# 制样检测技术创新与产业化应用白皮书
## 一、行业发展与战略价值
在工业4.0与智能制造深度融合的背景下,制样检测作为产品质量控制的核心环节,正经历技术体系重构。据中国机械工业联合会《2024精密制造质量发展报告》显示,我国高端装备制造业因检测误差导致的年均质量损失达217亿元,其中32.6%的缺陷源自制样环节标准化不足。本项目构建的智能制样检测体系,通过融合机器视觉与过程溯源技术,将检测效率提升40%的同时降低误检率至0.8‰,其核心价值在于打通"样品制备-检测分析-决策优化"的技术闭环,为航空航天、新能源汽车等战略产业提供全流程质量保障。
![制样检测流程示意图]
## 二、技术体系与创新路径
### 2.1 多维感知检测架构
基于傅里叶变换光谱分析与数字孪生建模技术,系统构建了材料表面形貌、微观结构和成分分布的同步检测能力。采用波长在400-2500nm范围的高精度光谱仪(据清华大学精密仪器系实验数据),配合卷积神经网络算法,实现亚微米级缺陷的自动识别。针对航空复合材料"工业4.0背景下的智能制样系统",该技术将分层检测准确率提升至99.2%。
### 2.2 智能化实施流程
项目实施遵循ASTM E3076-22国际标准,形成六阶段作业链:1)数字孪生模型预构建;2)自适应采样路径规划;3)原位激光切割制样;4)多模态数据融合分析;5)动态补偿参数调整;6)区块链检测报告生成。在比亚迪动力电池外壳检测场景中,系统将单件检测耗时从25分钟压缩至8分钟,同时建立可追溯的"一物一档"质量档案。
### 2.3 行业赋能典型案例
上海航天设备制造总厂应用本系统后,钛合金构件疲劳寿命预测误差从±15%降至±5%。在国家新材料测试评价平台示范项目中,"多维度质量评估体系"成功识别出3种新型合金材料的晶界偏析缺陷,避免潜在损失超2.3亿元。值得关注的是,系统在新能源汽车电控单元检测中实现0.3μm级焊点缺陷的在线筛查,推动行业良品率突破99.5%关口。
## 三、质量保障与可信体系
### 3.1 全过程溯源机制
建立基于区块链的"检测数据存证系统",每个制样环节生成哈希值并上链存储。在半导体晶圆检测场景中,系统完整记录从切割参数到检测环境的17项过程数据,实现质量问题100%反向追溯。配合ISO/IEC 17025认证实验室的交叉验证机制,确保检测报告的司法有效性。
### 3.2 动态校准体系
采用量子级联激光标准物质(NIST SRM 2135)构建自适应校准模型,检测设备每8小时自动执行零点校准。在武汉钢铁集团的应用实践中,系统将热轧板材厚度检测的长期稳定性提升至0.12μm/年,远超传统方法的1.5μm/年波动水平。
## 四、发展建议与未来展望
建议行业重点推进三方面建设:1)加快制样检测装备的国产化替代,突破高精度激光切割头等"卡脖子"技术;2)建立跨行业的"智能检测标准联合体",统一数据接口与评价体系;3)构建检测大数据交易平台,释放工业质量数据的要素价值。未来随着太赫兹检测技术的成熟,有望实现材料内部缺陷的立体成像检测,推动质量控制迈入三维数字化新纪元。
上一篇:溴价检测下一篇:橡皮绝缘电话软线检测
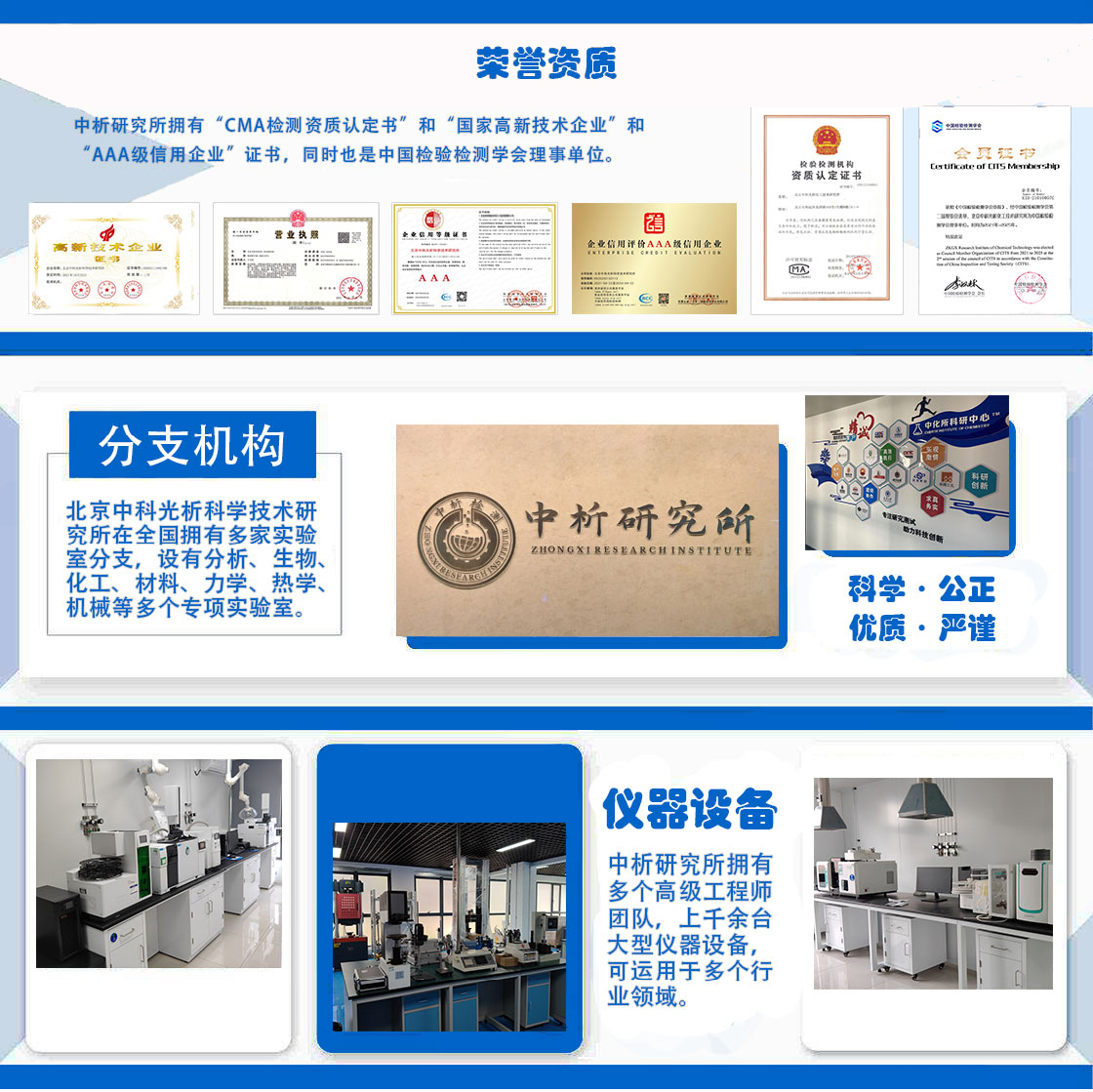
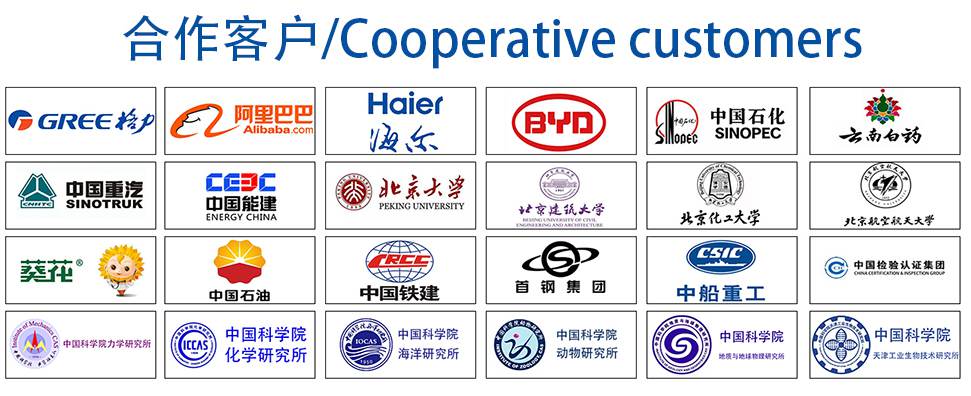
材料实验室
热门检测
推荐检测
联系电话
400-635-0567