电焊设备节能监测检测的重要性与实施路径
随着工业领域节能减排要求的不断提升,电焊设备作为制造业中能耗较高的工艺设备之一,其节能性能监测与优化已成为企业实现绿色发展的重要课题。根据《中国焊接行业能耗白皮书》统计,电焊设备在工业生产中的电力消耗占比可达5%-10%,而低效设备甚至存在20%以上的能源浪费。通过科学的节能监测检测,不仅能降低企业生产成本,还能显著减少碳排放。目前,我国已出台GB/T 28750-2018《焊接设备节能监测方法》等标准,明确了电焊设备能耗评估的技术规范,为行业提供了检测依据。
电焊设备节能监测的核心检测项目
1. 基础能耗参数检测
包括输入功率、空载功率、负载功率及电能转换效率的实时测量。通过电能质量分析仪记录设备在不同焊接模式下的瞬时能耗曲线,比对国家标准要求的能效限定值,识别设备是否属于高耗能等级。
2. 功率因数与谐波污染检测
使用功率分析仪评估设备的功率因数(要求≥0.85)及电流谐波畸变率(THDi≤30%)。低功率因数会导致线路损耗增加,而谐波超标可能引发电网污染,二者均为能效优化的关键指标。
3. 焊接工艺效率分析
在焊接过程中同步监测电弧电压、焊接电流与有效热输出,计算单位焊材消耗的能源量(kWh/kg)。例如,逆变式焊机应达到85%以上的热效率,而传统工频焊机通常不足70%。
4. 空载与待机能耗检测
通过红外热像仪和电能表连续监测设备非工作状态下的能耗。根据GB 21518-2020标准,电焊设备空载功率不得超过额定功率的2%,智能型设备需具备自动休眠功能。
5. 热效率与散热系统评估
采用热成像技术分析焊机变压器、整流模块等核心部件的温升情况,结合风道设计评估散热效率。设备表面温升超过45℃时,需优化冷却系统以减少额外能耗。
节能检测的技术配套与实施建议
企业应建立三级检测体系:日常巡检(每月)、专项检测(每季度)、全面能效审计(年度)。推荐配置智能化监测终端,例如基于物联网的焊机能耗监测模块,可实时上传数据至MES系统。检测过程中需重点关注焊接参数匹配性,如电流电压的优化组合可降低10%-15%的单点能耗。
节能改造的经济效益测算
以某汽车制造厂为例,通过对200台CO₂气体保护焊机实施能效检测,发现35%的设备存在空载损耗超标问题。经加装自动断电装置及逆变模块升级后,年节电量达72万kWh,节约电费约50万元,投资回收期仅为1.8年。
结语
电焊设备的节能监测检测是实现工业节能降耗的微观切入点。通过系统化的检测项目执行,企业不仅能满足日趋严格的环保法规要求,更能在全生命周期运营中获取持续的经济效益。未来,随着数字孪生、AI能效诊断等新技术的应用,电焊设备节能管理将迈向更高水平的智能化阶段。
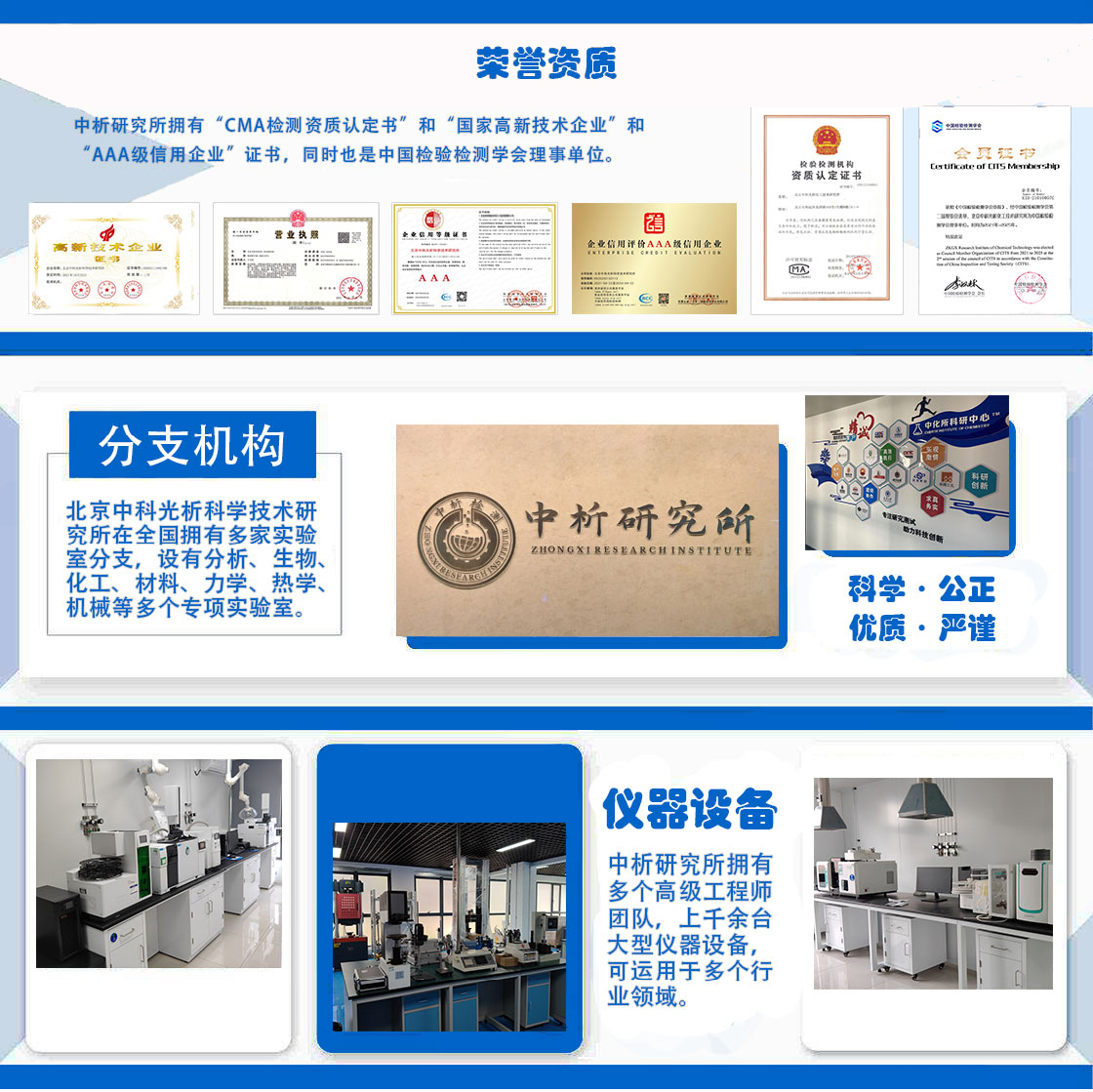
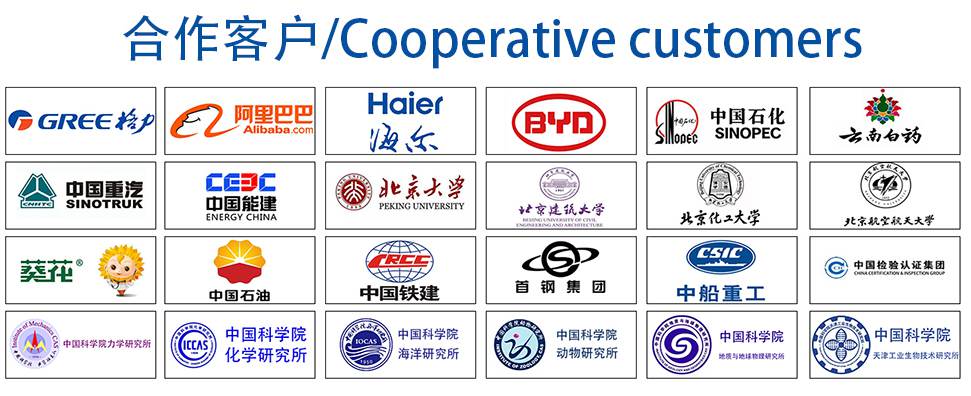