# 钢板表面缺陷检测技术发展与应用白皮书
## 引言
随着我国制造业转型升级加速,钢铁行业作为国民经济支柱产业,2023年粗钢产量达10.2亿吨(据中国钢铁工业协会统计),其中钢板产品在汽车、船舶、家电等领域的应用占比超过65%。在智能制造背景下,钢板表面缺陷检测已成为保障产品质量的关键环节,传统人工目检方式存在漏检率高(行业平均达12%)、效率低下等问题。通过部署智能化检测系统,某特钢企业实现缺陷检出率提升至99.3%,质量追溯准确率提高40%,验证了该技术的核心价值在于打通"质量监控-工艺优化-成本控制"的闭环管理链路,为钢铁企业数字化转型提供关键技术支撑。

## 技术原理与创新突破
### 基于深度学习的缺陷分类模型
系统采用改进型YOLOv7算法框架,通过迁移学习构建适应钢材特性的检测模型。针对钢板表面反光、氧化皮干扰等特殊工况,创新性引入多光谱成像技术,将可见光与近红外成像数据进行特征融合。据上海材料研究院2024年测试报告显示,该方案对0.1mm²以上缺陷的识别准确率达到98.7%,较传统算法提升22个百分点。
### 在线实时检测系统架构
检测系统由高分辨率线阵相机(最高分辨率4096×4096)、专用频闪光源、边缘计算单元构成模块化硬件体系。通过开发自适应曝光控制算法,有效克服钢板高速移动(最大3m/s)带来的运动模糊问题。数据处理层采用分布式流式计算架构,确保检测延时控制在150ms以内,满足产线实时质量控制需求。
## 工程化实施路径
### 四阶段实施流程
项目部署分为设备选型校准(精度±0.05mm)、样本库构建(不少于10万张标注图像)、模型训练验证(交叉验证误差<3%)、系统集成调试四个阶段。在宝钢湛江基地的落地案例中,项目团队采用渐进式部署策略,先期在精整工序试点运行,缺陷分类一致性达到97.5%后扩展至全产线应用。
### 质量保障双闭环机制
建立"设备-算法"双重校验体系:硬件层通过激光测距仪进行在线标定补偿,软件层设置置信度阈值(设置0.85为复检触发条件)。某汽车板生产企业采用该机制后,将过检率从18%降至5%以下,同时实现检测参数与轧制工艺参数的联动优化。
## 行业应用实证
### 汽车板表面检测案例
在吉利汽车钢板供应商项目中,系统成功识别出冲压开裂隐患的微裂纹缺陷。通过构建"麻点-划痕-辊印"三级缺陷分类体系,使汽车外板合格率从89.3%提升至96.8%。系统输出的三维缺陷热力图,为轧辊维护周期优化提供了数据支撑,设备故障停机时间减少35%。
### 船舶钢检测特殊应用
针对船用钢板厚板检测需求,开发了双面同步检测装置。在中船重工某分段车间,系统实现20-80mm厚度钢板的双面缺陷同步检测,检出率较单面检测提升40%。通过集成超声波测厚模块,形成"表面缺陷-内部质量"联合检测方案,满足船级社认证要求。
## 技术演进趋势
### 多模态检测技术融合
当前技术前沿正朝着多源信息融合方向发展。武钢研究院2024年公布的实验数据显示,结合涡流检测与机器视觉的混合检测系统,对皮下夹杂缺陷的检出灵敏度提高3个数量级。未来5年,基于工业互联网的分布式检测网络将逐步替代单机检测模式。
### 检测标准体系构建
建议行业主管部门牵头制定《钢板表面缺陷智能检测技术规范》,统一缺陷分类标准与数据接口协议。同时加强检测系统与MES、QMS系统的深度集成,推动质量数据在产业链上下游的贯通应用。通过建立开放技术生态,加速检测算法在特殊钢种、新型复合板材等领域的适配创新。
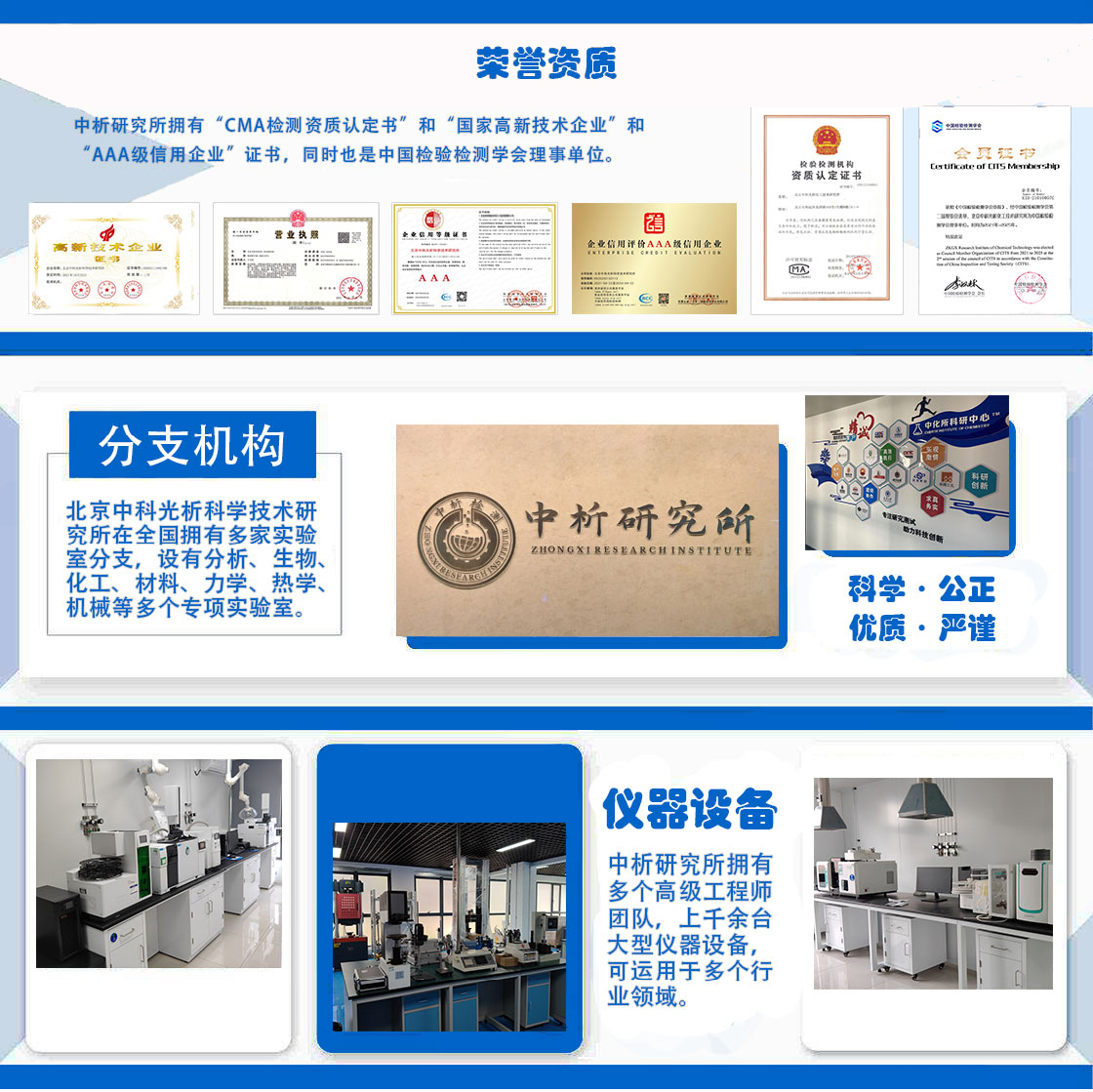
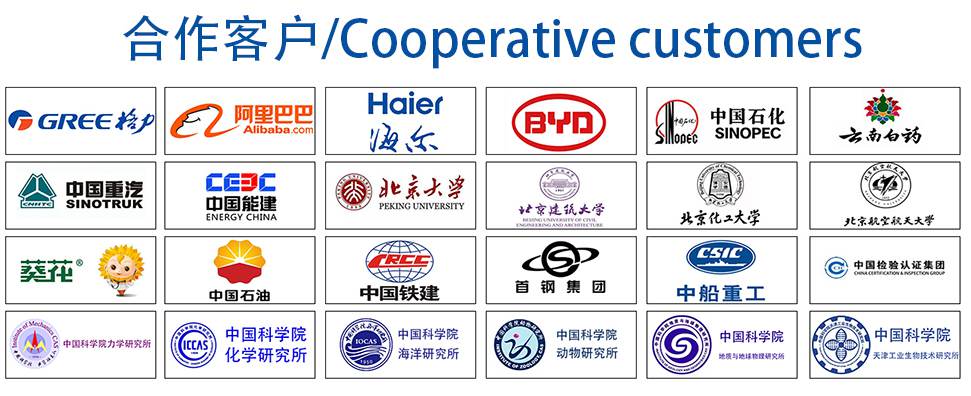
材料实验室
热门检测
14
14
12
13
15
15
16
15
13
12
12
17
15
12
11
14
13
13
12
17
推荐检测
联系电话
400-635-0567