卡车、公交车及类似车辆用车轮和轮辋检测的重要性
在重型车辆领域,车轮和轮辋作为承载车辆重量、传递动力的核心部件,其安全性与可靠性直接关系到车辆行驶安全、运营效率及使用寿命。由于卡车、公交车等车辆长期处于高负载、复杂路况及频繁启停的工作环境中,车轮和轮辋的疲劳损伤、形变、裂纹等问题可能引发严重事故。因此,针对这些部件的系统性检测成为车辆制造、维护及安全监管中不可或缺的环节。通过科学的检测手段,可提前识别潜在缺陷,确保其符合国家标准和行业规范,从而降低事故风险、延长部件寿命并提升车辆整体性能。
关键检测项目解析
1. 材料性能检测
车轮和轮辋的材质直接影响其强度和耐久性。检测内容包括:
- 化学成分分析:通过光谱仪等设备验证铝合金、钢等材料中元素含量是否符合标准(如GB/T 8733);
- 力学性能测试:检测抗拉强度、屈服强度、延伸率等指标;
- 金相组织分析:观察材料内部结构是否存在气孔、夹渣等缺陷。
2. 尺寸精度与形位公差检测
采用三坐标测量仪、激光扫描仪等设备对以下参数进行精确测量:
- 轮辋直径、宽度、偏距(ET值)偏差;
- 螺栓孔分布圆(PCD)精度;
- 轮缘高度、法兰平面度等形位公差(依据ISO 3911标准)。
3. 动态平衡性测试
通过动平衡机模拟高速旋转工况(最高达120km/h等效转速),检测车轮质量分布均匀性。允许不平衡量通常需≤40g·cm(按ISO 19453标准),超标会导致车辆振动加剧,影响悬架系统和驾驶安全性。
4. 疲劳寿命与抗冲击试验
在专用台架上进行径向疲劳试验(模拟载重)和弯曲疲劳试验(模拟转向受力),循环次数需满足ECE R124等法规要求。例如:
- 径向疲劳:加载1.5倍额定载荷,完成50万次循环无失效;
- 抗冲击测试:以590J能量冲击轮缘,检查是否产生裂纹或永久变形。
5. 表面质量与防腐性能评估
包括涂层厚度(如电泳漆膜≥20μm)、附着力(划格法测试)、盐雾试验(NSS测试≥720小时无红锈)等。对镀锌轮辋还需检测锌层均匀性,避免局部腐蚀导致结构强度下降。
6. 安装匹配性验证
通过扭矩测试验证轮毂螺栓连接可靠性(推荐扭矩误差≤±5%),同时检查轮胎装配后的气密性及胎圈接触区域压力分布,防止运行中发生漏气或脱圈风险。
7. 环境适应性测试
模拟极端环境条件,如:
- 高温(+60℃)与低温(-40℃)下尺寸稳定性;
- 湿热循环(85%湿度)对材料性能的影响;
- 碎石冲击测试评估表面防护层耐久性。
检测技术发展趋势
随着技术进步,工业CT无损探伤、数字孪生仿真预测等新兴技术正逐步应用于车轮检测领域。例如通过X射线断层扫描可三维重建内部缺陷,而基于大数据的疲劳寿命预测模型可将检测效率提升30%以上。这些创新手段为保障重型车辆的安全运营提供了更强有力的技术支撑。
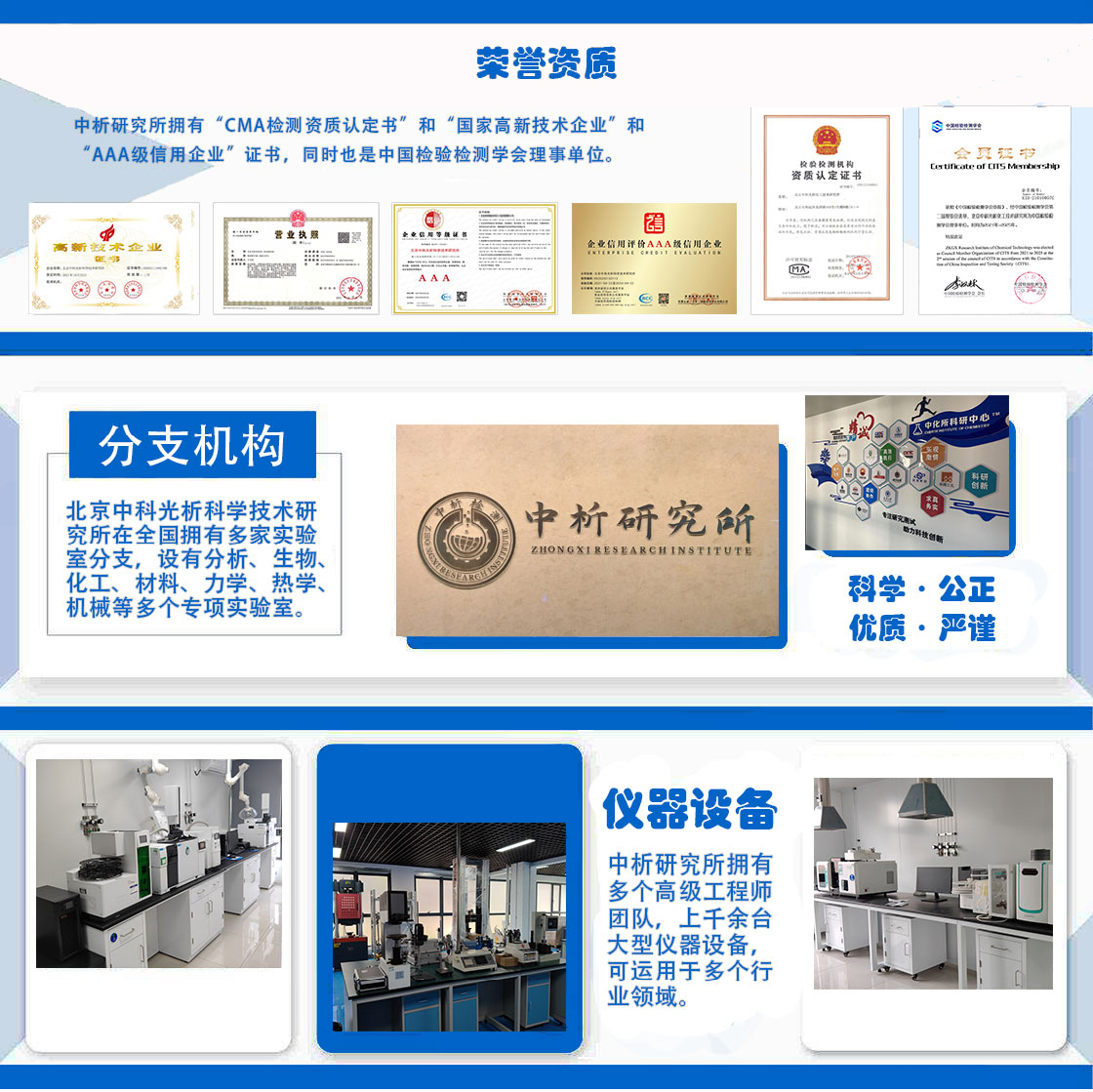
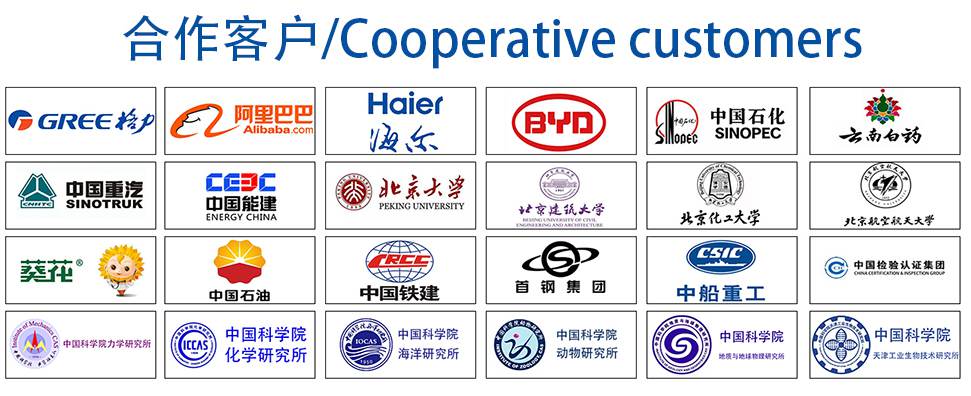