防爆机械检测的重要性与核心内容
防爆机械作为石油化工、矿山开采、粉尘加工等高风险行业的关键设备,其安全性能直接关系到人员生命安全和生产稳定性。由于这些设备长期处于易燃易爆环境中,任何结构缺陷或功能失效都可能引发灾难性事故。因此,定期开展防爆机械检测不仅是国家强制性安全规范的要求,更是企业实现风险防控的核心环节。检测工作需依据GB 3836《爆炸性环境用电气设备》系列标准、ISO 80079等国际国内技术规范,通过系统化评估确保设备在设计、制造和使用阶段的防爆性能符合要求。
防爆机械检测的核心项目
1. 防爆结构完整性检测
重点检查设备外壳的机械强度、隔爆接合面参数(如间隙宽度、表面粗糙度)是否符合标准。使用激光测距仪、三坐标测量仪等工具验证隔爆腔体的密封性,确保爆炸压力能被有效阻隔。对于增安型设备,需额外评估内部元件的绝缘性能与温升控制能力。
2. 材料与表面处理检测
分析设备材质是否具备抗静电、耐腐蚀特性,通过光谱仪检测金属成分,验证铝合金外壳的镁含量是否低于6%。表面涂层需进行附着力测试和电阻值测量,避免静电积聚风险。特殊工况下还需评估材料的高温抗氧化能力。
3. 电气系统安全性验证
对电路进行绝缘电阻测试(标准值≥1.5MΩ)、耐压试验(2U+1000V,历时10s)和接地连续性检测。检查接线端子的防松动设计,评估本安回路中限流电阻、隔离栅等保护元件的参数匹配性,确保在短路或过载时能可靠切断能量传输。
4. 防护等级(IP)与机械性能测试
通过IP6X防尘试验和IPX7防水试验验证外壳防护能力。对移动式防爆机械进行振动与冲击测试(如5Hz-150Hz扫频振动),检查紧固件是否松动、结构件是否变形。同时需验证设备在额定负载下的连续运行稳定性。
5. 安全保护装置功能性检测
测试超温报警、过载断电、气体浓度监测等联锁装置的动作灵敏性。使用热成像仪监测电机温升,验证散热系统的有效性。对防爆叉车的机械制动系统进行动态响应测试,确保紧急制动距离符合ATEX指令要求。
6. 环境适应性评估
模拟设备在爆炸性气体(IIA/IIB/IIC类)或粉尘(IIIA/IIIB/IIIC类)环境中的运行状态,检测隔爆面是否因腐蚀或磨损导致性能下降。对于海洋平台等特殊场景,还需进行盐雾试验和防爆结合面长效密封性验证。
检测周期与管理要求
根据TSG 21-2016《固定式压力容器安全技术监察规程》,防爆机械应每年进行一次全面检测,日常维护需包含月度点检与季度专项检查。检测机构须具备 防爆实验室认证资质,检测报告需明确设备防爆等级(如Ex d IIB T4 Gb)、失效部件清单及整改建议。企业应建立设备健康档案,实现检测数据的动态化管理。
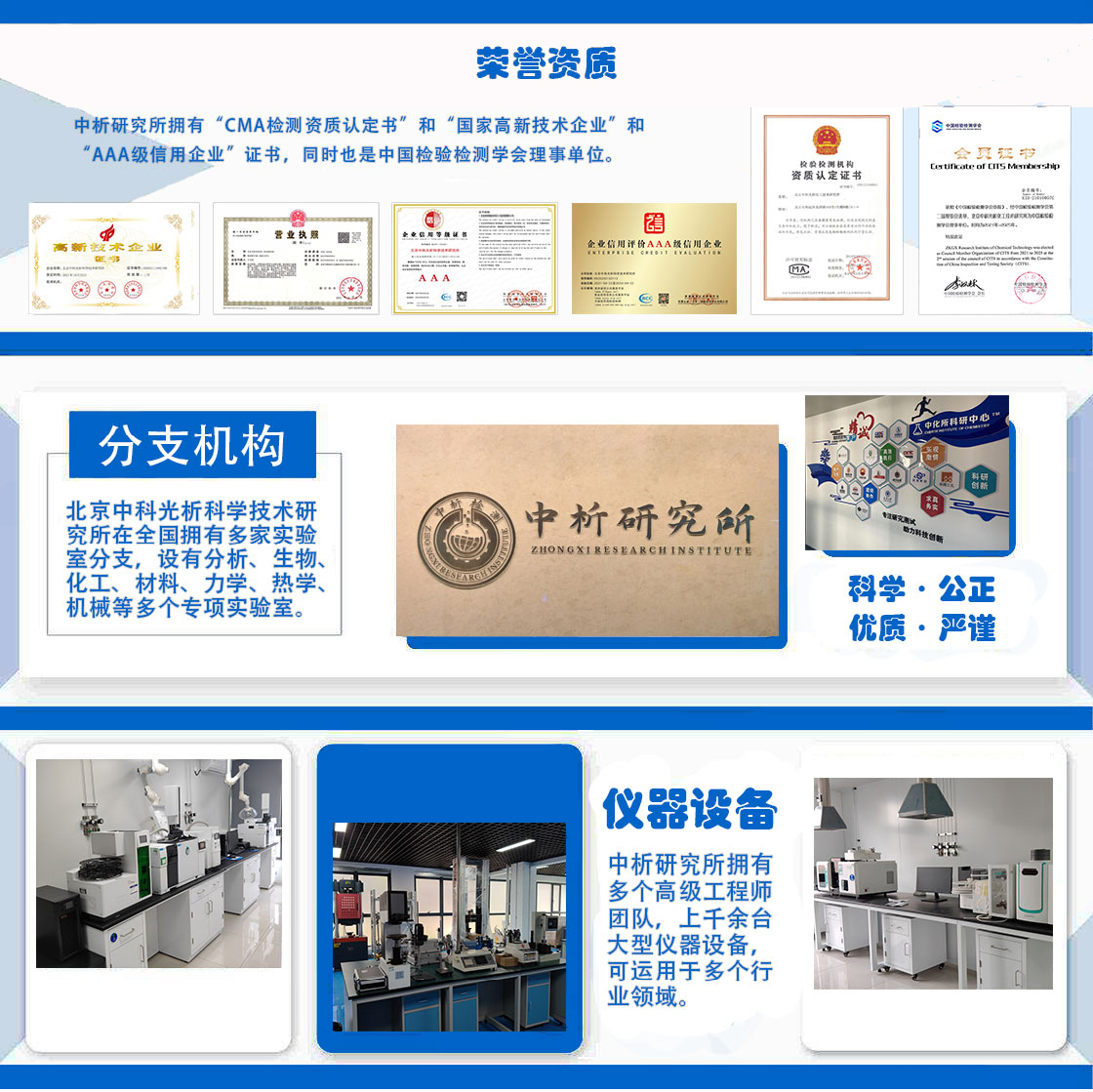
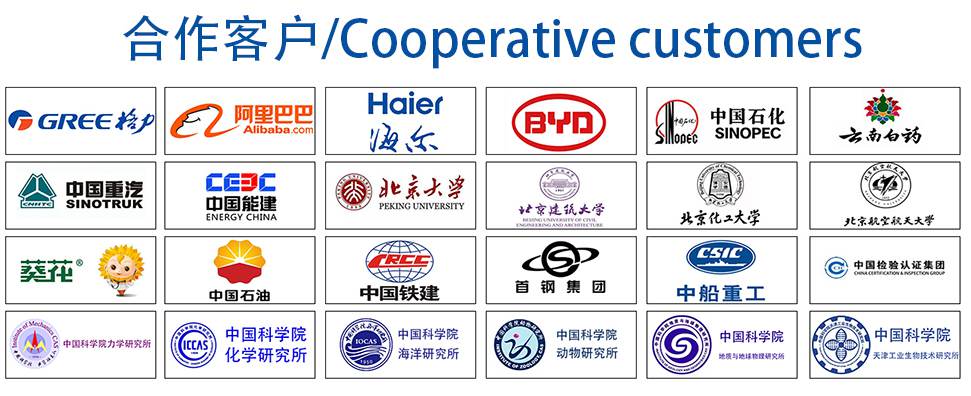