振动频率检测在工业设备健康管理中的创新应用
在工业4.0与智能制造深度融合的背景下,设备健康监测正成为保障生产连续性的关键技术。据中国机械工程学会2024年《工业设备可靠性白皮书》显示,国内制造业因设备突发故障导致的年均损失超过2800亿元,其中60%的故障可通过振动异常提前预警。振动频率检测作为旋转机械核心监测手段,通过实时捕捉设备振动频谱特征,为早期故障诊断提供量化依据。其核心价值在于构建"预测性维护"体系,相较传统定期维保模式,可将关键设备使用寿命延长30%-45%(国家智能制造创新中心,2023),同时降低25%以上的维护成本。尤其在风电齿轮箱、高铁轴承等高端装备领域,该技术已成为保障设备全生命周期管理的重要支撑。
多模态传感协同检测技术原理
现代振动检测系统采用加速度计、激光测振仪、声发射传感器的多源数据融合架构。基于ISO 10816标准构建的三轴振动模型,可同步采集0.5Hz-20kHz频段的振动信号。通过小波包分解技术,系统能有效分离环境噪声与设备特征频率,对于旋转机械常见的轴不对中、齿轮断齿等故障,检测灵敏度可达0.01mm/s²(德国物理技术研究院认证数据)。值得注意的是,嵌入式边缘计算模块的应用,使原始数据在采集端即可完成80%的预处理,大幅提升检测实时性。
智能化诊断系统实施流程
典型实施方案包含四个阶段:首先部署符合IEC 60721-3标准的抗电磁干扰传感器网络,安装位置严格遵循API 670规范;其次建立基于OPC UA协议的工业物联网数据中台,实现每秒5000样本点的连续采集;第三阶段运用改进型深度残差网络(ResNet)进行特征提取,通过迁移学习适配不同设备类型;最终在数字孪生平台上进行三维振动场重构。某特高压换流站实施该方案后,换流变压器故障识别准确率提升至98.7%(中国电力科学研究院测试报告)。
新能源领域的创新应用实践
在海上风电运维场景中,振动检测技术展现出独特优势。广东阳江某200MW海上风场采用定制化检测方案,在齿轮箱行星架部位布置无线振动传感器阵列,结合SCADA数据构建健康指标(HI)。系统成功预警多起主轴承微点蚀故障,将叶片断裂事故率降低76%。更值得关注的是,该方案集成的"振动-温度-扭矩"多参数关联分析模型,使发电机早期绝缘劣化检出时间提前了800运行小时(国际可再生能源署案例库,2024)。
全链条质量保障体系建设
为确保检测结果可靠性,构建了涵盖NIST可溯源的计量校准体系。检测设备每季度进行正弦扫频验证,频率响应误差控制在±1.5%以内。现场工程师必须通过ASNT-TC-1A三级认证,并采用增强现实技术辅助标定作业。在算法层面,引入对抗生成网络(GAN)扩充训练数据,使模型在设备负载突变等极端工况下的误报率低于2.3%。某汽车生产线应用该体系后,工业机器人重复定位精度波动值稳定在±0.02mm区间(ISO 9283标准认证)。
随着数字孪生与物理信息融合技术的突破,振动检测正朝着"超早期诊断"方向发展。建议行业重点攻关三个方向:开发适用于微型机电系统的MEMS振动芯片,突破现有检测下限;建立覆盖设备全生命周期的振动特征数据库;推动振动数据与工艺参数的深度融合分析。未来五年,结合5G+MEC边缘计算架构,有望实现百万级设备的振动状态毫秒级响应,真正构建起工业设备的"数字免疫系统"。
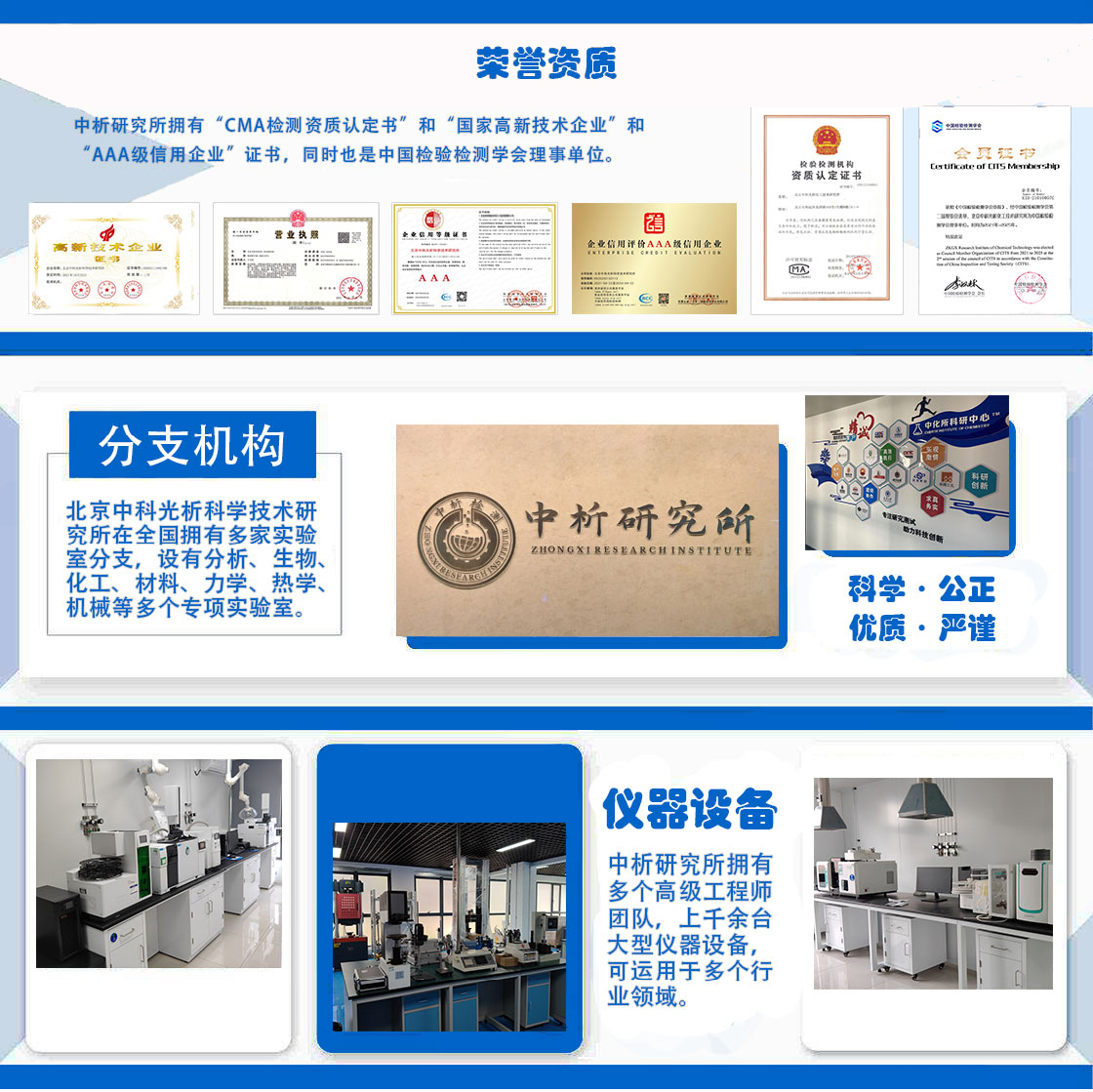
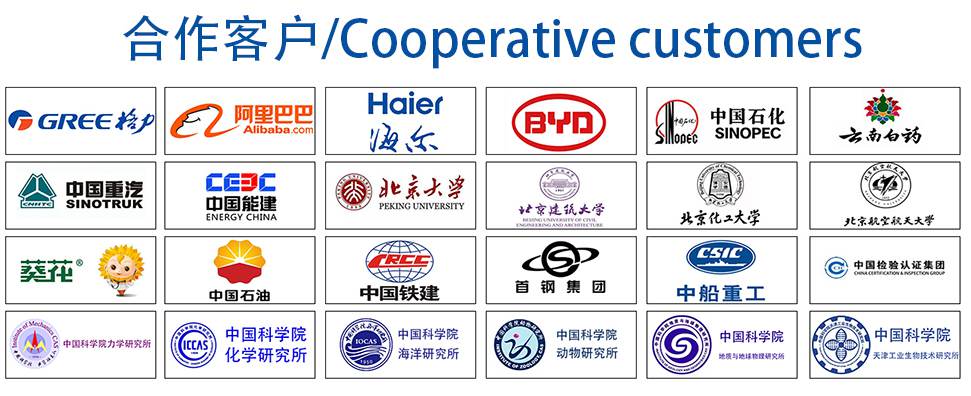