制动摩擦材料检测的重要性与应用领域
制动摩擦材料是汽车、轨道交通、工程机械等领域的核心安全组件,其性能直接关系到制动系统的可靠性与使用寿命。随着现代交通工具对安全性、环保性要求的提高,制动摩擦材料的检测技术已成为保障产品质量、优化生产工艺的重要手段。这类材料通常由金属、非金属及复合材料组成,需在高负荷、高温、高磨损等极端工况下保持稳定的摩擦系数与耐久性。因此,通过科学系统的检测项目评估其综合性能,不仅是行业法规的刚性要求,更是企业提升市场竞争力的关键环节。
关键检测项目与技术标准
在制动摩擦材料的检测体系中,主要包含以下核心项目:
1. 摩擦系数测试
通过定速式摩擦试验机或惯性台架试验,模拟不同温度(常温至600℃)、压力及速度条件下的摩擦系数变化。需符合GB 5763-2018《汽车用制动器衬片》标准,确保材料在冷态、热态及衰退恢复阶段的稳定性,避免制动效能热衰退导致的失效风险。
2. 磨损率分析
采用质量损失法或体积磨损法测定材料在特定工况下的磨损量,结合扫描电镜(SEM)观察磨损表面形貌,评估材料的抗磨性能。高磨损率会导致制动系统间隙异常增大,直接影响制动响应速度。
3. 热衰退性能评价
通过连续制动试验检测材料在高温循环下的摩擦系数衰减程度,模拟车辆连续下坡等极端场景。检测需记录衰退率及恢复特性,确保材料在高温下仍能保持至少70%的初始摩擦系数。
4. 剪切强度与抗冲击性测试
采用万能试验机测定材料与背板的粘接强度,评估其在震动、冲击载荷下的结构完整性。剪切强度不足易引发衬片分层脱落,造成制动失灵事故。
5. 环保性能检测
依据欧盟REACH法规及GB/T 30512标准,检测材料中石棉、重金属(铅、镉、铬)、多环芳烃(PAHs)等有害物质的含量,满足绿色制造要求。
6. NVH特性试验
通过噪声振动测试系统(NVH)分析制动过程中的异响与抖动现象,优化材料配方以降低高频噪声,提升驾乘舒适性。
检测技术发展趋势与挑战
当前,随着电动汽车对能量回收制动系统的需求增加,检测项目正向着多物理场耦合测试(热-力-电)方向发展。同时,人工智能技术的引入使磨损预测、材料寿命评估更加精准。然而,如何建立统一的标准体系、实现复杂工况下的动态模拟仍是行业亟需突破的技术难点。
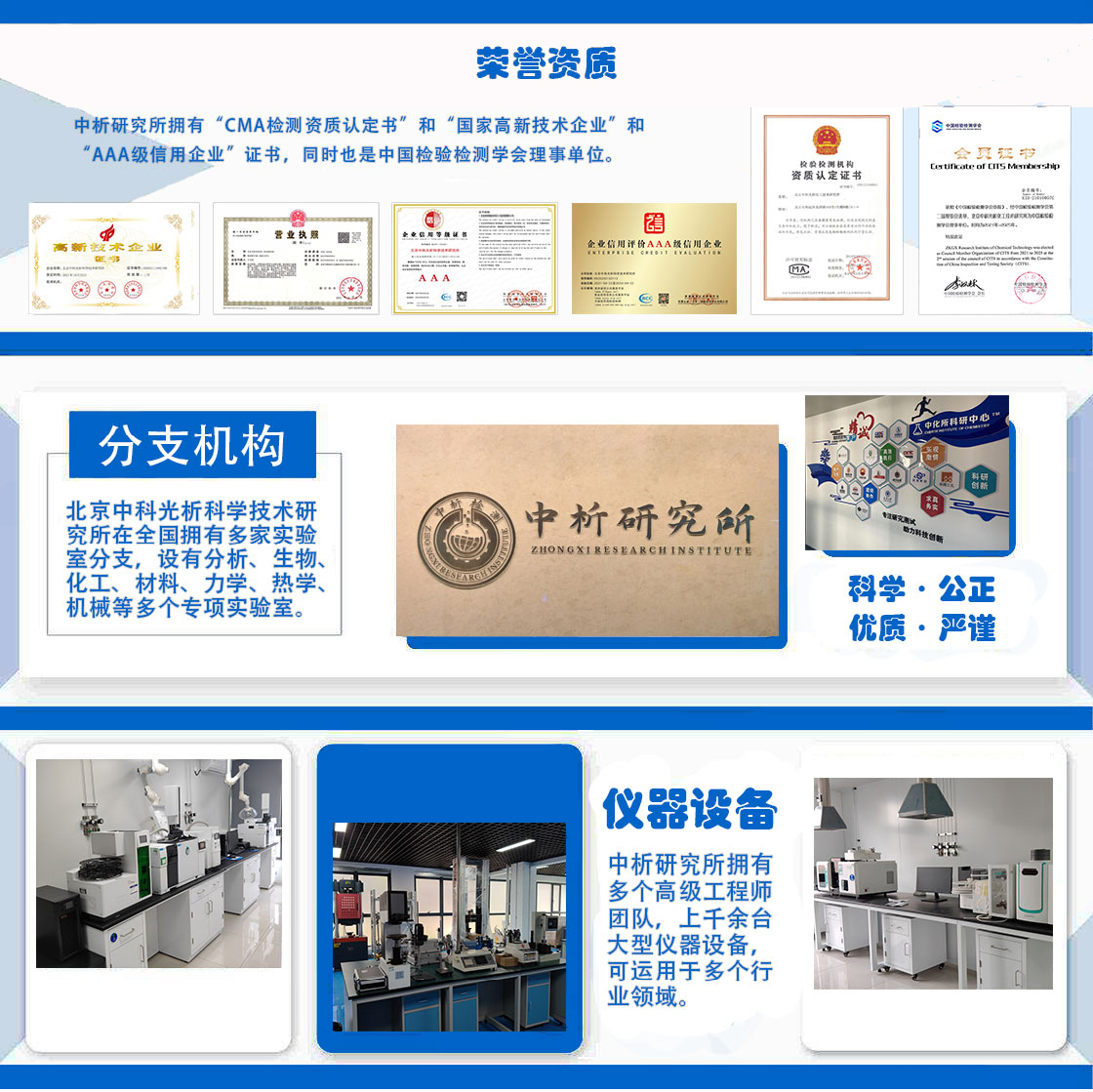
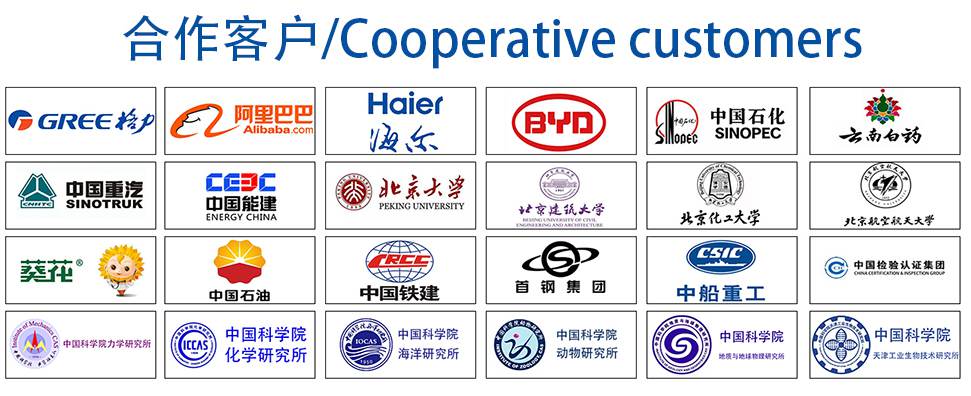