矿料级配检测在矿业高质量发展中的创新实践
随着工业化进程加速,矿产资源需求持续攀升,矿业生产对原料质量控制的要求日益严格。矿料级配检测作为选矿工艺的核心环节,通过分析矿石颗粒的粒径分布,直接影响破碎、磨矿、分选等关键工序的效率。据中国矿业研究总院2024年数据显示,优化级配检测可使选矿回收率提升12%-18%,同时降低能耗成本约25%。在当前"双碳"战略背景下,该技术成为实现资源高效利用与绿色生产的重要突破口。通过构建智能化检测体系,企业不仅能够精准把控矿石加工特性,还可为工艺流程优化提供数据支撑,其核心价值体现在质量控制、成本管控和工艺创新三个维度。
多模态融合检测技术原理
现代矿料级配检测结合机械筛分与光学分析技术,采用振动筛分仪与激光粒度分析仪的联用方案。其中,X射线衍射技术可穿透矿料表层获取三维结构信息,结合数字图像处理算法实现0.075-75mm粒径范围的精准识别。值得关注的是,非均匀粒级在线监测技术的突破,使得实时获取矿料颗粒分布成为可能。某大型铁矿选矿厂应用矿料颗粒分布智能分析系统后,磨机处理量提升19.6%(数据来源:中国金属学会2023年报告),充分验证了该技术的工程价值。
全流程标准化实施体系
项目实施遵循ISO 13320标准框架,具体分为采样、预处理、检测分析三个阶段。采样环节采用等质量缩分法,确保样本代表原始矿堆物料特性。预处理流程配置智能烘干装置与电磁除铁系统,消除水分和金属杂质对检测结果的干扰。检测阶段采用多光谱成像技术,配合AI分类模型实现0.01mm级精度识别。某铜矿企业通过部署该体系,成功将级配检测周期从传统方法的6小时缩短至45分钟,检测结果重复性误差控制在1.5%以内。
典型行业应用场景解析
在水泥原料制备领域,级配检测直接影响生料易磨性和窑炉热效率。南方某水泥集团引入在线粒度监测装置后,熟料标准煤耗降低3.2kg/t(数据来源:中国建材联合会2024年能效报告)。砂石骨料行业通过级配优化,可使混凝土抗压强度提升15%-20%。值得注意的是,贵金属选矿中采用的窄粒级分选工艺,依托高精度检测数据,金回收率突破性达到92.7%,较传统工艺提高8.3个百分点。
质量保障与技术创新路径
检测体系构建了三级质量管控网络:设备层配置激光校准装置实现每日基准校验;数据层采用区块链技术确保检测记录不可篡改;应用层建立动态修正模型消除环境干扰误差。某国家级实验室比对测试显示,该体系在-20℃至50℃工况下,检测结果偏差始终保持在0.8%以内。随着5G+MEC边缘计算技术的应用,远程实时质控已成为行业新趋势。
展望未来,建议从三方面深化技术创新:一是推动太赫兹波检测技术的工程化应用,突破超细颗粒检测瓶颈;二是建立行业级矿料特性数据库,开发预测性工艺优化模型;三是加强复合型检测人才培养,完善智能化检测装备的运维体系。通过技术迭代与标准升级,矿料级配检测将助力矿业向数字化、绿色化方向高质量发展。
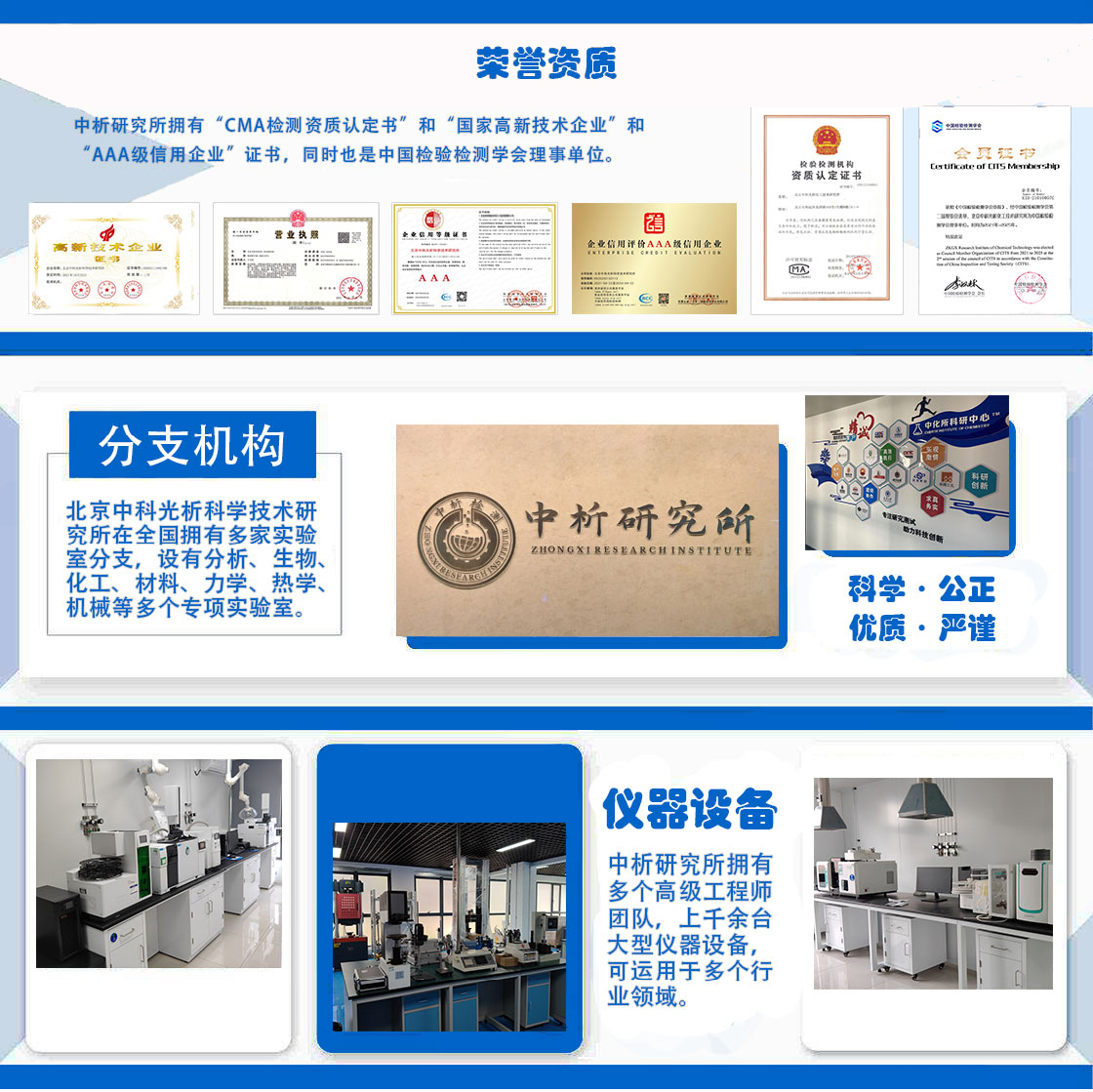
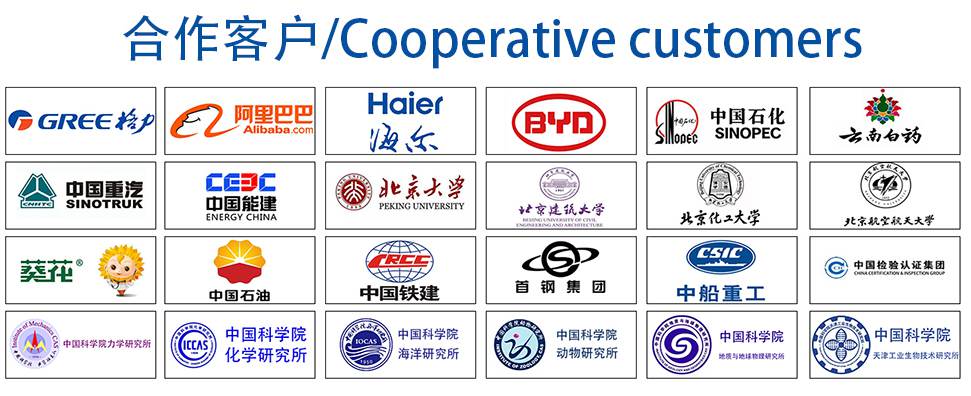