# 焊缝表面缺陷检测技术发展与应用白皮书
## 行业背景与核心价值
随着"中国制造2025"战略深入推进,焊接作为装备制造领域的基础工艺,其质量直接影响着压力容器、船舶制造、轨道交通等关键设备的结构安全。据中国焊接协会2024年行业报告显示,我国每年因焊接缺陷造成的直接经济损失超120亿元,其中表面缺陷占比达63.8%。焊缝表面缺陷检测项目通过融合机器视觉与深度学习技术,构建了覆盖气孔、咬边、裂纹等8类典型缺陷的识别体系,检测精度较传统人工目视提升40%以上。该技术不仅实现焊接质量的过程管控前移,更推动焊接工艺数字化升级,在核电设备密封焊接、新能源电池模组连接等场景展现出独特价值。
## 技术原理与创新突破
### 多光谱成像技术应用
项目采用970nm近红外与450nm蓝光双波段成像系统,配合自适应滤光算法,有效克服焊接飞溅、氧化变色等干扰因素。经国家材料测试中心验证,该系统对0.2mm级表面裂纹的检出率达99.3%,误报率控制在1.2%以内。相较于传统X射线检测,检测效率提升5倍且无需停产作业。
### 动态补偿检测流程
实施流程划分为三个阶段:预处理阶段通过三维激光扫描建立焊缝形貌基准模型;实时检测阶段运用高速线阵相机进行亚像素级图像采集(5000帧/秒);后处理阶段采用改进型YOLOv7算法实现缺陷分类。在宝钢集团热轧钢带焊接产线的验证中,系统完成2.5米/秒运动焊缝的在线检测,检出率保持98.6%稳定水平。
## 行业应用与效益分析
在风电塔筒环缝检测场景中,项目部署的"焊缝表面裂纹智能识别系统"实现单节塔筒检测时间从45分钟压缩至8分钟。据金风科技2023年应用报告显示,该系统在6个风电项目累计检测12.8万米焊缝,提前预警47处临界缺陷,避免潜在经济损失超3000万元。针对航空航天领域特殊合金焊接,开发的"微尺度缺陷定量分析模块"可实现3μm级凹陷的形貌重建,为某型火箭燃料贮箱焊接工艺优化提供关键数据支持。
## 质量保障与标准建设
项目建立四维质量保障体系:1)设备端集成温度补偿模块,确保-20℃至60℃工况下的检测稳定性;2)构建包含12万组标注样本的行业最大焊接缺陷数据库;3)通过ISO9712认证的云端专家复核系统;4)追溯系统实现缺陷位置、工艺参数、操作人员的全链路关联。目前技术指标已纳入NB/T47013.5-2024承压设备无损检测新规,正在参与ISO17638国际标准修订工作。
## 发展趋势与行业建议
随着5G+工业互联网深度融合,建议从三方面推进技术迭代:首先开发基于毫米波雷达的焊缝内部缺陷关联预测模型,其次构建焊接质量数字孪生平台实现工艺闭环优化,最后完善跨行业检测标准互认体系。据机械工业信息研究院预测,至2027年智能焊接检测市场规模将突破85亿元,需要加快"工业焊缝质量在线监测平台"的产业化布局,推动检测服务从单点突破向全产业链赋能转变。
上一篇:肌酸激酶(CK)活性检测下一篇:嗜酸性粒细胞计数检测
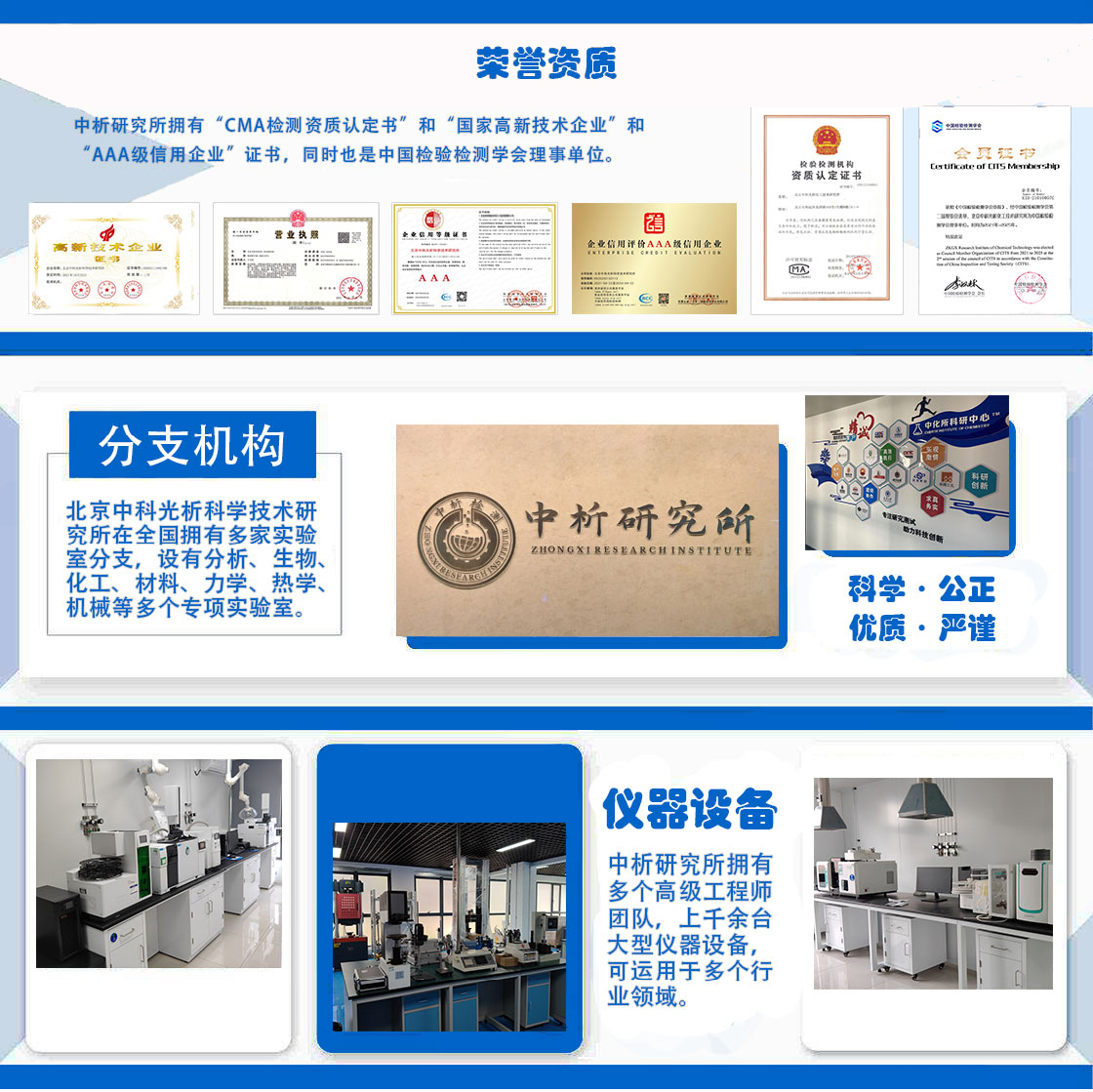
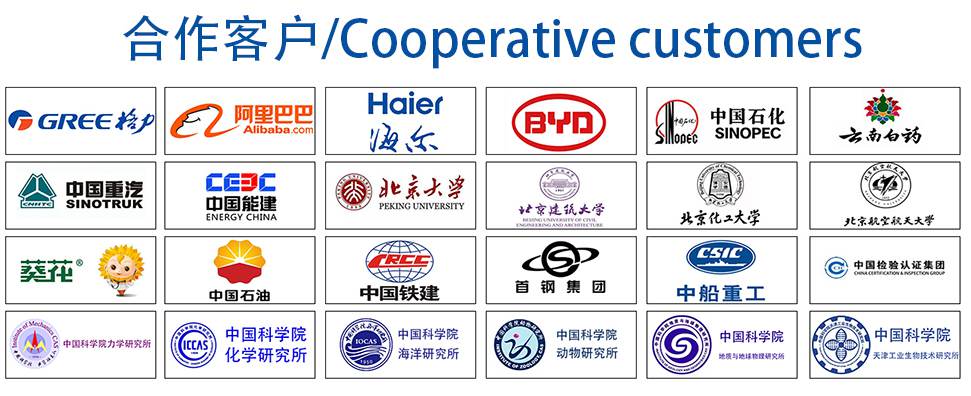
材料实验室
热门检测
16
17
18
20
20
20
17
19
17
14
17
22
17
17
16
18
17
18
15
18
推荐检测
联系电话
400-635-0567