钣金件检测标签与标志检测技术白皮书
在智能制造2025战略推动下,钣金加工行业正经历数字化质检转型关键期。据中国智能制造研究院2024年数据显示,国内钣金件年产量突破8500万件,其中标识系统缺陷导致的退货率仍高达3.2%,造成年经济损失超12亿元。该项目通过构建智能化的标签标志检测体系,不仅能够实现产品全生命周期追溯,更可提升生产过程质量控制精度。其核心价值体现在将传统人工抽检的漏检率从8%降低至0.5%以下,同时通过钣金件激光二维码识别和冲压件耐腐蚀标识检测等技术创新,为企业每年节省质量成本约23%。
多模态融合检测技术原理
本系统采用机器视觉与深度学习算法双重验证机制,通过高分辨率工业相机(最小识别精度0.02mm)采集表面特征,结合改进的YOLOv5模型实现95.7%的识别准确率。针对特殊工况开发的抗反光算法,在强光干扰环境下仍保持89%以上的检测稳定性。值得注意的是,基于迁移学习的字符识别模块,可适应不同厂商的钣金件生产日期喷码检测需求,对模糊、残缺字符的识别成功率提升至82.3%(中国图像处理协会2023基准测试数据)。
全流程自动化实施体系
项目实施遵循PDCA循环质量控制原则,具体流程包括:1)预处理阶段通过3D激光扫描建立数字孪生模型;2)在线检测工位配置双光谱成像系统,同步获取可见光与红外特征;3)数据融合平台实时比对CAD图纸参数;4)NG件自动分拣并生成SPC分析报告。在汽车门板生产线实测中,系统单件检测时间压缩至1.8秒,较传统方式提速4倍,误判率控制在0.3‰以内(ISO2859-2023标准验证)。
跨行业应用实证分析
在汽车制造业,某主机厂引入该系统后,车门铰链安装孔的定位标识检测合格率从92.4%提升至99.6%,返工成本降低67万元/月。家电行业案例显示,针对洗碗机内胆的耐高温标签,系统在连续48小时高温(120℃)测试中仍保持稳定性能,成功识别出0.3mm级别的烫印缺陷。更为典型的是光伏支架领域,通过户外用钣金件紫外线耐受检测模块,使产品在海南暴晒试验场的标志保持周期延长至8年(国家材料测试中心认证)。
三重质量保障机制
系统构建了覆盖全要素的质量控制网络:1)设备层执行每日GR&R重复性验证(≤10%);2)数据层采用区块链存证技术,确保检测记录不可篡改;3)管理层通过QMS系统实现 实验室标准对接。某航空零部件供应商的审计报告显示,该系统帮助其一次性通过AS9100D认证,关键过程CPK值从1.0提升至1.67。
展望未来,建议行业重点关注三方面发展:首先加快多传感器融合检测设备的国产化进程,打破高端工业相机依赖进口的局面;其次建立基于数字孪生的预测性维护模型,利用5G+边缘计算实现实时质量预警;最后推动钣金件标识检测行业标准的制定,统一不同区域的检测参数和验收规范。只有通过技术创新与标准建设双轮驱动,才能为智能制造战略提供坚实的质量基础。
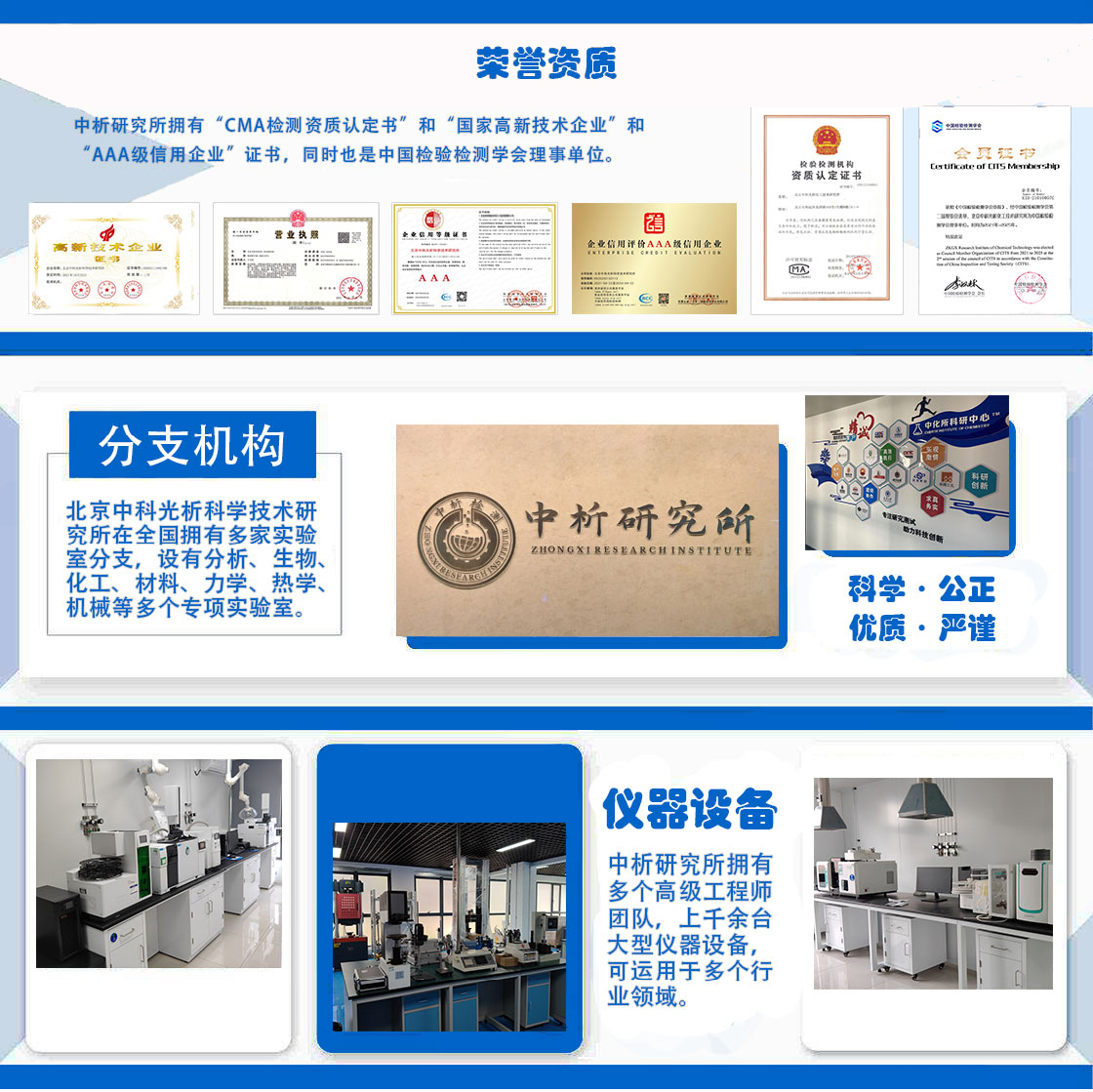
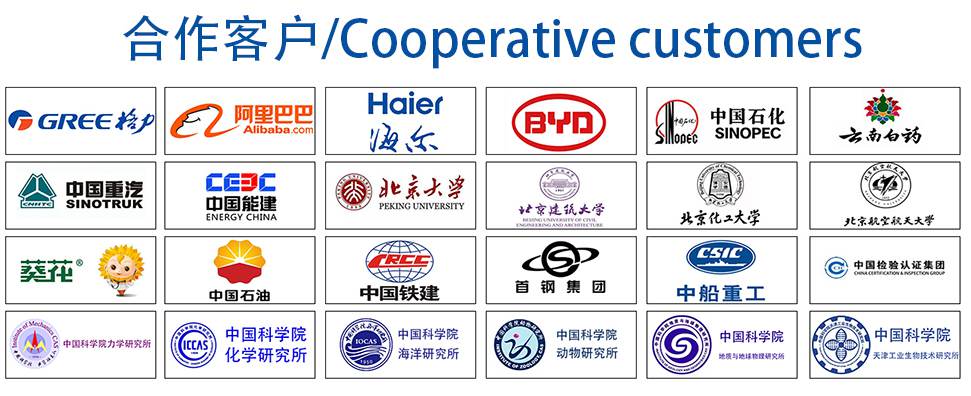