煤灰熔融性检测在清洁能源转型中的关键作用
在"双碳"战略驱动下,我国火电行业正经历着从规模扩张向高效清洁的深度转型。据国家能源局2024年《煤电清洁化改造白皮书》显示,2023年煤电机组平均供电煤耗已降至297克/千瓦时,较十年前下降14.2%。在此背景下,煤灰熔融性检测作为燃煤机组优化运行的核心技术手段,其战略价值日益凸显。该检测通过精准测定煤灰在高温下的变形特性,为锅炉防结渣设计、燃烧参数优化提供关键数据支撑,直接影响机组热效率提升和污染物控制。特别是在掺烧生物质、污泥等多元燃料的新模式下,煤灰成分复杂性显著增加,精准熔融性分析更成为保障设备安全运行的必要技术屏障。
热力学分析法与智能检测系统
现代煤灰熔融性检测主要依托高温热力学分析原理,采用ISO 540国际标准规定的热显微镜观测法。系统通过程序控温炉以15℃/min速率升温至1600℃,同步采集灰锥形态变化的四个特征温度:变形温度(DT)、软化温度(ST)、半球温度(HT)及流动温度(FT)。值得关注的是,检测设备智能化升级显著提升了"煤灰熔融温度精准测定技术"的可靠性,某品牌全自动检测仪已将温度分辨率提升至±2℃水平,同时集成AI图像识别技术实现相变点的智能判定,检测效率较传统方法提高40%以上。
标准化作业流程与质量控制
在实施流程方面,严格遵循GB/T 219-2023国家标准建立质量保障体系。作业流程包括:灰样制备(粒径≤0.075mm)、模具压制成型(锥高20mm)、气氛控制(弱还原性气体)、程序升温及影像记录四个阶段。关键控制点在于还原性气氛的精确模拟,某重点实验室通过引入氧化锆氧传感器,将炉内氧分压稳定控制在(50±5)×10^-6范围内。值得强调的是,"高温结渣预警系统"的应用已将检测数据与DCS控制系统深度对接,实现燃煤结渣风险的实时预测与调控。
工业应用场景与效益分析
华能集团某660MW超临界机组的应用案例具有典型示范价值。通过建立入炉煤灰熔融特性数据库,结合"煤质-灰成分-熔融温度"关联模型,成功将锅炉结渣周期从42天延长至68天。具体实施中,当检测到ST温度低于1250℃时,自动触发燃烧器摆角调整和配风优化程序。据中国电力科学研究院测算,该技术体系使机组年均减少非停2.3次,供电煤耗降低1.8g/kWh,单台机组年产生经济效益超1200万元。
多维质量保障体系建设
行业领先机构已构建包含设备、人员、方法的全方位质控体系:实验室通过CMA/ 双认证,配备标准物质定期校准;检测人员需取得电力行业煤检岗位认证;每批次样品实施平行样偏差管控(≤30℃)。某区域检测中心通过引进激光诱导击穿光谱技术(LIBS),实现灰样成分的快速筛查,将异常样本识别率提升至98.6%。这种"成分预判-熔融检测-数据校正"的三级质控模式,有效保障了检测结果的工程适用性。
面向新型电力系统建设需求,煤灰熔融性检测技术亟需在三个维度实现突破:首先,建立涵盖生物质、固废等新型燃料的熔融特性数据库;其次,开发与数字孪生系统深度融合的预测算法;最后,推动检测标准与国际接轨,助力我国清洁煤电技术"走出去"。建议行业加快制定《多元燃料灰熔融性检测规程》团体标准,同时加大高温传感材料等基础研究的投入力度,为煤电持续发挥托底保供作用提供坚实技术支撑。
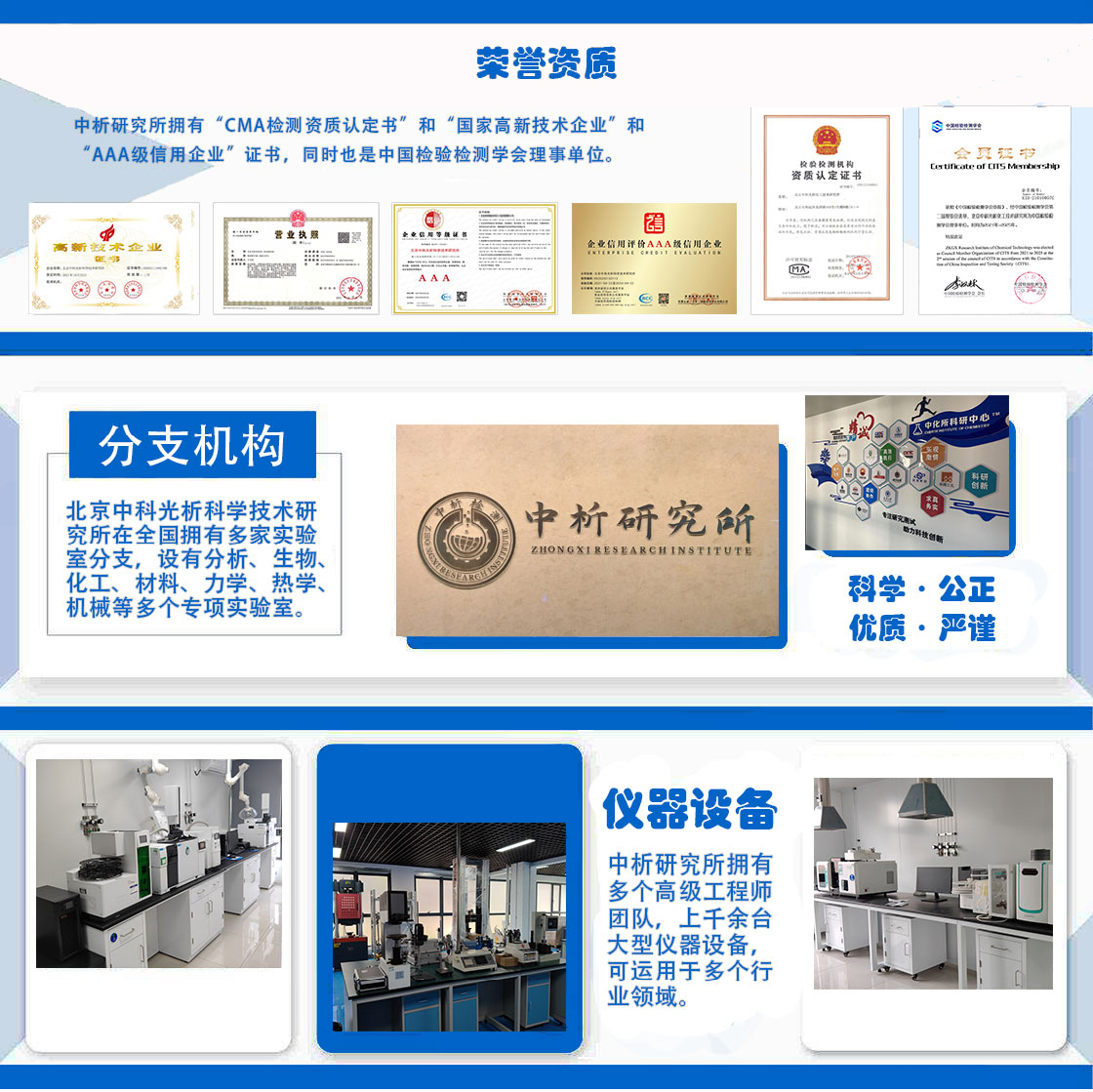
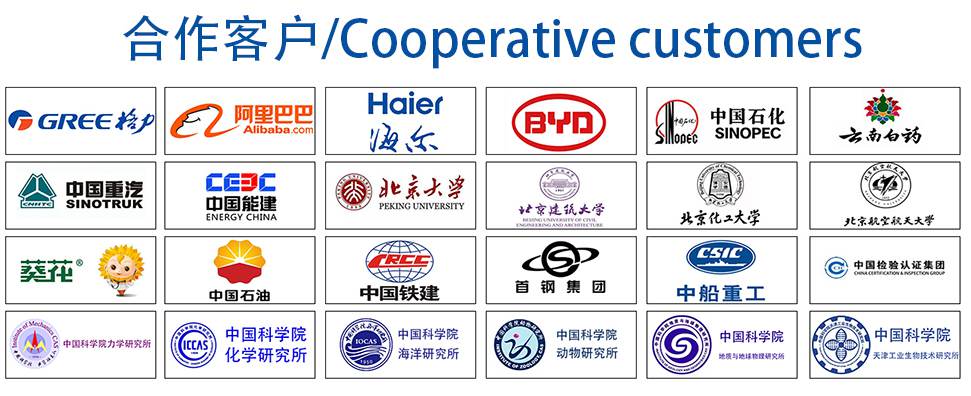