压缩机组系统效率测试检测的重要性
压缩机组作为工业领域中的核心动力设备,广泛应用于石油、化工、电力、制冷等行业,其运行效率直接关系到能源消耗、生产成本及设备寿命。系统效率测试检测是通过科学方法评估压缩机组实际性能与设计指标之间的差异,识别潜在问题并优化运行参数的关键手段。随着“双碳”目标的推进和能效要求的提高,定期开展压缩机组系统效率检测已成为企业节能降耗、提升竞争力的必要环节。
主要检测项目及内容
1. 压缩机入口/出口参数检测
通过高精度传感器测量压缩机入口和出口的气体温度、压力、流量等关键参数,结合热力学公式计算理论功率与实际功率,评估压缩过程的热力学效率。重点关注气体泄漏、阀门启闭延迟等异常现象。
2. 容积效率测试
采用流量对比法或示踪气体法,检测实际排气量与理论排气量的比值,分析由余隙容积、气体泄漏、阀片磨损等因素引起的效率损失。该指标可直观反映压缩机的机械密封性能。
3. 轴功率与机械效率检测
使用扭矩传感器或电功率法测量压缩机输入轴功率,结合等熵效率计算值,评估机械传动系统的损耗(如轴承摩擦、联轴器效率)。通常要求机械效率不低于92%。
4. 系统能效比(EER/COP)测试
对于制冷/热泵系统,需综合测试单位能耗下的制冷量或制热量,重点关注冷却水温度、冷凝压力等外部条件对系统整体能效的影响,确保符合GB/T 18430等国家标准。
5. 振动与噪音监测
采用频谱分析仪检测机组振动加速度和噪声频谱,识别由转子不平衡、轴承磨损或气流脉动引起的异常振动,避免因机械故障导致效率下降。
6. 控制系统响应测试
模拟负载变化场景,验证压力调节阀、变频器等控制元件的响应速度和稳定性,确保系统在不同工况下均能保持最佳效率点运行。
检测方法与技术规范
测试需遵循ISO 1217(容积式压缩机)、ASME PTC-10(离心式压缩机)等国际标准,结合现场工况选用热力学法、示功图法或联合测试法。对于变频机组,还应进行多频段效率特性曲线绘制。检测数据需通过专业软件(如ProSim+、Aspen HYSYS)进行动态模拟与能效对标分析。
结语
通过系统化的效率检测,企业可精准定位压缩机组的能效瓶颈,制定针对性改进方案。建议每5000运行小时或年度大修期间开展全面检测,同时结合实时监控系统实现预防性维护,确保机组始终处于高效、安全、稳定的运行状态。
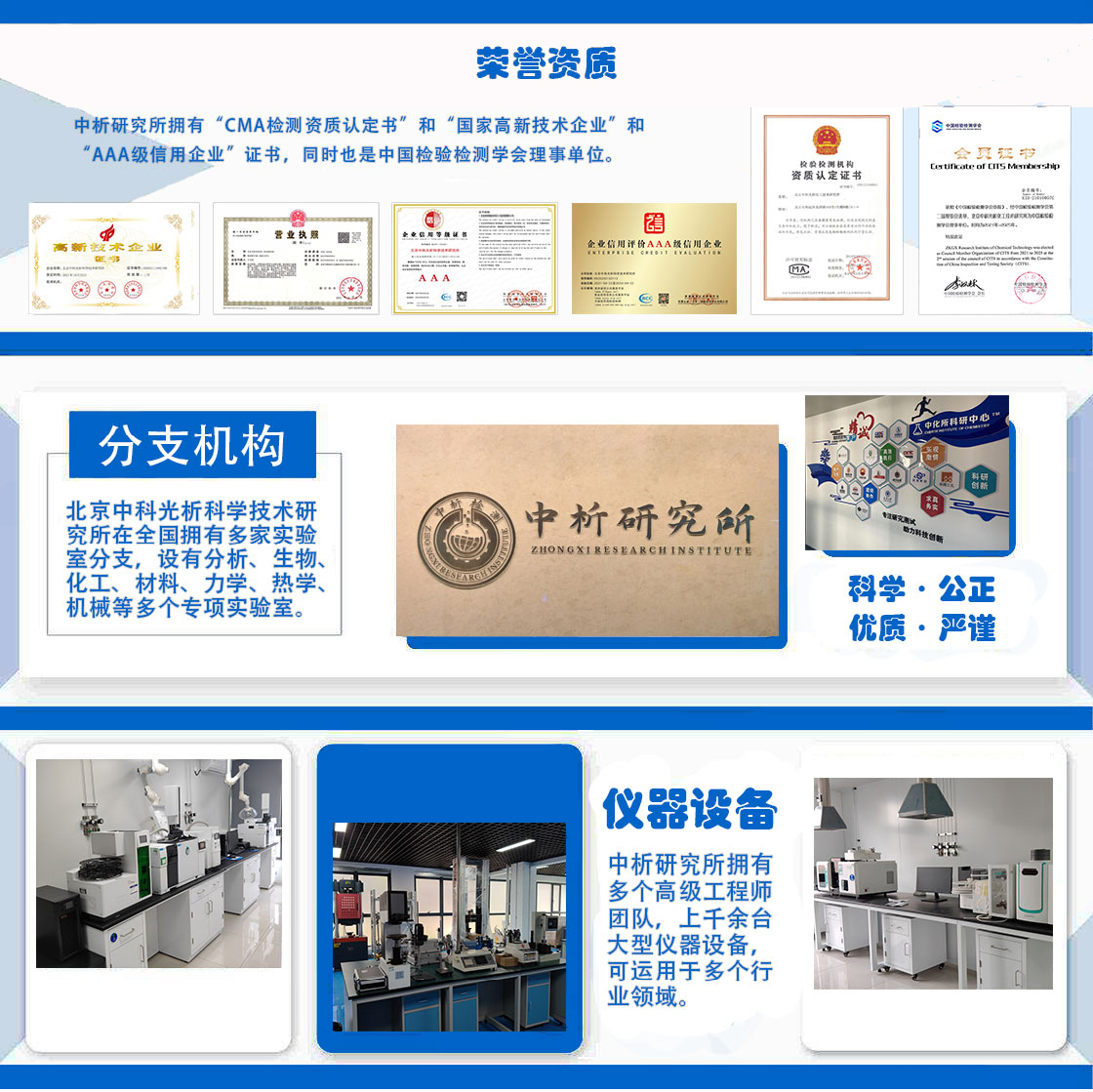
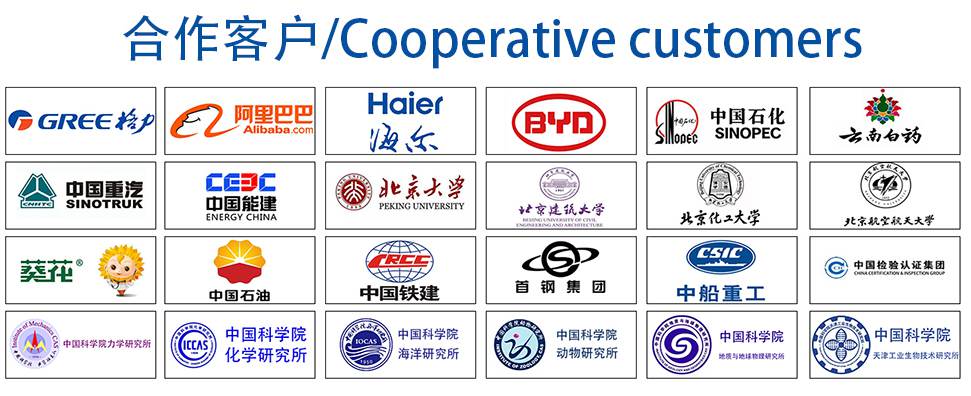