震击器检测:保障井下作业安全的关键环节
震击器作为石油钻井、修井作业中不可或缺的井下工具,其性能直接关系到钻井效率和作业安全。在高压、高温、高腐蚀的复杂井下环境中,震击器需要承受频繁的机械冲击和化学侵蚀。因此,定期开展系统化、标准化的震击器检测,不仅是设备维护的基础要求,更是预防井下事故、延长工具使用寿命的核心保障。
震击器检测的关键项目
1. 机械性能检测
通过液压测试台模拟井下工况,检测震击器的冲击力输出值、工作行程及复位时间。重点验证最大释放能量是否符合API 7-1标准,使用应变片测量关键部位的应力分布,确保结构强度满足设计要求。
2. 密封性能检测
采用氦气检漏仪对震击器密封组件进行气密封测试,检测压力范围需覆盖0-70MPa工况。同时进行持续72小时的高压持压试验,观察压力衰减值是否控制在3%以内,确保防喷器组件的可靠性。
3. 材料抗性检测
使用光谱分析仪对本体材料进行化学成分检测,重点监控Cr、Mo、Ni等合金元素含量。通过金相显微镜观察材料微观结构,配合洛氏硬度计测试表面硬度(通常要求HRC 28-32),评估材料的抗硫化氢腐蚀能力。
4. 功能性测试
在模拟井筒装置中,测试震击器在不同倾斜角度(0-90°)下的触发响应时间和冲击传递效率。使用加速度传感器记录冲击波形,分析峰值加速度是否达到120g以上,同时检测重复工作时的性能稳定性。
专业检测的技术要求
检测机构需配备符合ISO/IEC 17025标准的实验室环境,检测人员须持有API Q2认证资质。动态测试时应采用不低于200Hz采样率的数采系统,扭矩检测精度需达到±1%。每台震击器应建立完整的检测档案,记录包括震动频谱分析、金属磁记忆检测等30余项数据参数。
通过实施全面的震击器检测体系,可有效预防因工具失效导致的卡钻、井喷等重大事故。建议每完成3次井下作业或累计工作150小时后即进行预防性检测,确保设备始终处于最佳工作状态。
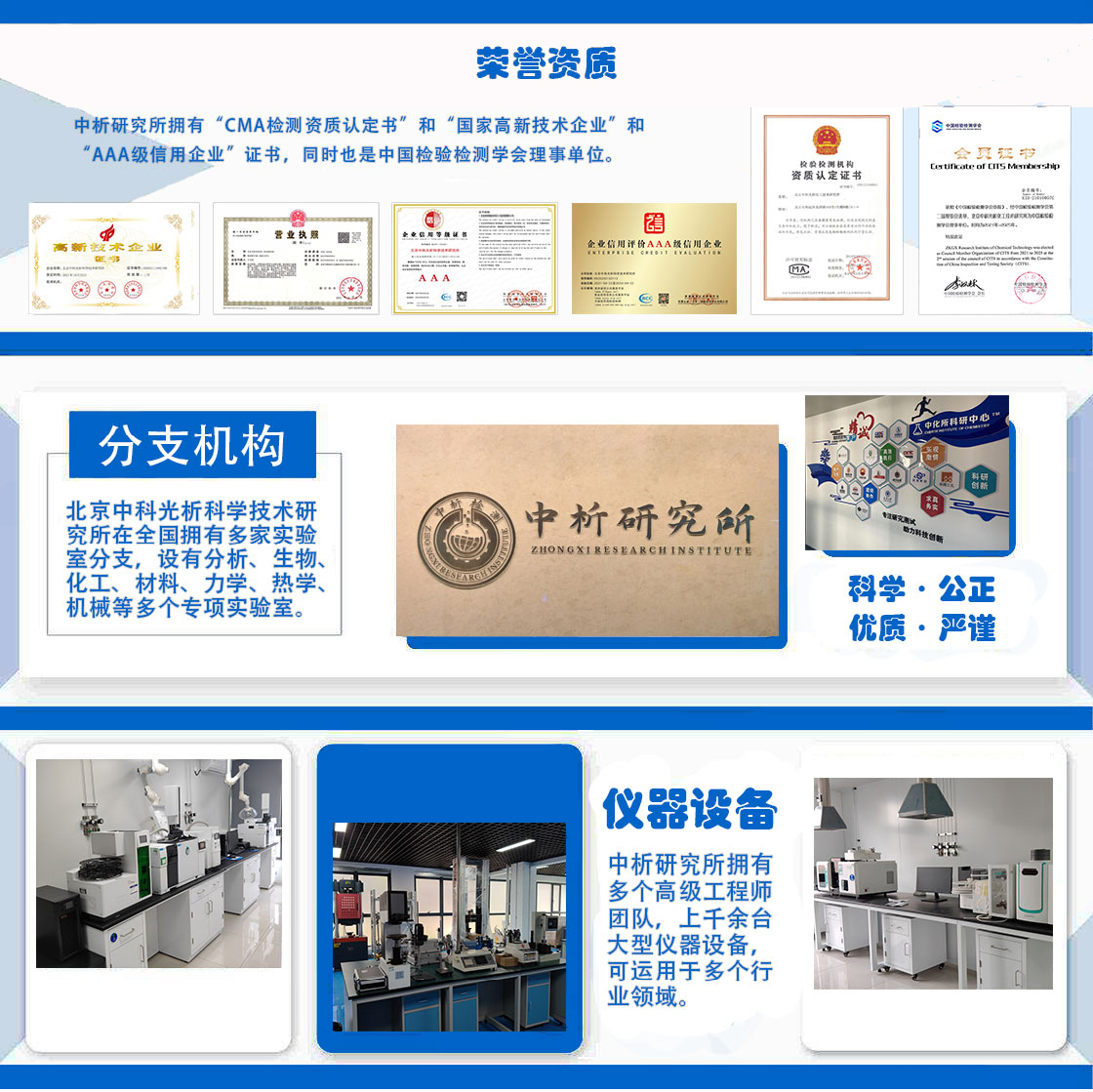
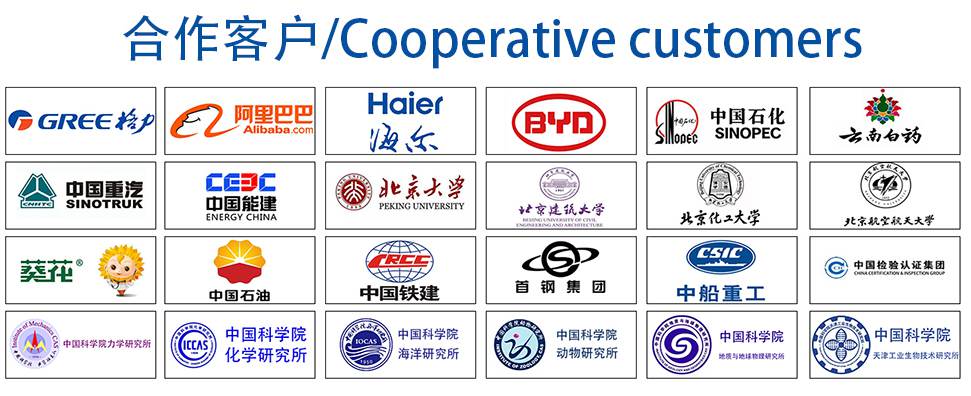