修井用铣鞋及磨鞋检测的重要性
在石油和天然气开采作业中,修井用铣鞋及磨鞋是井下作业的核心工具,用于清除井筒内残留物、修复套管损伤或打捞落井设备。由于井下环境复杂(高温、高压、腐蚀性介质等),工具的可靠性直接关系到作业安全和效率。若铣鞋或磨鞋存在质量缺陷,可能导致工具断裂、作业停滞甚至井筒损坏等严重后果。因此,对其制造质量和使用性能进行系统性检测,是保障钻井工程顺利实施的必要环节。
核心检测项目及方法
1. 尺寸与几何精度检测
铣鞋及磨鞋的尺寸公差直接影响其与井筒的匹配性。需通过三坐标测量仪、卡尺等工具检测外径、内径、齿高、刃口角度等关键参数,确保符合API标准或企业技术规范。例如,铣鞋的切削齿间距误差需控制在±0.5mm以内,避免局部应力集中导致的过早磨损。
2. 材料性能检测
通过光谱分析仪验证材料的化学成分是否符合设计要求(如耐磨合金钢的Cr、Mo含量),同时进行硬度测试(洛氏硬度HRC)、冲击韧性试验和金相组织观察。重点检测焊接部位是否存在晶间腐蚀或热影响区脆化现象,确保其在井下高强度作业中的抗疲劳性能。
3. 表面质量与失效分析
使用渗透探伤(PT)或磁粉探伤(MT)检测工具表面裂纹、气孔等缺陷;通过电子显微镜观察磨损形貌,分析磨损失效模式(如磨粒磨损、粘着磨损)。对于返厂修复工具,需额外评估补焊区域与基体材料的结合强度,避免二次作业中出现剥落风险。
4. 动态性能模拟测试
在实验室模拟井下工况(转速200-500rpm、轴向载荷5-20吨),通过扭矩传感器和振动监测系统记录工具的切削效率与稳定性。同时利用高压釜进行腐蚀性介质(如H₂S、CO₂)环境下的加速老化试验,预测工具的实际使用寿命。
5. 特殊功能验证
针对具有水力喷射功能的铣鞋,需进行流量-压力曲线测试,验证流道设计是否合理;对于可更换齿结构的磨鞋,需进行重复拆装试验,评估螺纹连接部位的抗松动性能。此外,需检查密封件的耐温耐压能力(最高175℃/70MPa)。
检测标准与规范
检测过程应严格遵循API SPEC 7-1、ISO 10424等国际标准,并结合SY/T 5112-2016《石油天然气工业井下工具检测规范》等国内行业要求。第三方检测机构需具备 或CMA认证资质,确保检测结果的权威性和可追溯性。
结语
随着非常规油气资源开发规模的扩大,修井作业对铣鞋及磨鞋的性能要求日益提高。通过多维度检测手段,可有效识别工具潜在缺陷,优化生产工艺,延长工具服役周期,最终降低综合作业成本。建议企业建立全生命周期检测档案,结合大数据分析实现预测性维护,推动井下工具管理的智能化转型。
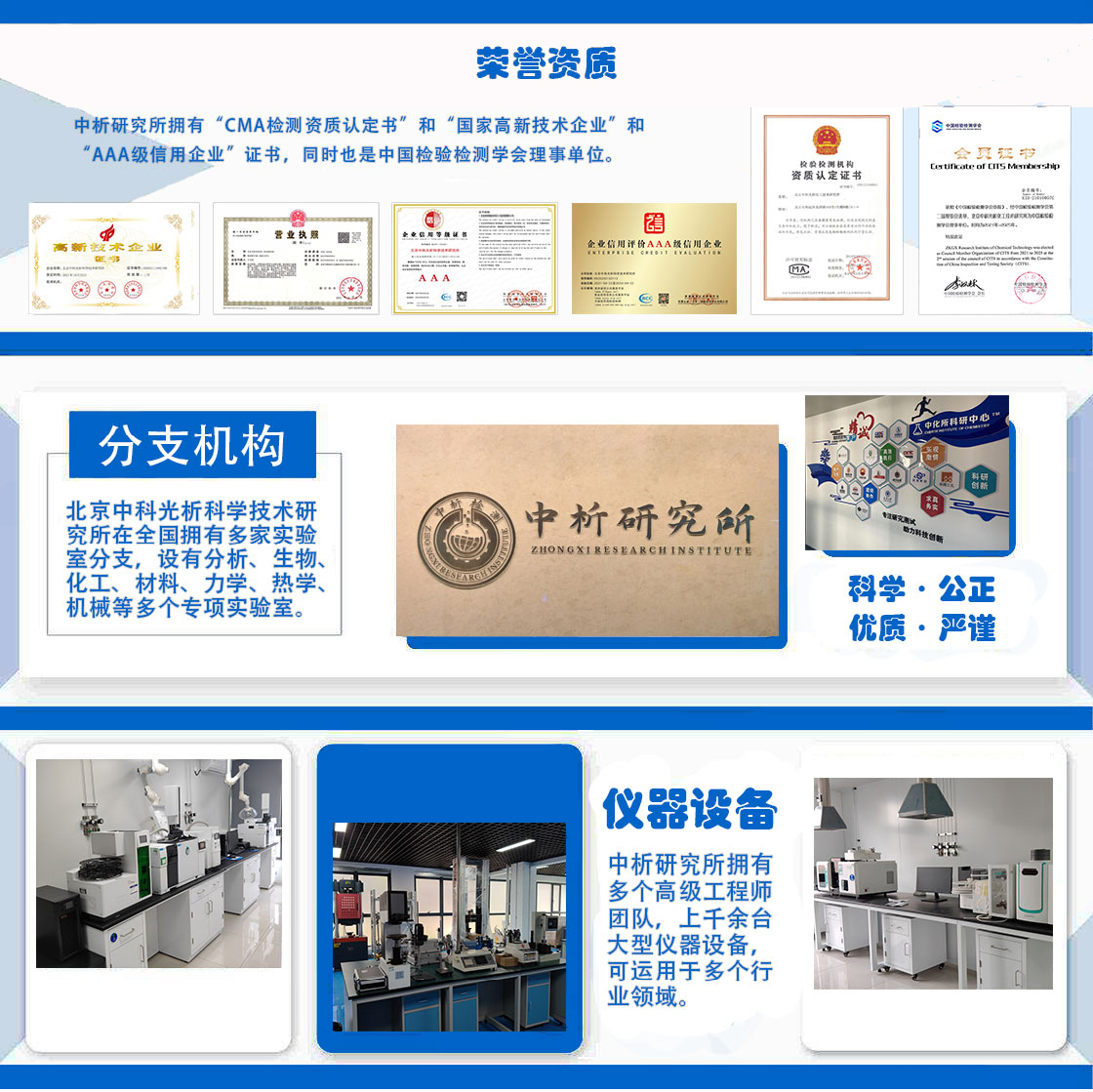
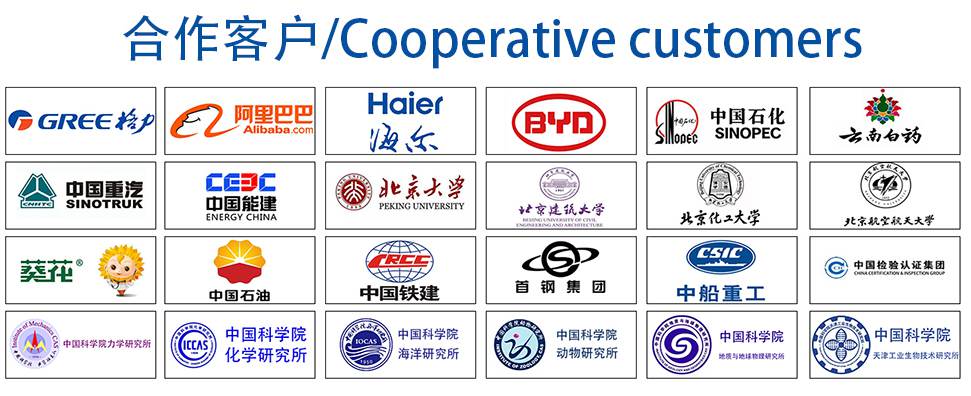