相控阵超声探伤仪检测:原理与应用
相控阵超声探伤仪(Phased Array Ultrasonic Testing, PAUT)是近年来工业无损检测领域的重要技术突破。与传统超声检测相比,其通过电子控制多个晶片阵列的声束偏转与聚焦,能够实现多维、高精度的缺陷检测。该技术广泛应用于航空航天、轨道交通、石油化工、核电能源等领域,尤其在复杂几何结构或高安全性要求的部件检测中表现卓越。检测项目的多样性和精准性使其成为保障设备安全运行的核心工具。
核心检测项目解析
1. 焊缝质量检测
相控阵超声探伤仪可对金属焊缝(如管道、压力容器等)的内部裂纹、未熔合、气孔等缺陷进行高灵敏度检测。通过多角度声束扫描和动态聚焦技术,能够生成焊缝截面成像(C扫描或S扫描),直观显示缺陷位置、尺寸和走向,显著提升检测效率与准确性。
2. 复合材料分层与孔隙率检测
针对碳纤维复合材料、层压结构等非均质材料,PAUT可识别微小分层、脱粘及孔隙缺陷。其高频声波(可达20 MHz)能够穿透多层结构,结合扇形扫描模式,精确量化缺陷深度与面积占比,满足航空航天部件的严格质量要求。
3. 铸件与锻件内部缺陷分析
在大型铸锻件(如涡轮叶片、曲轴)的检测中,相控阵技术可有效检测缩孔、夹杂、疏松等内部缺陷。通过调整声束角度和聚焦深度,能够穿透厚壁工件(可达500 mm以上),生成三维缺陷分布图,辅助工艺优化与寿命评估。
4. 腐蚀与壁厚测量
针对管道、储罐等设备的腐蚀损伤,PAUT可进行高精度壁厚测绘,最小分辨率可达0.1 mm。通过线性扫描与全聚焦模式(TFM),能够识别点蚀、均匀腐蚀及局部减薄区域,并提供剩余壁厚趋势分析,为维护决策提供数据支撑。
5. 复杂几何结构检测
对于异形部件(如法兰、弯头、齿轮齿根等),相控阵技术通过动态声束偏转功能,实现无死角检测。其自适应扫描方案可匹配曲面轮廓,解决传统探头接触不良或盲区问题,显著提升检测覆盖率。
技术优势与挑战
相控阵超声探伤仪的核心优势在于:① 多维度成像能力;② 检测参数可编程化;③ 数据可追溯性。然而,其技术要求较高,需配合专业软件分析,且设备成本相对昂贵。未来,随着人工智能算法的集成与便携式设备的普及,PAUT将在智能化检测领域进一步突破。
行业应用场景
在核电领域,相控阵技术用于反应堆压力容器焊缝的定期检测;在轨道交通中,车轴、轮对等关键部件依赖PAUT保障运行安全;石化行业则通过其监控高温管道的应力腐蚀裂纹。检测项目的标准化(如ASTM E2700、ISO 20601)进一步推动了技术的规范化应用。
结语
相控阵超声探伤仪通过创新的检测项目与灵活的技术方案,正在重塑工业无损检测的格局。随着制造业对质量与安全要求的提升,该技术的应用边界将持续扩展,为设备全生命周期管理提供更强大的技术支撑。
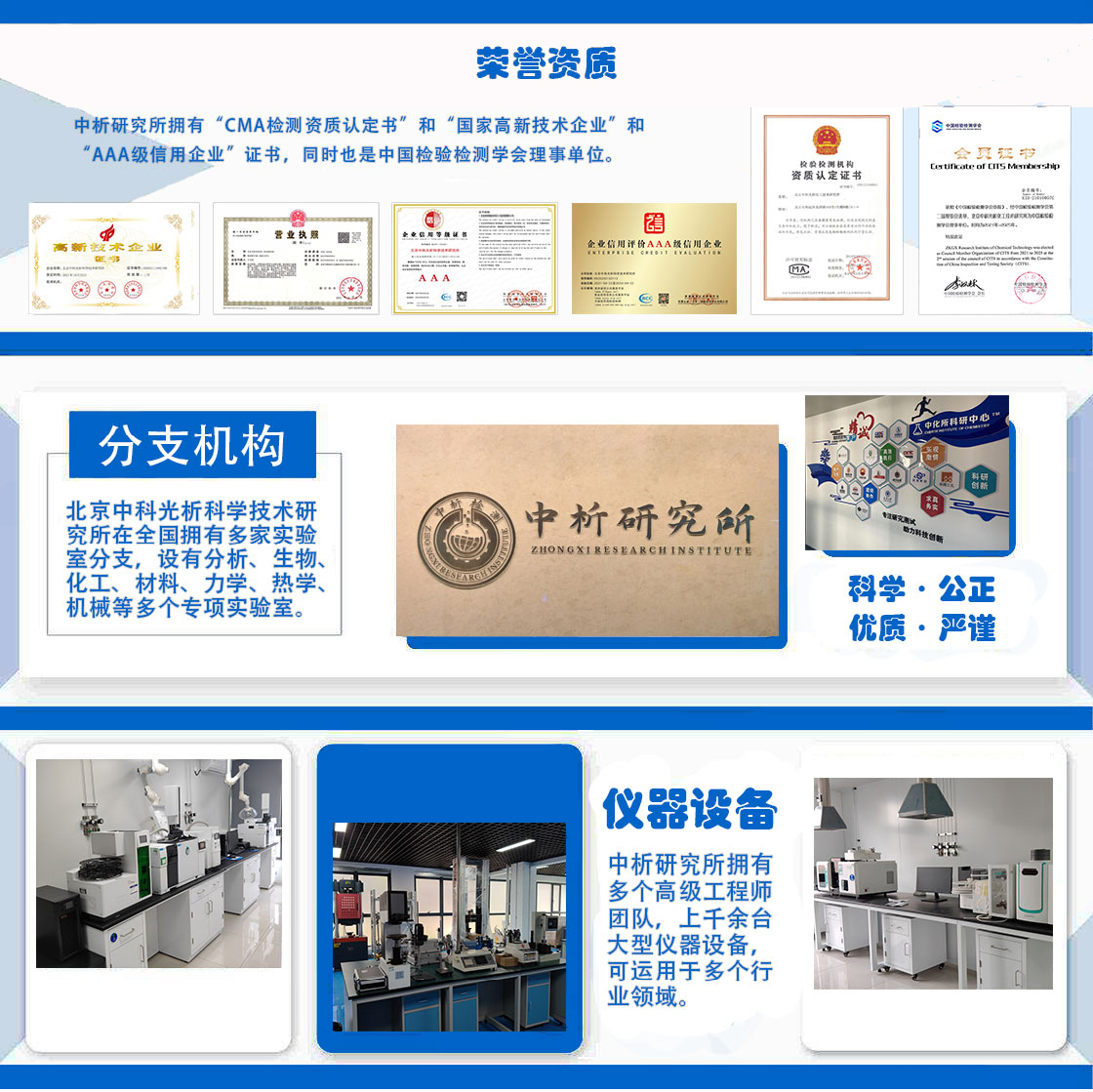
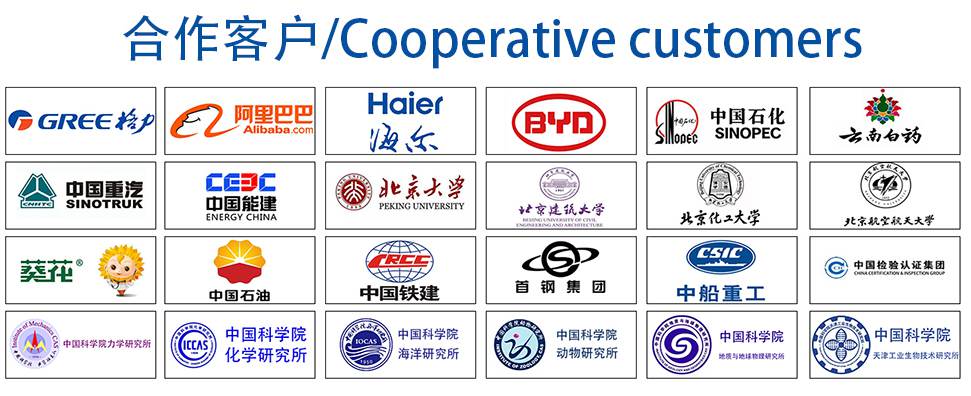