汽车电子/电气零部件检测技术发展与应用白皮书
随着汽车智能化、电动化进程加速,电子电气系统在整车成本中的占比已从2015年的22%提升至2023年的34.5%(据中国汽车工程研究院2024年报告)。在此背景下,汽车电子/电气零部件检测成为保障车辆安全性与可靠性的核心环节。该检测体系不仅涵盖传统ECU控制模块、线束接插件等基础部件,更延伸至智能座舱、自动驾驶域控制器等新型电子架构。其核心价值在于通过全生命周期质量管控,将电子系统故障率降低60%以上(德国TÜV统计数据),同时满足ISO 26262功能安全认证和AEC-Q100车规级标准。尤其在新能源汽车领域,检测项目可有效预防高压系统漏电、电池管理失效等安全隐患,为行业技术升级提供关键支撑。
技术原理与检测体系架构
汽车电子检测采用分层验证模式,包含元器件级、子系统级和整车集成三级验证体系。基于失效模式分析(FMEA)构建的检测矩阵,覆盖电气性能、环境适应性、电磁兼容(EMC)三大维度。以车载充电机(OBC)检测为例,需进行85℃高温满载老化测试、20G机械振动冲击试验及GB/T 18655-2018标准下的辐射发射检测。通过引入边界扫描(Boundary Scan)技术,可实现复杂PCB电路板的自动化诊断,将故障定位效率提升40%。值得关注的是,车规级电子元器件可靠性验证和车载网络系统CAN总线诊断正成为行业重点攻关方向。
全流程实施与质量控制
典型检测流程分为四个阶段:供应商来料检验(IQC)阶段执行AEC-Q200被动元件筛选;工程验证(EVT)阶段开展温度循环(-40℃~125℃)和湿热交变测试;设计验证(DVT)阶段构建包括负载突降、反接保护在内的电气应力测试场景;生产批准(PPAP)阶段建立基于统计过程控制(SPC)的质量数据库。上汽集团某电动平台项目采用该流程后,DC-DC转换器早期故障率从1.2%降至0.35%。目前,智能硬件在环(HIL)测试台架的应用,使检测周期压缩30%的同时,测试用例覆盖率突破95%。
行业应用与效能提升
在智能驾驶领域,某头部企业通过毫米波雷达EMC检测优化,将误报率从每千公里1.8次降至0.5次。具体方案包含在电波暗室中模拟2GHz~8GHz频段干扰,结合雷达信号处理算法迭代。据中国汽车工业协会调研,采用自动化线束导通测试系统的企业,平均减少返修工时1200小时/年。特斯拉上海工厂部署的AI视觉检测系统,可在0.8秒内完成车载显示屏的坏点检测,准确率达到99.97%。这些实践印证了数字化检测在提升制造质量中的关键作用。
质量保障体系创新
行业正在构建三层质量保障架构:底层为 认证实验室的硬件能力建设,中间层覆盖ISO 17025质量管理体系,顶层接入云端大数据分析平台。博世汽车电子苏州检测中心通过部署LIMS系统,实现检测数据自动采集与可追溯性管理,数据完整率从82%提升至99.5%。威马汽车建立的供应商质量指数(SQI)模型,将零部件检测结果与企业售后数据关联,成功将高压配电盒的MTBF(平均无故障时间)提升至8000小时。国家认监委最新数据显示,符合新版CNCA-C11-09认证规则的检测机构,客户投诉率同比下降67%。
面向未来,建议行业重点布局三个方向:其一,建立适应OTA远程升级特性的动态检测机制,应对软件定义汽车带来的验证挑战;其二,开发针对域控制器架构的多物理场耦合测试方案,解决跨域通信的安全验证难题;其三,推动AI赋能的预测性检测技术落地,通过历史数据建模实现潜在故障预警。据中汽研预测,到2026年智能检测装备市场规模将突破280亿元,唯有构建产学研协同创新生态,才能充分释放汽车电子检测的技术红利。
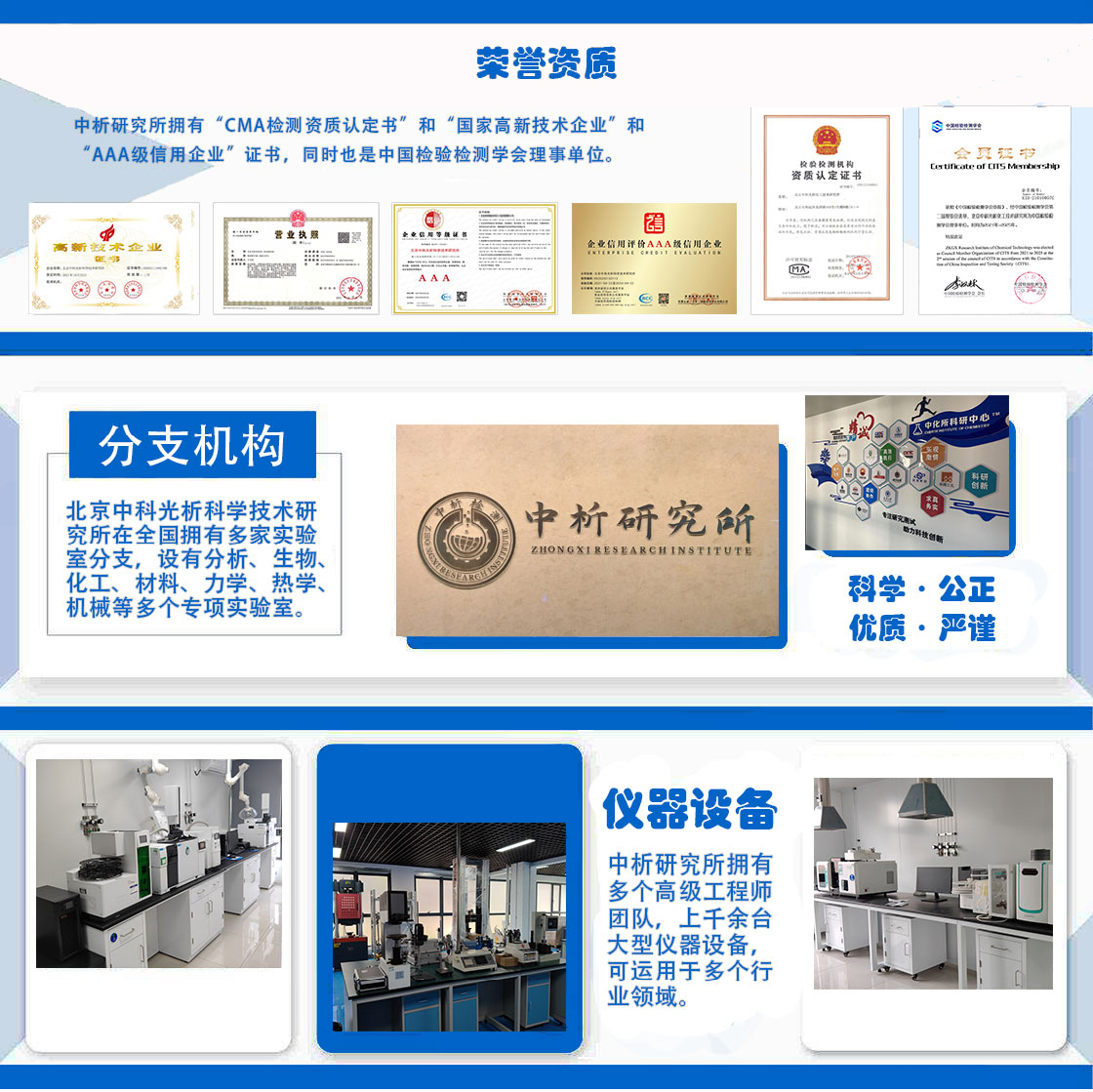
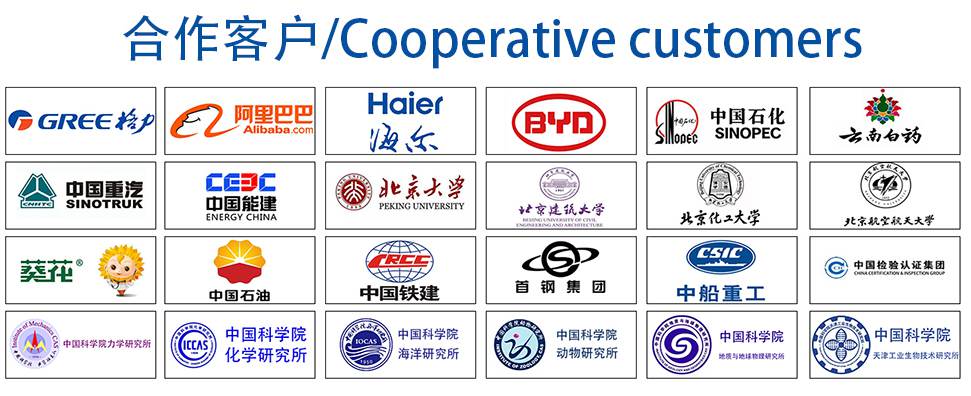