奥氏体-铁素体型双相不锈钢焊接钢管在热交换器应用中的关键检测项目
奥氏体-铁素体型双相不锈钢焊接钢管因其优异的耐腐蚀性、高强度和抗应力腐蚀性能,被广泛应用于石油化工、电力及海洋工程等领域的热交换器制造。作为热交换器的核心传热元件,其质量直接关系到设备的安全性、能效和使用寿命。为确保焊接钢管在高温、高压及腐蚀性介质环境下的可靠性,需通过系统化的检测项目对原材料及成品进行严格质量控制。
1. 化学成分分析
通过光谱分析仪或化学滴定法检测钢管母材及焊缝区域的化学成分,重点验证C、Cr、Ni、Mo、N等关键元素的含量是否符合标准(如ASTM A789/A789M)。双相不锈钢的相比例(奥氏体与铁素体的体积比)需控制在40%-60%,元素偏差可能导致相平衡破坏。
2. 机械性能测试
包括拉伸试验(检测抗拉强度、屈服强度及延伸率)、硬度测试(布氏/维氏硬度)及冲击韧性试验。热交换器用管需满足在高温工况下的机械稳定性,焊接接头区域的强度衰减值不得超过母材的15%。
3. 金相组织检验
采用金相显微镜观察微观组织,评估奥氏体与铁素体相的分布均匀性。通过腐蚀试验(如按ASTM A923方法)检测是否存在σ相、氮化物等有害析出物,防止晶间腐蚀风险。
4. 耐腐蚀性能检测
进行点蚀临界温度(CPT)、缝隙腐蚀试验及应力腐蚀开裂(SCC)试验。针对热交换器常见的Cl-腐蚀环境,需确保钢管在模拟工况下的耐局部腐蚀能力满足ASME BPV规范要求。
5. 尺寸与形位公差测量
使用激光测径仪、超声波测厚仪等设备检测钢管的外径、壁厚、椭圆度及直线度。对于焊接管,需特别关注焊缝余高(≤0.5mm)和错边量(≤10%壁厚),避免流动阻力增大和应力集中。
6. 焊缝质量检测
采用X射线/超声波探伤检测焊缝内部缺陷,配合渗透检测(PT)或磁粉检测(MT)检查表面裂纹。根据ASME Section VIII标准,焊缝缺陷应满足Ⅱ级合格要求,气孔、夹杂等缺陷尺寸需严格管控。
7. 水压试验与气密性试验
按设计压力的1.5倍进行水压试验,保压时间不少于10秒;对存在致密性要求的管束,需进行氦检漏试验,泄漏率应低于1×10^-9 Pa·m³/s。
通过上述检测项目的系统实施,可有效保障奥氏体-铁素体双相不锈钢焊接钢管的服役性能,为热交换器的安全稳定运行提供技术支撑。随着检测技术智能化发展,基于数字孪生的在线监测体系正在成为行业质量控制的新趋势。
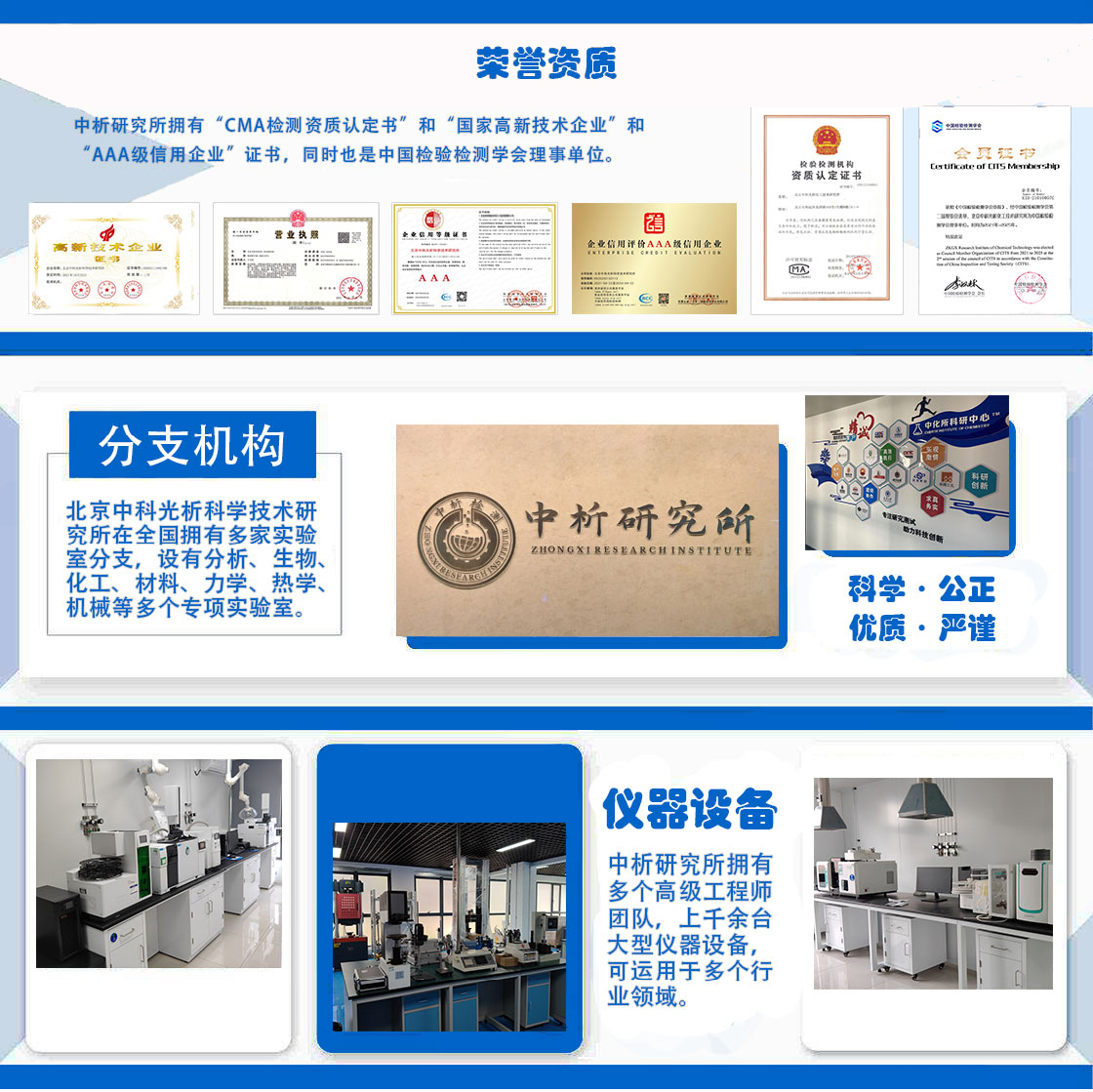
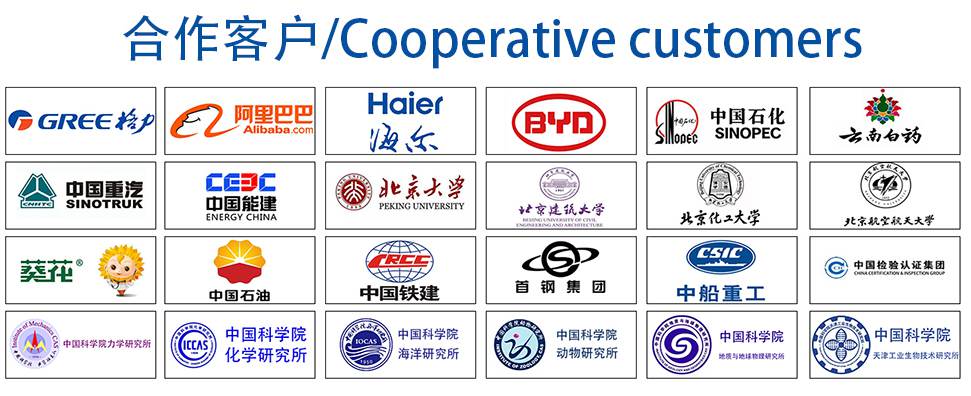