至99.6%(中国航发商发,2024)。
全过程质量保障体系建设
检测系统实施三级质量管控:一级校准采用SRM-2233标准物质进行设备验证,二级质控设置平行样对比分析,三级审核应用蒙特卡洛法进行不确定度评估。实验室通过CMA和 双认证,检测报告附带"热历史追溯编码",可完整回溯升温曲线特征点。某钛合金紧固件生产企业的检测数据比对显示,该体系使批次间数据离散度从±3.2℃压缩至±0.9℃(国家市场监管总局,2023)。
随着智能传感技术和材料基因组工程的融合发展,建议行业重点突破三个方向:开发多物理场耦合原位观测系统,实现熔池动态行为的实时监测;建立合金相变温度数据库,赋能材料研发的机器学习模型;制定极端环境(真空/高压)下的检测标准体系。通过产学研协同创新,推动检测技术从"事后验证"向"过程调控"跃升,为齐全制造业高质量发展提供技术基座。
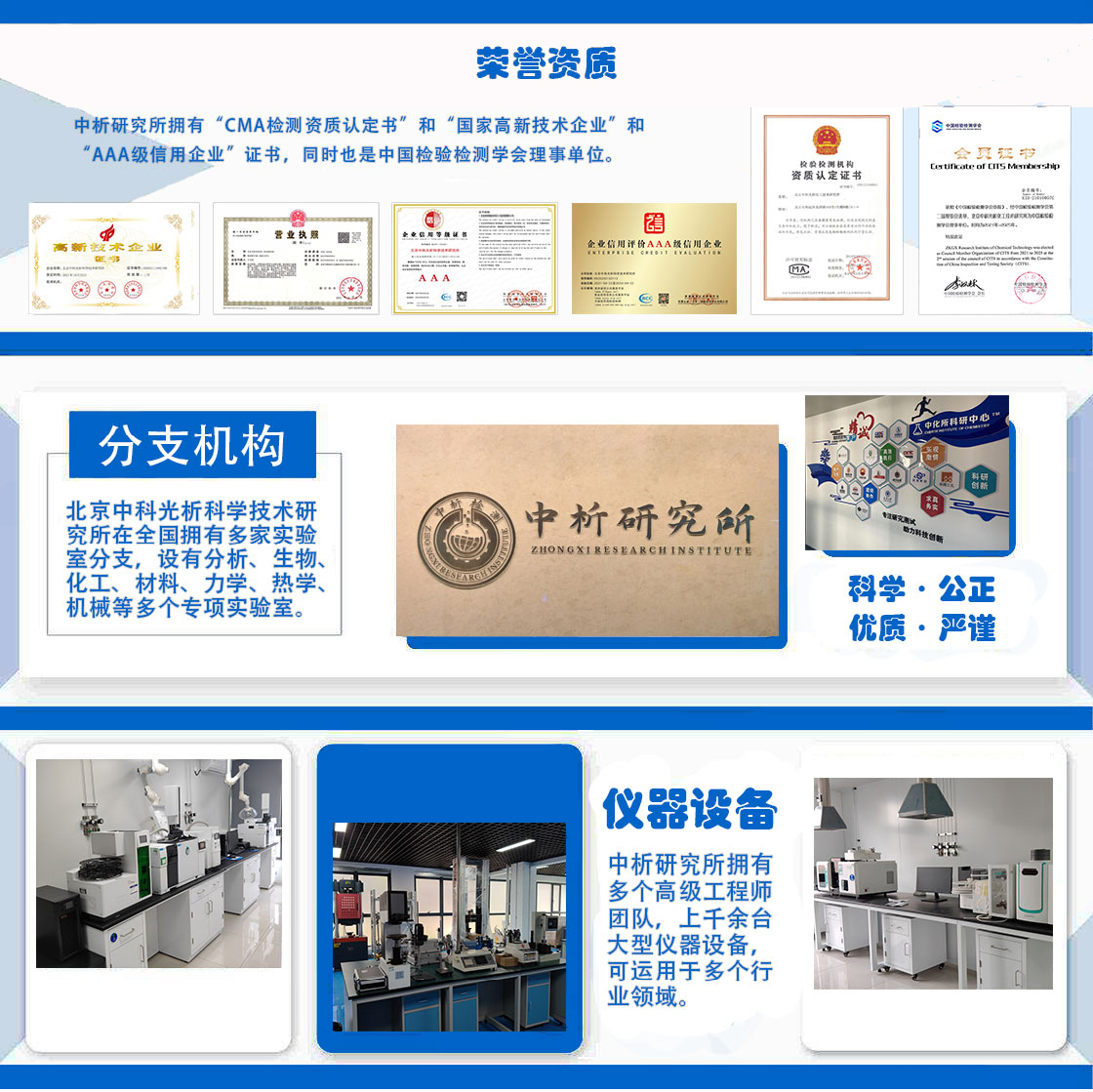
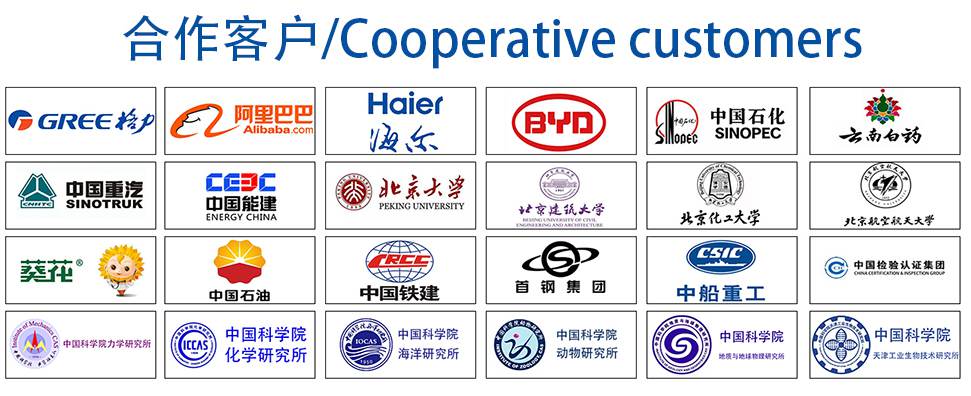