陶瓷砖自动液压机检测项目解析
作为现代建筑陶瓷生产线的核心设备,自动液压机的性能直接决定了陶瓷砖的成型质量与生产效率。其检测工作需从机械性能、控制系统到成品参数进行全方位验证,以确保设备在高压压制、精准定位和快速循环等复杂工况下的稳定性。通过系统化的检测流程,可有效规避因设备异常导致的成品开裂、尺寸偏差或能耗过高等问题,同时延长关键部件的使用寿命。
一、基本性能检测
1. 压力精度测试:采用高精度传感器监测主缸压力输出,要求最大工作压力误差≤±2%,保压阶段压力波动控制在设定值的±1.5%内
2. 动作同步性验证:通过位移传感器检测各油缸动作时序,模具闭合阶段同步误差需<0.1mm,开模行程重复精度应达到±0.05mm
3. 循环周期稳定性:连续运行200次压制循环,统计周期时间标准差需≤0.3秒,验证液压系统和PLC控制的响应速度
二、安全防护系统检测
1. 急停装置测试:模拟突发状况触发急停按钮,验证制动装置应在0.2秒内完成停机,模具上升高度须立即锁定
2. 安全光栅功能验证:采用标准测试块遮挡光幕,设备需在10ms内停止动作并发出声光报警
3. 电气防护检测:测量设备各接地端电阻值,要求≤0.1Ω,绝缘电阻测试需≥10MΩ/500V
三、工艺参数验证
1. 温度场标定:在连续工作状态下,使用红外热像仪监测模具温度分布,温差应控制在±5℃以内
2. 压制速度测试:采用激光测速仪检测压制阶段速度曲线,要求快下段速度误差≤3%,工进段速度波动≤1.5%
3. 模具平行度校正:使用千分表测量上下模具四角间隙,平面度误差需≤0.02mm/m²
四、成品质量关联检测
1. 砖坯尺寸检测:通过三坐标测量仪抽检压制砖坯,长度/宽度公差应≤±0.3mm,厚度波动≤±0.15mm
2. 密度均匀性测试:采用γ射线密度仪扫描砖坯断面,密度差异需<5%
3. 表面缺陷分析:借助工业相机进行视觉检测,裂纹检出精度达到0.1mm,边角缺损识别率≥99%
五、检测周期建议
根据GB/T 3810.4-2016标准,常规检测应每500小时进行1次全面校验,关键压力传感器需每200小时进行零点校准。新设备安装后需进行72小时连续跑合试验,并在首3000次冲压周期内实施加密检测(每8小时记录运行数据)。
通过上述系统化的检测方案,可确保自动液压机保持98%以上的有效运行率,同时将陶瓷砖优等品率提升至95%以上。建议企业建立检测数据库,结合机器学习算法实现预测性维护,进一步降低设备故障风险。
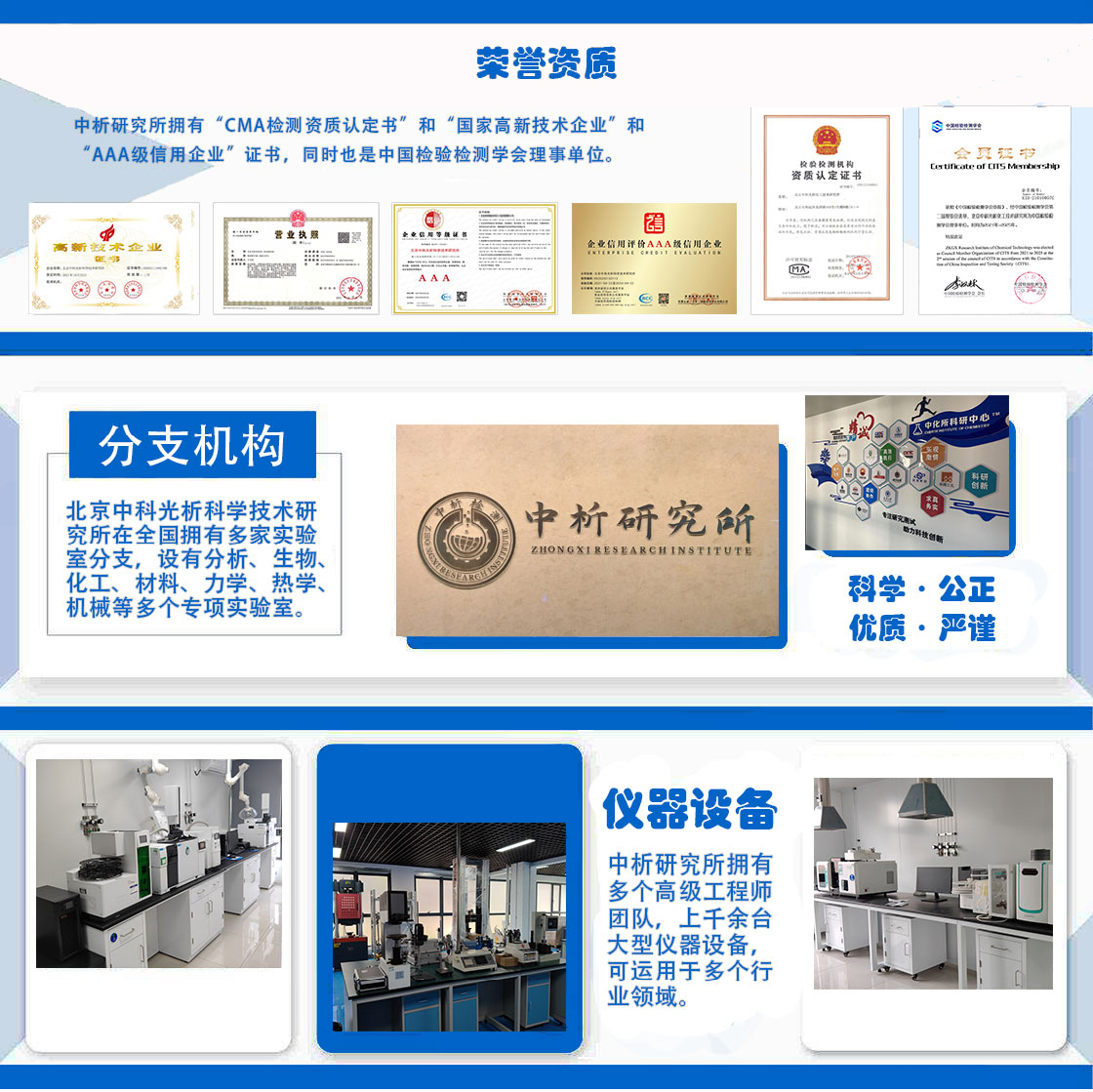
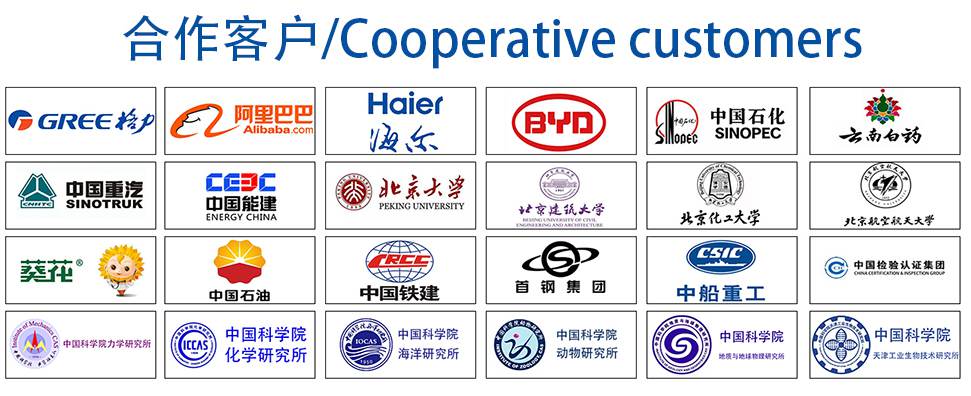