炭黑用焦化原料油检测的重要性
炭黑作为一种重要的工业原料,广泛应用于橡胶、塑料、油墨、涂料等领域,其生产过程中焦化原料油的质量直接决定了炭黑的物理化学性能及最终产品的稳定性。焦化原料油通常来源于煤焦油、石油渣油等高温裂解产物,其成分复杂且易受生产工艺、储存条件等因素影响。若原料油中含有过量杂质、金属离子或未完全裂解的组分,可能导致炭黑产品分散性差、导电性异常、结构度不稳定等问题。因此,对焦化原料油进行系统性检测是保障炭黑品质、优化生产流程的核心环节。
关键检测项目及意义
1. 密度与黏度检测
密度和黏度是焦化原料油的基础物理指标,直接影响其在炭黑反应炉中的雾化效果和裂解效率。通过密度计和旋转黏度计可测定油品流动性,若黏度过高可能导致喷嘴堵塞,而密度异常则可能反映杂质含量或组分偏差。
2. 残炭值测定
残炭值反映原料油在高温裂解后残留的固体碳含量,是评估其成炭性能的关键参数。过低的残炭值可能导致炭黑产率下降,而过高值则可能引发反应炉结焦。通常采用康氏残炭法(Conradson Carbon Residue)进行测试。
3. 硫含量分析
硫元素对炭黑的表面活性和环保性具有显著影响。通过X射线荧光光谱(XRF)或紫外荧光法测定硫含量,超标硫分不仅会降低炭黑在橡胶中的补强效果,还可能在生产中释放有害气体,需严格控制。
4. 馏程与挥发分检测
通过蒸馏试验确定原料油的初馏点、终馏点及馏程分布,可评估其轻重组分比例。挥发分过高会导致反应炉温度波动,影响炭黑结构的均匀性;而重质组分过多则可能增加结焦风险。
5. 芳烃与沥青质含量
芳烃是生成炭黑骨架结构的主要成分,其含量需通过色谱法或质谱法测定。高芳烃油品有利于形成高比表面积的炭黑,但沥青质含量超过3%时易导致反应炉积碳,需结合工艺参数调整原料配比。
6. 金属离子检测
采用原子吸收光谱(AAS)或ICP-MS检测钠、铁、镍等金属含量。金属杂质会催化副反应,导致炭黑颗粒团聚或灰分超标,尤其在轮胎用炭黑中需将总金属含量控制在50ppm以下。
7. 灰分测定
通过高温灼烧法测定灰分含量,可直接反映原料油中无机杂质的水平。灰分过高会降低炭黑的纯度,影响其在高端领域的应用,需确保灰分≤0.05%(质量分数)。
8. 水分与机械杂质检测
水分会导致反应炉热效率降低,而机械杂质(如焦粉、粉尘)可能堵塞设备。采用卡尔费休法测定微量水分,机械杂质则通过过滤称重法检测,通常要求水分≤0.5%、杂质≤0.1%。
检测数据的综合应用
上述检测结果需结合生产工艺参数建立数据库,通过统计过程控制(SPC)分析各指标间的相关性。例如,当残炭值与芳烃含量呈正相关时,可通过调整原料油混合比例实现炭黑DBP吸油值的精准调控。生产企业应建立动态检测机制,确保原料油批次间质量稳定,为生产高性能炭黑提供可靠保障。
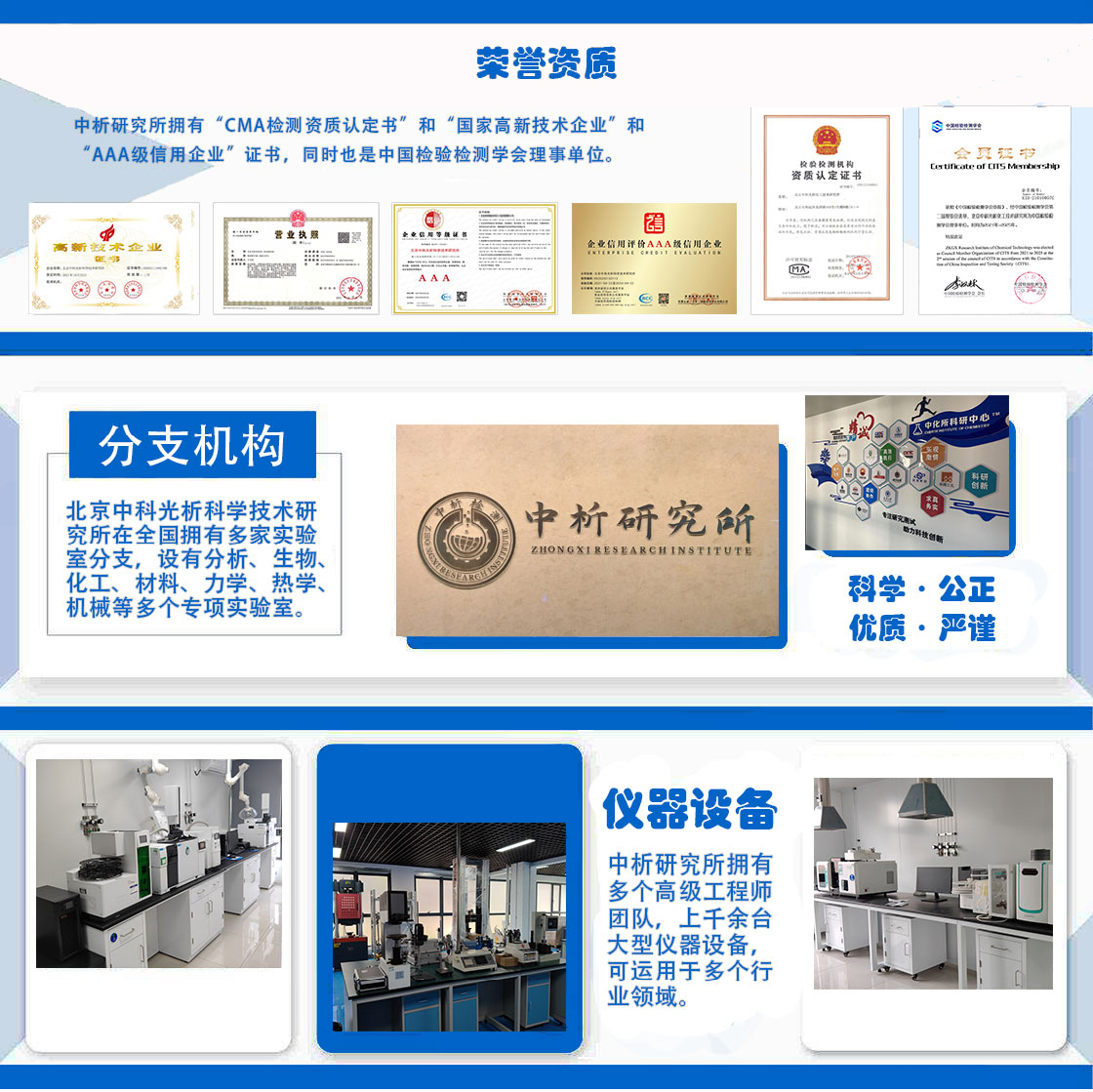
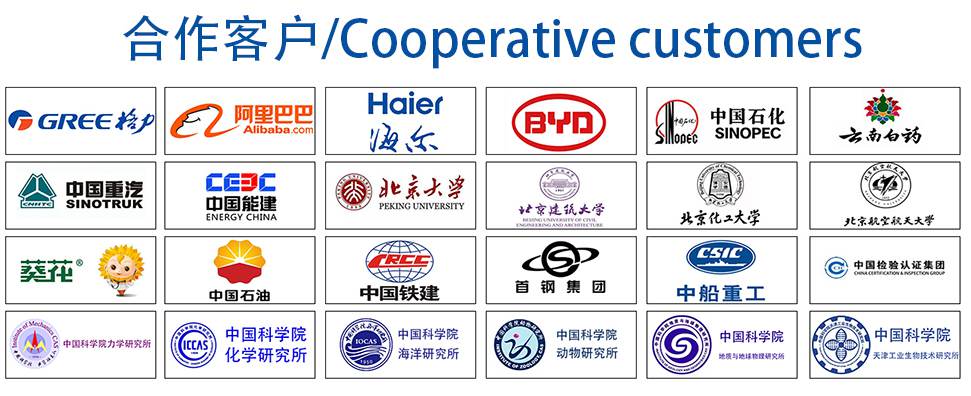