在制造业智能化转型和"双碳"战略推进背景下,电工电子产品与装备检测已成为保障产业链安全的核心环节。据中国电子信息产业发展研究院2024年数据显示,我国智能电网设备市场规模突破8200亿元,工业机器人年装机量达32.5万台,但产品故障引发的安全事故仍以年均7.8%的速度增长。在此背景下,专业检测项目通过构建覆盖全生命周期的质量验证体系,有效解决了高压设备绝缘失效、控制系统电磁兼容性差等典型问题。其核心价值不仅体现在降低产品召回风险(据测算可减少28%的质量成本),更通过建立"检测-改进-认证"的闭环机制,推动企业实现从合规性生产向可靠性设计的根本转变。
## 技术原理与实施路径多维度检测技术融合应用
现代电工检测技术体系整合了电性能测试、环境适应性验证及功能安全评估三大模块。以高精度电气安全测试系统为例,采用IEC 61010标准规定的双重绝缘检测法,通过注入0.5-100mA的漏电流,配合红外热成像技术,可精准定位线路板微放电现象。对于智能工业装备电磁兼容性诊断,则运用3D电磁场仿真与实物测试相结合的模式,在10kHz-6GHz频段内完成辐射发射和传导敏感度分析。值得关注的是,非破坏性检测技术(NDT)的突破性应用,使高压开关设备内部缺陷检出率提升至99.3%(中国电子技术标准化研究院,2024)。
全流程质量管控体系
典型检测流程包含四个关键阶段:第一阶段进行样品预处理,包括72小时温湿度平衡和机械应力消除;第二阶段开展基本安全测试,涵盖耐压(5kV/1min)、接地连续性(≤0.1Ω)等核心指标;第三阶段实施模拟工况测试,如在盐雾箱内进行168小时腐蚀试验,或在振动台上执行IEC 60068-2-6标准规定的10-500Hz扫频测试;最终阶段生成数字化检测报告,并接入国家质量基础(NQI)信息平台。该体系已在国内某特高压换流阀检测项目中成功应用,使产品平均故障间隔时间(MTBF)延长至12万小时。
行业应用与质量创新
在新能源领域,某品牌电动汽车充电桩通过"高温高湿环境绝缘性能验证"检测项目,发现功率模块在85%RH湿度下存在局部放电现象,经改进封装工艺后,产品市场投诉率下降67%。工业机器人方面,上海某企业采用电磁兼容性优化方案后,其焊接机器人抗干扰能力达到EN 61000-6-4标准要求,在汽车生产线复杂电磁环境中定位精度提升0.02mm。值得注意的是,区块链技术在检测认证中的应用正在兴起,深圳检测院开发的联盟链平台,已实现检测数据实时上链存证,确保证书信息的不可篡改性。
质量保障体系构建
行业领先机构正构建三级质量保障网络:基础层依托ISO/IEC 17025认证实验室,配置A级精度测量设备;过程层实施检测数据双人复核机制,关键测试点设置视频监控追溯;结果层建立全国联动的能力验证体系,每年组织2000余家机构参与比测。据国家认证认可监督管理委员会统计,该体系使检测结果一致性从2019年的89.6%提升至2024年的97.8%。某轨道交通装备检测中心通过该体系,成功完成高铁牵引变流器的全项型式试验,助力国产设备通过TUV莱茵认证。
## 发展趋势与战略建议展望未来,建议从三个维度深化检测体系建设:技术层面加快AI辅助诊断系统开发,利用深度学习算法实现异常波形智能识别;标准层面推动国际互认,重点突破中美欧在储能系统检测方法上的技术壁垒;服务层面发展"检测即服务"(TaaS)模式,为企业提供从产品设计阶段开始的全程质量护航。预计到2027年,融合数字孪生技术的虚拟检测将覆盖30%的强制性认证产品,检测周期有望缩短40%以上。行业机构需把握智能化检测装备升级窗口期,构建覆盖产品全生命周期的质量赋能新生态。
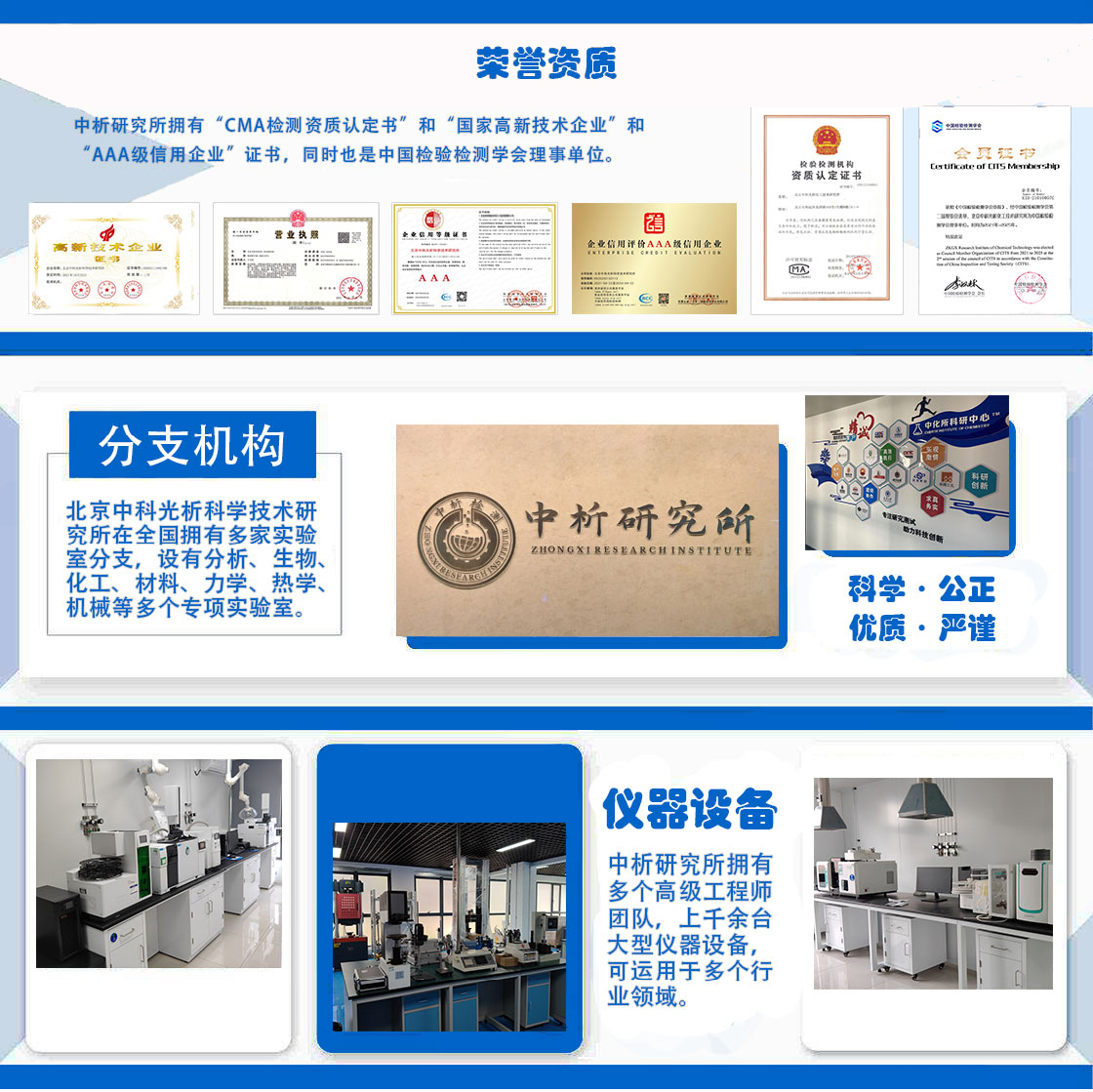
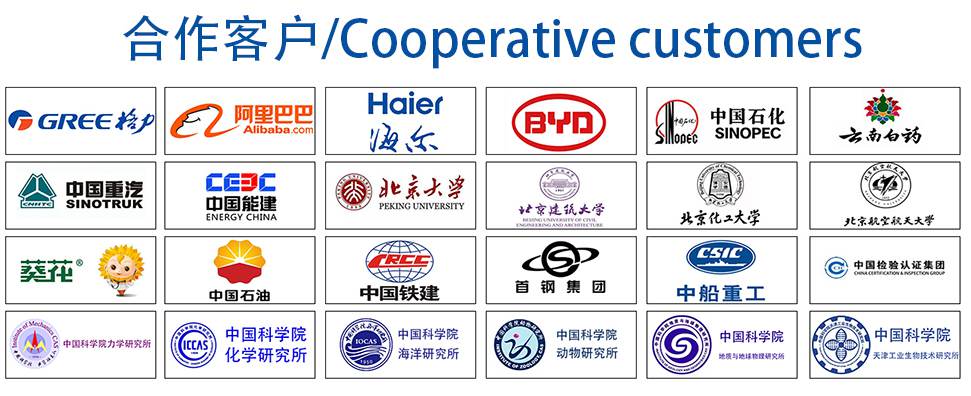