水泥工业用预热器分解炉系统装备技术条件检测的重要性
在水泥生产过程中,预热器分解炉系统是新型干法水泥生产线的核心装备之一,承担着原料预分解、热量回收和降低能耗的关键作用。其运行状态直接影响熟料质量、能源利用率及生产稳定性。因此,定期对预热器分解炉系统装备的技术条件进行检测,是保障生产线高效运行、延长设备寿命的重要措施。通过科学的检测手段,能够及时发现设备隐患、优化工艺参数,并为维护决策提供数据支持。
主要检测项目及技术要求
1. 系统结构完整性检测
重点检查预热器分解炉的筒体、内衬、连接管道及支撑结构的完整性。通过目视检查、超声波测厚仪和激光扫描技术,评估是否存在变形、裂纹或腐蚀现象。筒体厚度偏差需控制在设计值的±5%以内,焊接部位需满足《水泥工业设备安装验收规范》的要求。
2. 热效率与温度分布检测
利用红外热成像仪和热电偶对系统各部位温度进行实时监测,分析热分布均匀性及热量损失情况。分解炉出口气体温度应稳定在850~900℃,预热器各级温差需符合工艺设计要求。热效率检测数据用于优化燃料配比和通风系统参数。
3. 耐火材料状态评估
定期检测分解炉内耐火材料的磨损、剥落及结皮情况。采用内窥镜观察结合抗压强度测试,确保耐火材料厚度不低于设计值的80%。同时需关注材料的抗热震性能,避免因温度波动导致结构失效。
4. 气体流动与压力平衡检测
通过差压传感器和风速仪测量系统内气流速度、压力分布及阻力参数。预热器各级压力梯度需保持合理范围(一般级间压差为500~800Pa),防止气流短路或堵塞。检测数据可用于调整风机频率或优化旋风筒结构。
5. 密封性能与漏风率测试
系统漏风是导致能耗增加的主要原因之一。采用气体示踪法或氧含量分析法检测系统漏风率,要求预热器分解炉系统整体漏风率≤5%。重点关注法兰连接处、检修门及膨胀节的密封状态。
6. 自动化控制系统校验
对温度、压力、流量等传感器的校准精度进行检测,确保误差范围≤1.5%。同时验证DCS系统与执行机构的联动响应速度,如喂料阀门开闭时间误差需≤0.5秒,以保障工艺控制的稳定性。
检测周期与后续管理
根据设备运行时长和工况条件,建议每6个月进行一次全面检测,关键部位(如耐火内衬)需缩短至3个月。检测结果应形成数字化报告,结合历史数据建立设备健康档案。对于发现的局部缺陷,需制定分级维修方案;若检测指标连续超标,则需启动系统停机大修程序。
通过系统化、标准化的技术条件检测,水泥企业可显著降低非计划停机风险,提升熟料线运转率至90%以上,同时实现吨熟料煤耗降低3%~5%的节能目标。未来,随着智能传感和AI诊断技术的应用,检测的实时性和精准性将进一步提升。
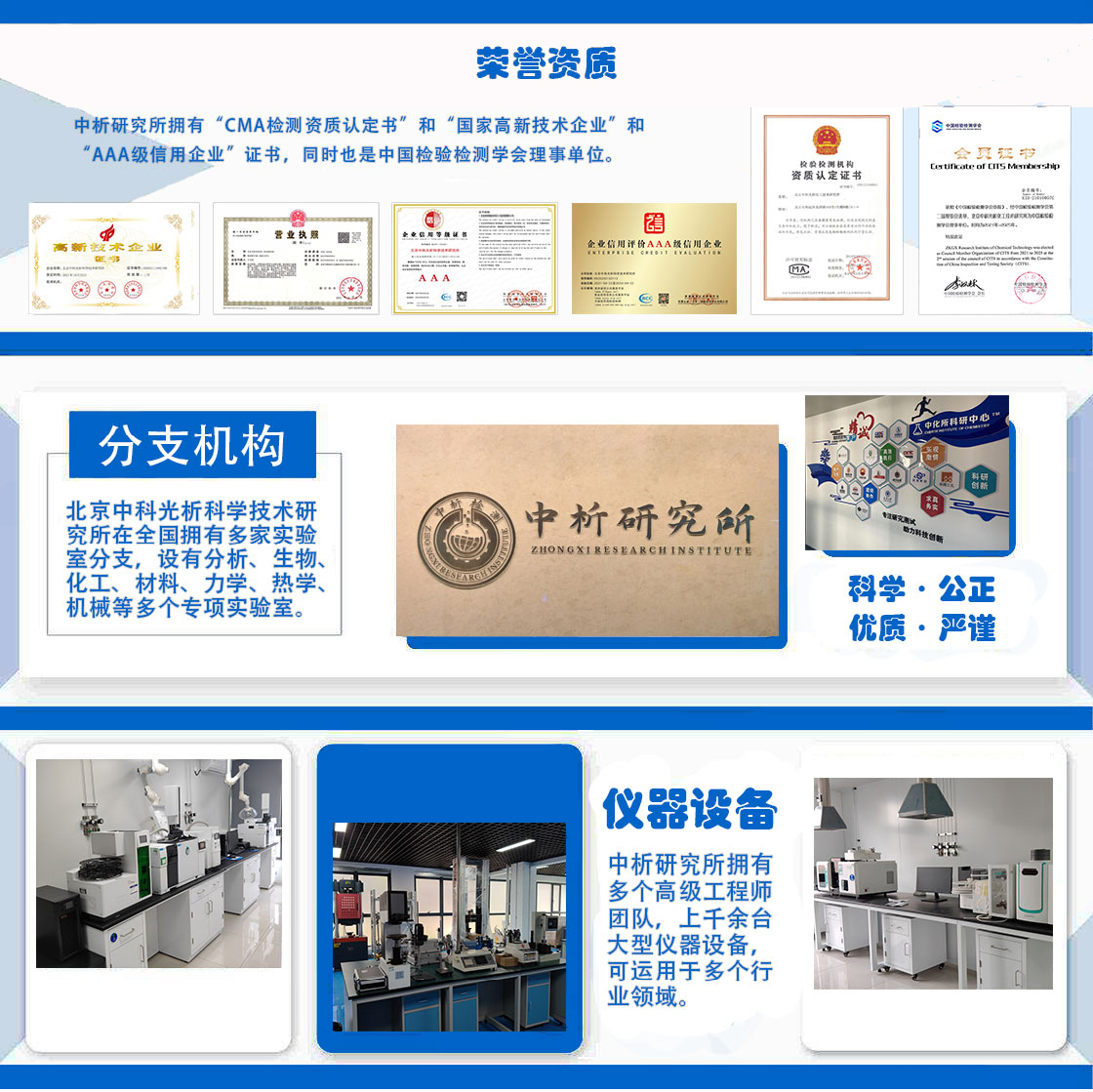
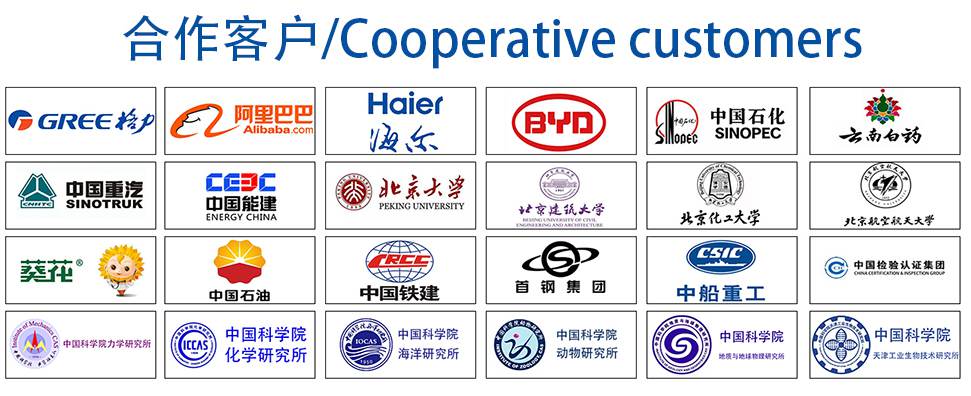