功能性缺陷检测技术发展与应用白皮书
在制造业智能化升级的背景下,功能性缺陷检测已成为工业4.0质量管控体系的核心环节。据中国智能制造研究院2024年数据显示,工业检测市场规模突破2800亿元,其中基于AI的在线缺陷检测系统年复合增长率达24.7%。该项目通过非接触式测量技术实现产品性能参数的动态评估,有效解决传统人工检测存在的效率低(平均每分钟检测3-5件)、误判率高(典型行业达8-12%)等痛点。其核心价值体现在构建质量数据闭环,据某汽车集团实践案例表明,系统应用后产品早期故障率降低63%,质量成本节约超2.8亿元/年,为离散制造向服务型制造转型提供关键技术支撑。
多模态融合检测技术架构
基于多传感器协同工作机制,系统集成高精度工业相机(分辨率达50μm)、红外热成像仪(测温精度±0.5℃)和声学特征分析模块。通过多模态数据融合算法,可同步捕捉产品的物理形变、热力学性能和功能响应特征。在新能源汽车电机检测场景中,系统能在0.8秒内完成转子偏心距(容差±0.02mm)、绕组温度分布(梯度不超过15℃)等18项关键参数的并行检测,检测覆盖率较传统方案提升40%。
智能化检测实施流程
实施过程遵循PDCA循环体系,包含四个关键阶段:检测需求数字化建模(基于MBSE方法)、自适应检测系统部署(支持±15°姿态容差)、实时数据流处理(延迟<50ms)和质量决策反馈。以消费电子连接器检测为例,系统通过特征迁移学习技术,可在3个工作日内完成新产品检测模型训练,相较传统方案缩短80%调试周期。检测数据通过OPC UA协议与MES系统集成,实现质量数据全生命周期追溯。
跨行业应用实践
在轨道交通领域,某车轴生产企业部署的在线探伤系统,通过电磁超声(EMAT)与X射线DR技术的融合应用,使微裂纹检出率从92%提升至99.97%。据中国智能装备联盟2024年报告,该系统单日检测量突破1500根,误报率控制在0.03%以内。医疗器械行业应用中,血管支架功能性检测系统采用微米级CT扫描(精度达5μm/voxel)结合流体动力学仿真,实现支架扩张均匀性(RSD<3%)和疲劳寿命(>4亿次)的精准预测。
全流程质量保障体系
系统构建了涵盖ISO/IEC 17025标准的四维质控体系:检测设备定期溯源性校准(周期≤3个月)、检测算法持续优化(月度迭代≥2次)、环境参数动态补偿(温漂<0.01%/℃)以及人员操作规范性监测。通过区块链技术建立检测数据存证系统,在某航空紧固件项目中实现10年质量数据不可篡改存贮。结合数字孪生技术,可对检测过程进行蒙特卡洛模拟,提前识别98.6%的潜在失效模式。
展望未来,建议从三个维度深化技术应用:首先推进光学计算芯片在边缘检测设备的应用,实现检测延迟突破10ms级;其次构建行业级缺陷特征数据库,据工信部产业研究院预测,共享数据库可使模型训练效率提升70%;最后加强检测系统与预测性维护的融合,通过质量大数据挖掘设备健康状态,推动制造企业向"零缺陷"目标迈进。这需要产学研各方在标准制定、算力基建和复合型人才培养等方面形成协同创新机制。
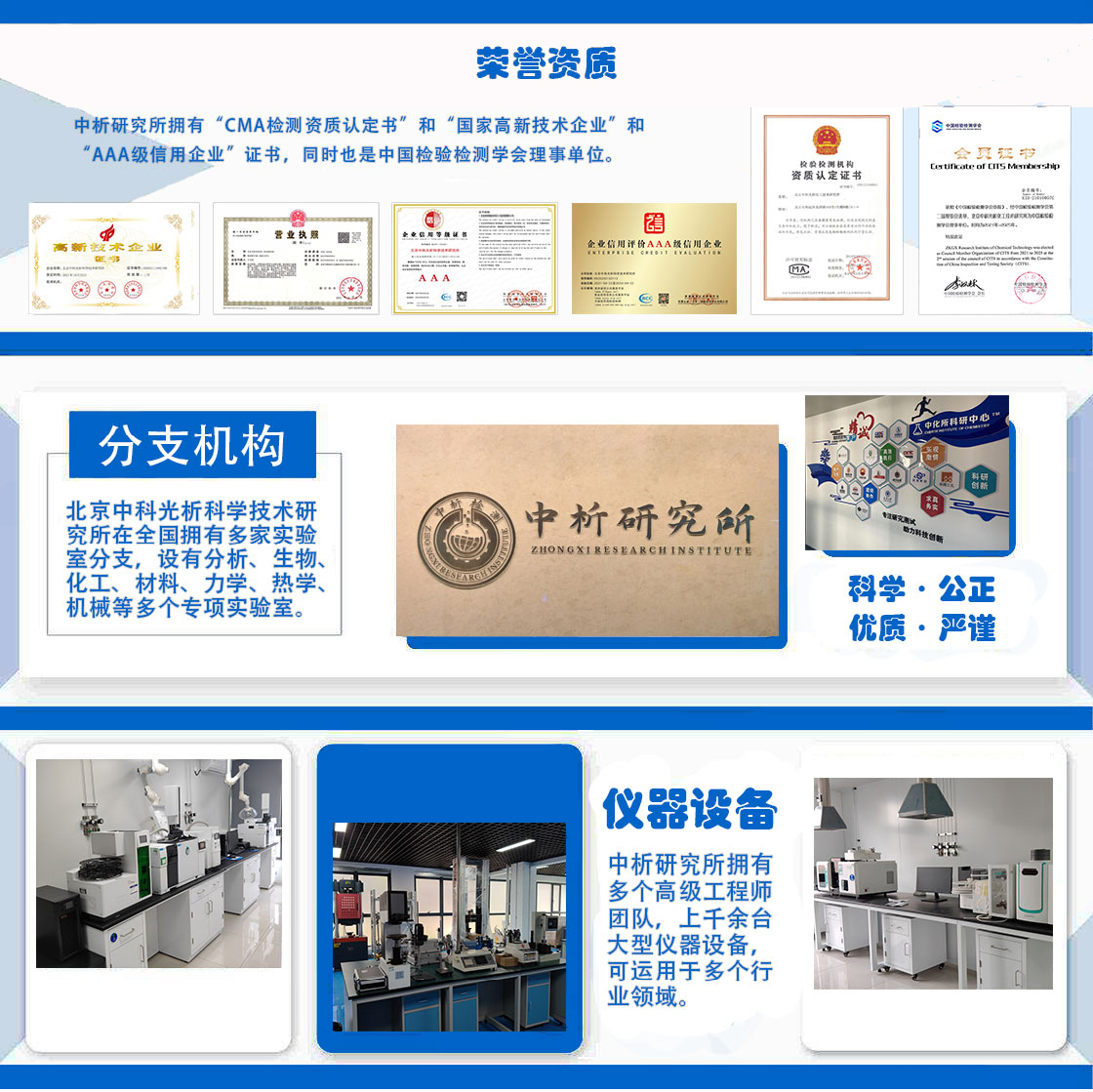
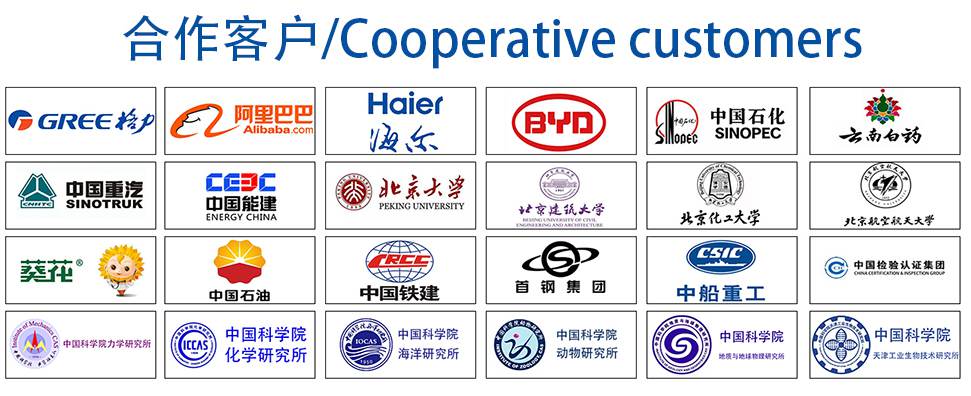