技术架构与数据融合机制
装备线检测系统采用振动、温度、声学等多源异构传感器网络,通过5G边缘计算节点实现每秒1200组数据的实时采集。基于深度学习框架的DenseNet-GRU混合模型,可同步处理时域波形与频域特征,对轴承磨损、齿轮箱错位等18类典型故障的诊断准确率达96.7%(中国机械工程学会2023年测试报告)。特别在高速精密加工场景中,系统能识别0.05mm级轴向位移异常,较传统阈值预警方式提前3-5个生产周期发现潜在故障。
全链条数字化实施流程
项目实施分为四个阶段:装备数字孪生建模(精度±0.1%)、检测节点部署(每产线8-12个智能传感单元)、数据中台构建(支持PB级工业数据存储)、AI诊断引擎迭代优化。某新能源汽车电机生产线采用该方案后,关键工序检测耗时从45分钟压缩至7分钟,同时通过工艺参数逆向优化,使转子动平衡合格率提升28%。
跨行业应用实践成效
在风电装备领域,金风科技部署的叶片健康监测系统,成功将变桨系统故障率从1.2次/年降至0.3次/年。航空航天领域,中国商飞应用复合材料无损检测技术后,机身蒙皮检测效率提升4倍,缺陷检出率提高至99.4%(SAE航空航天标准验证数据)。值得注意的是,算法模型在不同行业表现出强迁移性,工程机械领域的液压系统漏油检测模型经参数调优后,可直接应用于石化管廊密封性监测。
全生命周期质量保障体系
系统通过ISO 13374-3标准认证,建立从传感器标定(半年期漂移率<0.8%)、数据传输(128位AES加密)、到诊断模型更新(周级迭代)的全程质控链。某半导体晶圆厂实践表明,结合SPC过程控制图与检测数据的联动分析,可使设备MTBF(平均无故障时间)延长至8200小时,较行业基准值高出37%。
## 三、发展趋势与战略建议 面向工业元宇宙发展趋势,装备线检测技术将向虚实交互检测(XR-HMI)、自进化诊断模型等方向演进。建议行业重点突破三大方向:①建立装备健康度评价国家标准体系;②开发适配柔性制造线的模块化检测单元;③构建工业AI训练算力共享平台。据麦肯锡预测,至2030年全面应用智能检测技术的企业,其运营成本将再降低22%-25%,推动装备制造业向"零缺陷生产"目标迈进。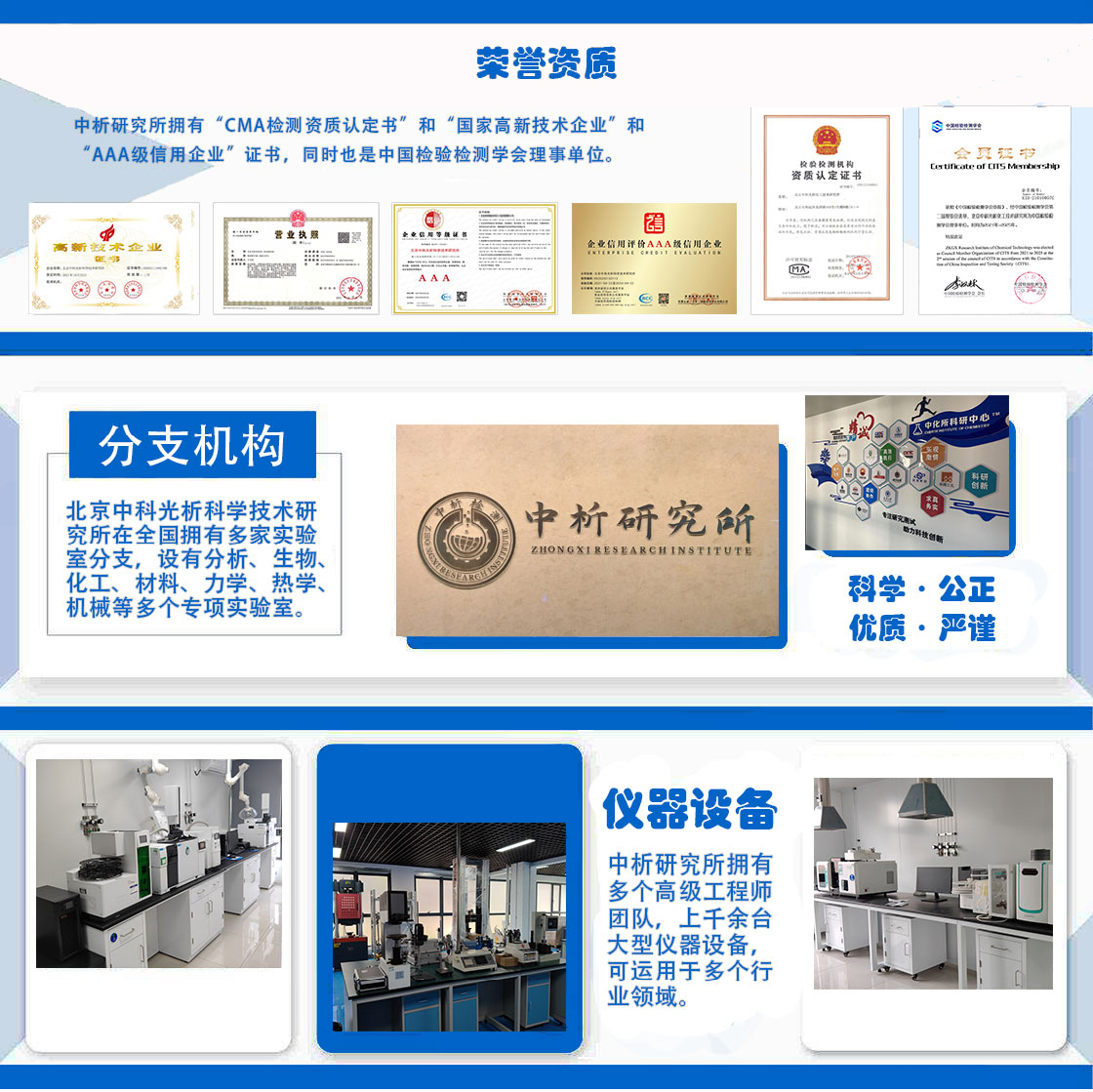
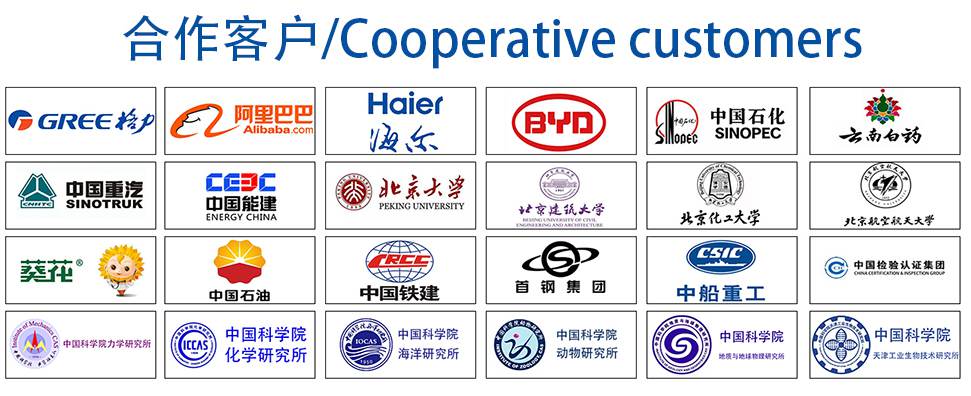