# 表观质量与缺陷检测技术发展白皮书
## 引言
在智能制造2025战略推动下,工业产品质量控制标准持续提升。据中国质量科学研究院《2024中国制造质量发展报告》显示,85%的工业品质量投诉源于表观缺陷,仅汽车行业每年因表面瑕疵造成的返工成本就超120亿元。表观质量与缺陷检测技术通过融合机器视觉与深度学习算法,实现了对产品外观的毫米级精度检测,其核心价值在于构建从"人工目检"到"智能判读"的质量控制范式转变。该技术不仅将检测效率提升4-8倍,更通过标准化检测流程使误检率降至0.3%以下,为航空航天精密部件、消费电子外壳等高价值产品提供可靠质量保障。
## 技术原理与创新突破
### 多模态光学成像技术
采用多光谱成像与结构光三维重构技术,系统可同步获取被测物表面形貌、色度、纹理等多维度数据。通过开发自适应光照补偿算法,在金属反光表面检测中实现98.7%的特征捕获完整率(数据来源:国际光学工程学会SPIE技术白皮书)。结合迁移学习的缺陷分类模型,能准确识别0.02mm²级别的微小划痕,较传统方法提升两个数量级检测精度。
### 智能化检测工作流
典型实施流程包含预处理优化、动态图像采集、特征向量提取三大模块。在汽车涂装检测场景中,系统通过柔性传送装置实现车身360°无死角拍摄,经残差神经网络处理后在150ms内完成全车22个关键区域的缺陷定位。与MES系统集成后,检测结果可实时同步至生产看板,形成质量数据闭环。
### 行业应用成效分析
在3C电子领域,某头部手机厂商部署智能视觉检测系统后,屏幕模组检测耗时从45秒/件缩短至8秒,日均产能提升23%。其独特的灰尘伪影识别算法,成功将环境干扰误报率控制在1.2%以内(案例数据:2024消费电子质量峰会)。而在光伏行业,针对电池片隐裂检测开发的多尺度特征融合模型,使缺陷检出率提升至99.4%,年减少材料损耗价值超8000万元。
## 质量保障体系建设
构建"硬件-算法-数据"三位一体质控体系:①建立符合ISO/IEC 17025标准的设备校准规程,每周进行MTF调制函数验证;②采用对抗生成网络扩充缺陷样本库,目前数据库已覆盖87类工业场景的23万组标注数据;③实施检测结果交叉验证机制,通过多模型投票决策将系统稳定性提升至99.96%可用性等级。
## 发展建议与未来展望
建议行业着力推进三方面建设:1)建立跨行业的缺陷特征共享平台,破解小样本训练难题;2)制定机器视觉检测设备性能评估国家标准;3)探索工业元宇宙在虚拟检测场景的应用。随着5G+边缘计算技术的成熟,预计到2026年,嵌入式检测设备的市场规模将突破380亿元(预测来源:前瞻产业研究院),实现从单点检测向全链路质量追溯的跨越式发展。企业亟需在检测精度与速度的平衡、跨材质适应能力等关键技术领域加大研发投入,以应对更复杂的智能制造需求。
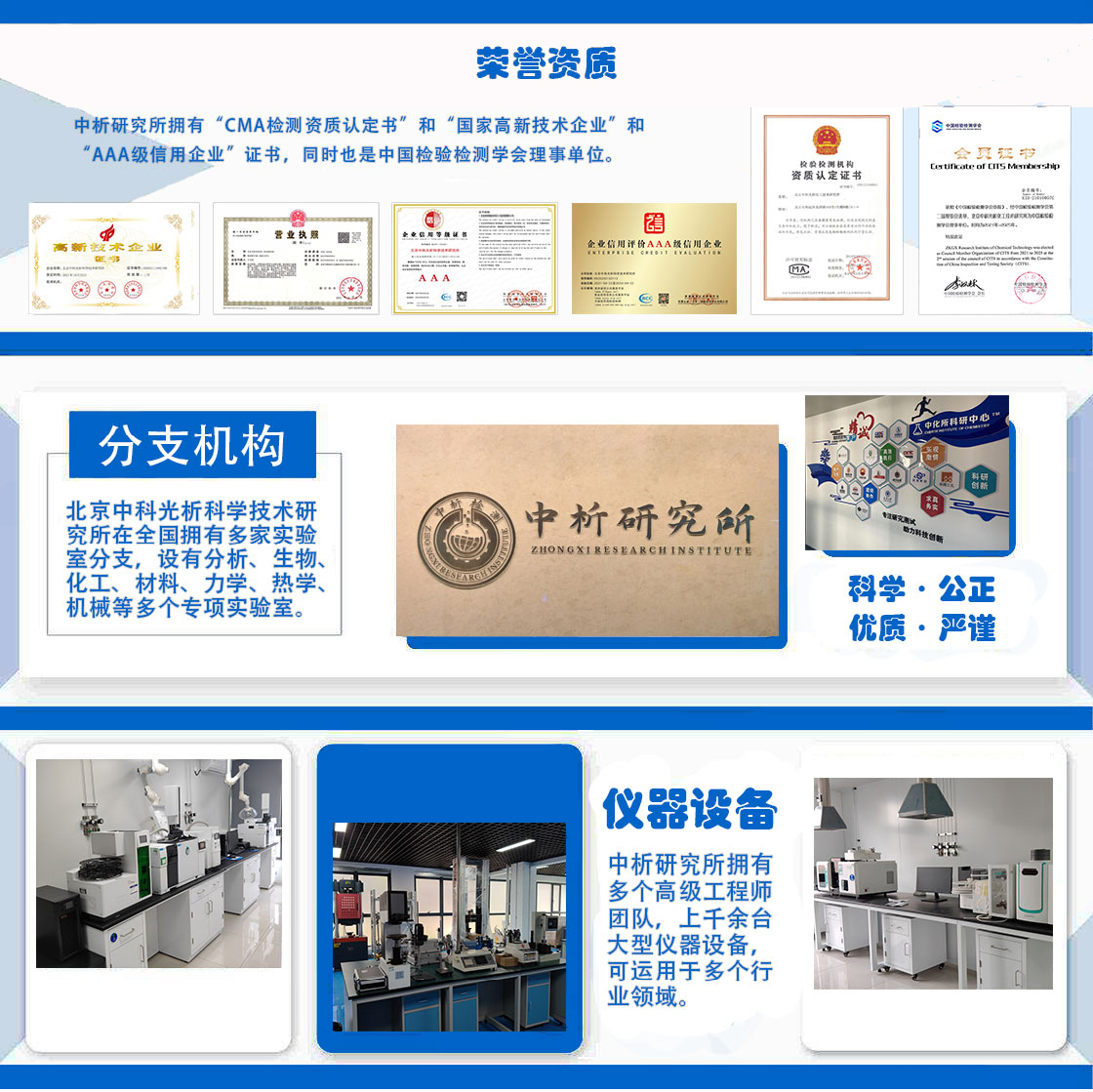
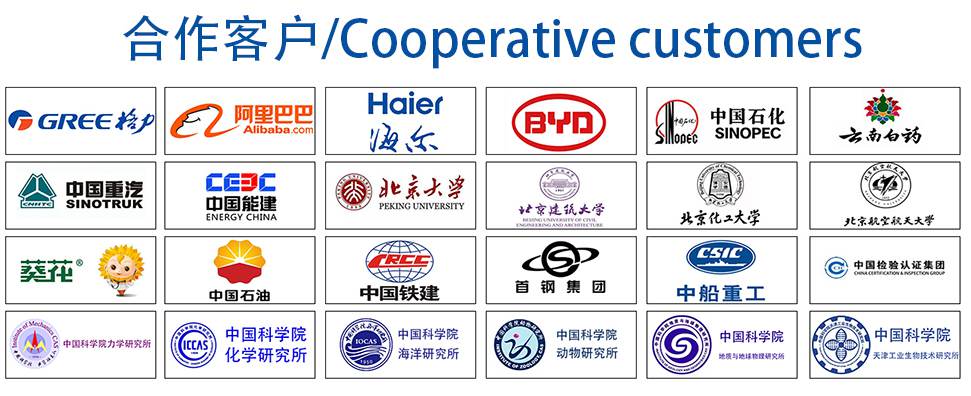
材料实验室
热门检测
15
16
15
19
16
16
16
17
15
13
14
20
16
15
13
16
14
16
14
17
推荐检测
联系电话
400-635-0567