工业机器人参数检测的重要性与实施流程
随着智能制造技术的快速发展,工业机器人已成为现代制造业的核心装备之一。其性能参数直接决定了生产效率、产品质量及生产安全性。工业机器人参数检测是确保设备出厂质量、运行稳定性和长期可靠性的关键环节。通过系统化检测,企业能够验证机器人是否达到设计指标,识别潜在隐患,并为后续调试、维护提供数据支持。典型的检测内容涵盖机械性能、电气特性、运动精度、环境适应性等多个维度,需结合国际标准(如ISO 9283、GB/T 12642)与行业规范执行。
核心检测项目及技术要点
1. 定位精度与重复定位精度检测
通过激光跟踪仪或三坐标测量机(CMM)对机器人末端执行器的空间位置进行高精度测量,计算实际位置与指令位置的偏差。重复定位精度需连续执行100次以上相同路径操作,统计最大偏差值和标准差,确保符合±0.05mm等级要求。
2. 负载能力与力矩性能检测
采用动态力传感器和转矩测试仪,分别测试机器人额定负载下的关节力矩、末端最大承载重量及过载保护功能。需模拟不同工况(如加速、急停)下的力矩波动曲线,验证传动系统刚性是否符合ISO 10218标准。
3. 运动速度与加速度特性检测
使用高速摄像系统或光电编码器记录各轴运动轨迹,分析最大速度、加速度平滑度及轨迹跟踪误差。重点关注加减速阶段的振动抑制能力,避免因动态性能不足导致加工件表面质量缺陷。
4. 电气系统安全检测
包括绝缘电阻测试(≥100MΩ)、接地连续性(≤0.1Ω)、紧急停止响应时间(≤0.5s)等项目。需使用兆欧表、接地电阻仪等设备,结合功能安全标准(IEC 61508)验证控制系统的可靠性。
5. 环境适应性测试
在温湿度试验箱中模拟-10℃~50℃工况,持续运行48小时检测机器人润滑系统、电子元件的工作状态。同时进行粉尘防护(IP等级)和抗电磁干扰(EN 61000标准)测试,确保复杂环境下的稳定运行。
6. 通讯协议兼容性验证
通过PROFINET、EtherCAT等工业总线协议分析仪,测试机器人控制器与PLC、视觉系统的数据交互能力。需验证指令延迟(≤2ms)、数据丢包率(≤0.01%)等关键指标,保证生产线的协同效率。
检测数据管理与智能化趋势
现代检测系统已集成数据采集、分析和可视化功能,可通过数字孪生技术实现参数预测性维护。基于AI算法的异常检测模型能自动识别关节磨损、谐波减速器失效等潜在故障,推动检测效率提升40%以上。
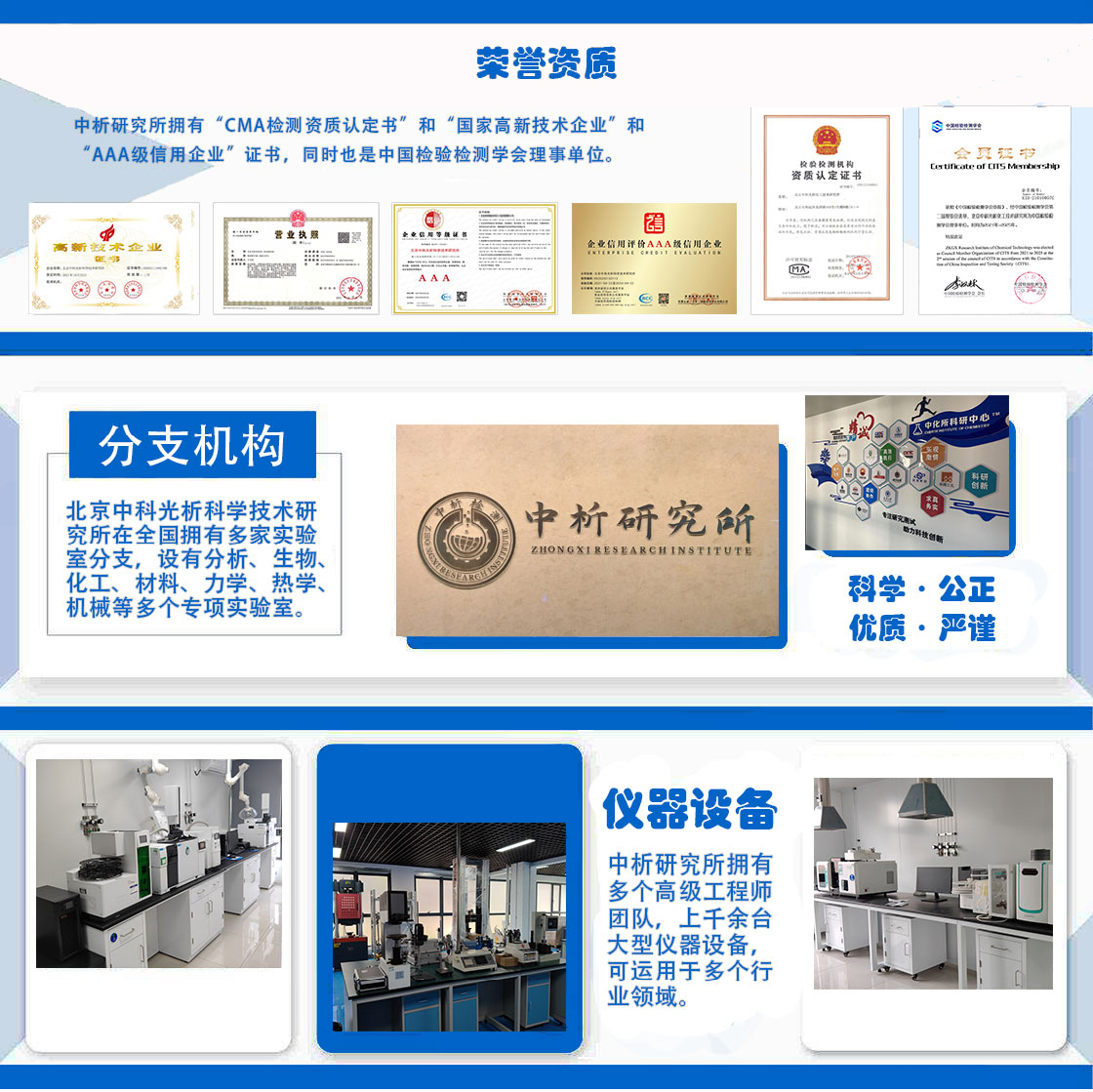
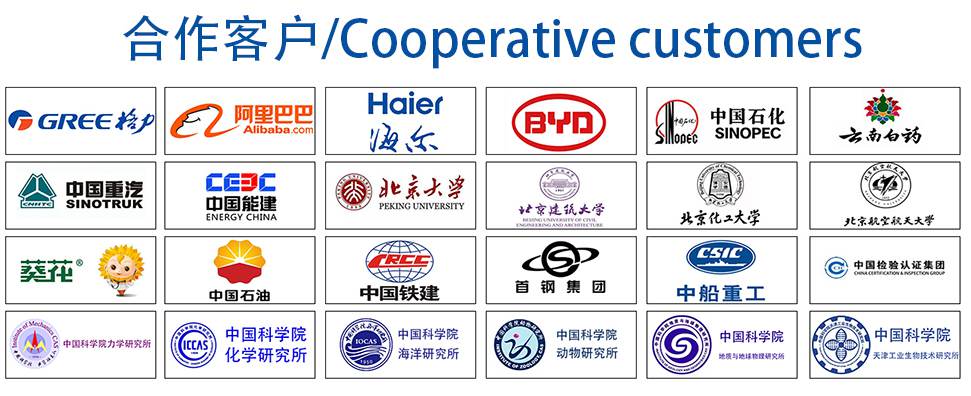