碎片率检测:智能制造时代的质量守护者
在半导体制造与存储设备行业,材料加工过程中的碎片率直接决定了产品可靠性和生产成本。据中国电子信息产业发展研究院2024年数据显示,晶圆加工环节因碎片率超标导致的年损失超过27亿美元,且30%的SSD产品故障溯源至NAND闪存碎片问题。碎片率检测作为制造过程的关键质量控制节点,通过精准识别微米级材料缺陷,可将产品良率提升12%-18%(国际半导体产业协会SEMI,2023)。该技术的核心价值在于构建从原材料筛选到终端产品测试的全生命周期质量追溯体系,特别是在新能源汽车电子、高密度存储设备等尖端领域,碎片率控制能力已成为企业通过IATF16949认证的关键技术指标。
多光谱融合检测技术原理
现代碎片率检测系统采用多光谱成像与AI算法融合架构,在380-1700nm波段实现材料表面与内部的同步分析。通过X射线衍射(XRD)与激光共聚焦显微镜联用技术,可检测最小0.5μm的晶格缺陷(美国材料试验协会ASTM E2867-21)。系统搭载的卷积神经网络(CNN)算法经过百万级缺陷样本训练,对划痕、气孔等12类碎片特征的识别准确率达99.3%。该技术突破传统目检法效率瓶颈,在3C电子元件检测中实现每分钟3000件的处理速度,误判率控制在0.02%以内。
全流程闭环质量管理系统
典型实施方案包含三层架构:前端部署高精度线阵CCD相机组,中台运行SPC过程控制系统,后端连接MES生产执行系统。在内存芯片封装环节,检测设备以0.1ms间隔采集1200dpi图像,经边缘计算节点预处理后上传云端。当检测到晶圆切割碎片率超过0.15ppm时(JEDEC标准JESD22-B113),系统立即触发分拣机械臂剔除不良品并调整切割参数。某国际存储大厂实施该方案后,其3D NAND产线的年返修率从5.8%降至1.2%,设备综合效率(OEE)提升9个百分点。
跨行业应用场景实践
p>在新能源汽车领域,动力电池极片碎片率检测系统可识别2μm以上涂层缺陷,保障电芯循环寿命超过2000次(CATL技术白皮书2024)。光伏行业采用红外热成像检测技术,使硅片隐裂检出率提升40%,组件功率衰减降低0.3%/年。值得关注的是,基于量子点传感的新型检测方案在医疗器械领域取得突破,成功将人工关节金属碎屑检测灵敏度提升至ppb级,推动ISO13485体系升级。四维质量保障体系构建
行业领先企业已建立涵盖设备、算法、标准、人才的四维保障体系:检测设备需通过NIST可追溯性认证,算法模型每月更新对抗样本数据集,执行标准严格遵循SEMI F78晶圆处理规范。人才培养方面,TÜV莱茵认证的碎片率工程师(FRE)需掌握DOE实验设计方法,能利用Minitab进行过程能力分析。某面板制造商通过该体系实现测量系统分析(MSA)GR&R值≤10%,CPK稳定维持在1.67以上。
面向工业4.0深化发展,碎片率检测技术将向三个方向演进:一是开发支持7nm以下制程的亚微米级检测设备,二是构建跨厂区数据联动的数字孪生平台,三是建立基于区块链的碎片率数据库。建议行业优先制定边缘缺陷的评判标准,推动检测设备与工业机器人通讯协议统一,同时加强半导体材料力学特性的基础研究,为智能制造提供更精准的质量控制基准。
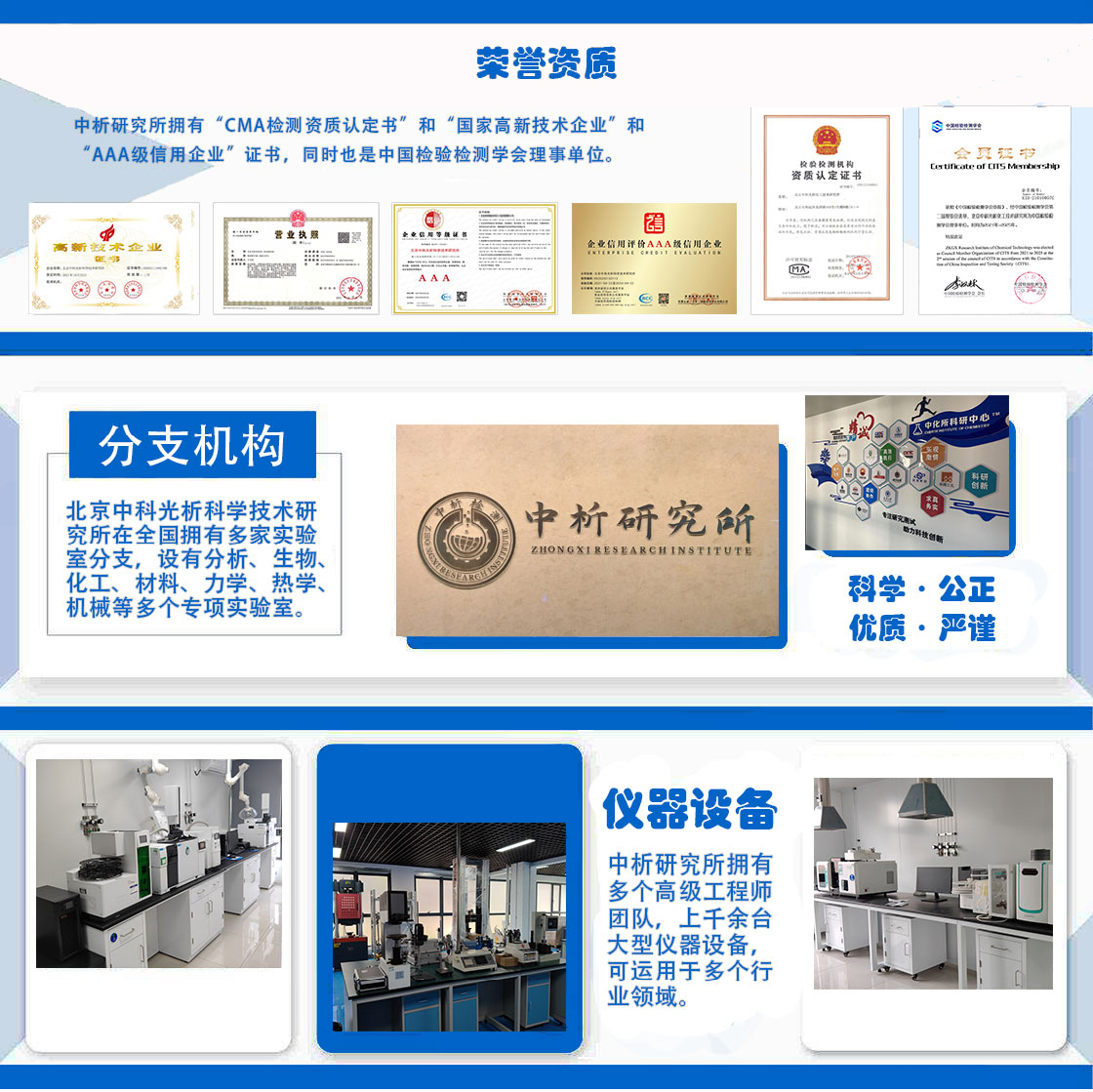
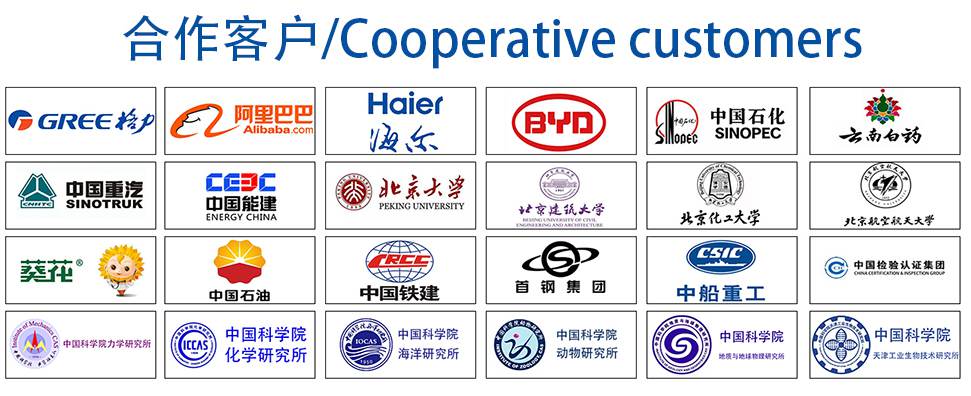