城市轨道交通车辆制动系统检测的意义与要求
城市轨道交通作为现代都市出行的核心载体,其安全性直接关系到乘客生命财产与城市运行效率。制动系统作为车辆安全控制的关键子系统,承担着减速、停车及紧急制动等重要功能。由于车辆频繁启停、高载荷运行以及复杂环境的影响,制动系统易出现磨损、老化、性能衰减等问题。因此,定期开展系统化、标准化的检测项目,是保障列车运行安全、延长设备寿命、降低运维成本的必要手段。检测需覆盖机械、电气、气动(或液压)等多个维度,并遵循国家及行业标准(如《城市轨道交通车辆制动系统技术规范》),确保检测结果的科学性与可靠性。
核心检测项目及内容
1. 制动性能测试
通过动态试验台或实际线路测试,评估制动系统的响应时间、制动力分配均匀性及制动减速度。需模拟不同载荷(空载/满载)、不同速度(最高运行速度至低速)下的制动效果,验证是否符合紧急制动距离(如80km/h时速下≤190米)与常规制动的设计要求。
2. 摩擦材料检测
针对制动盘、闸片等摩擦副,检查磨损量、表面裂纹及热衰退特性。采用三维轮廓仪测量材料厚度,并通过高温摩擦试验(如300℃以上环境)评估摩擦系数稳定性,确保制动效率不受极端工况影响。
3. 气动/液压管路密封性检测
使用压力传感器和泄漏检测仪,对制动管路、阀门及执行机构进行气密性试验。要求系统在额定压力(如常用8-10Bar气动压力)下保压30分钟无泄漏,同时验证电磁阀动作响应时间≤0.1秒,避免因压力损失导致制动力不足。
4. 电控系统功能性验证
通过故障注入测试,检验制动控制单元(BCU)的信号处理能力与故障诊断精度。包括速度传感器信号异常、通信中断等场景下的冗余控制策略,确保系统能自动切换至备份模式并触发安全制动。
5. 防滑保护系统测试
在模拟湿滑轨道条件下,激活轮对滑行保护功能。检测滑行率超过阈值时系统能否动态调整制动力,避免车轮抱死导致轨道擦伤或制动距离异常延长,并通过加速度传感器记录轮轨接触状态。
6. 机械部件疲劳强度分析
对制动夹钳、连杆机构等关键部件进行疲劳寿命测试,利用有限元仿真与实物循环加载试验(如10^6次以上动作测试),评估其抗疲劳性能,预防因金属疲劳引发的结构性失效风险。
检测技术创新与发展趋势
随着智能运维技术的普及,车载实时监测(如安装振动传感器与温度传感器)与大数据分析逐步成为检测体系的重要组成部分。通过采集制动过程中的多维度数据,结合AI算法预测部件剩余寿命,实现从“定期检修”向“状态修”的转型,进一步提升检测效率与精准度。
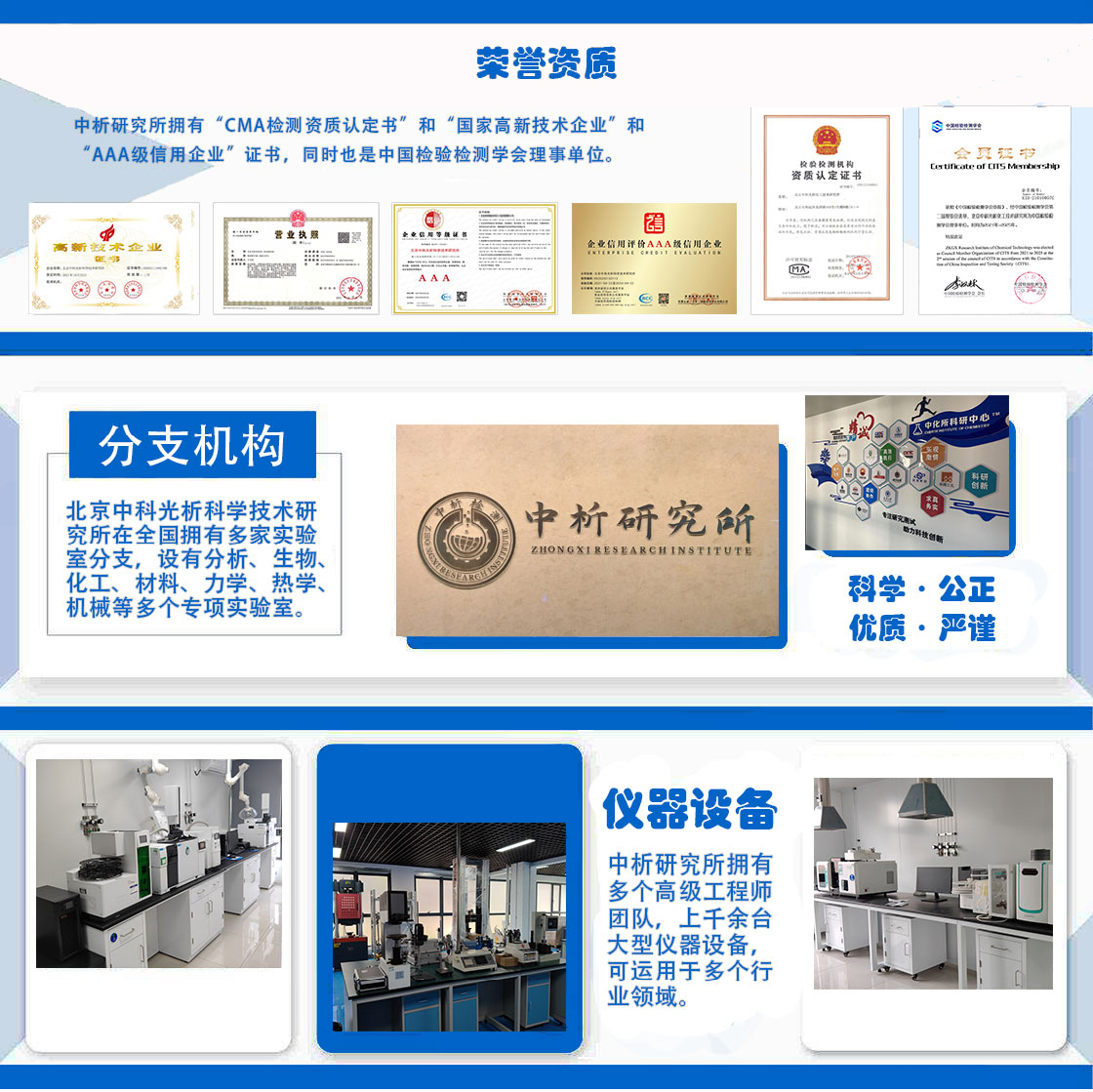
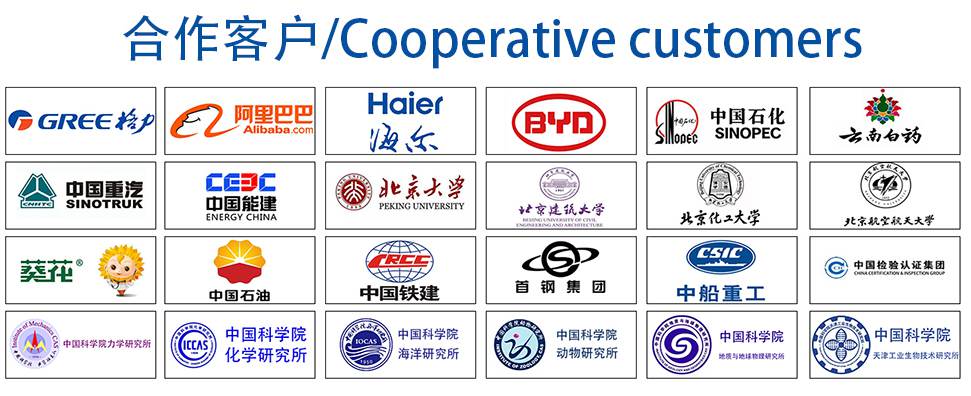