热采井口装置检测的重要性与核心内容
热采井口装置作为稠油热力开采过程中的关键设备,承担着控制井口压力、保障注汽安全和防止介质泄漏的核心功能。其长期在高温(300℃以上)、高压(20MPa以上)及腐蚀性介质环境中运行,易出现材料老化、密封失效、结构变形等问题。因此,定期开展系统化检测是确保油气田安全生产、延长设备使用寿命的核心措施。根据行业规范(如SY/T 5323、API 6A等),检测需覆盖装置完整性、耐温耐压性能、密封可靠性等关键指标,并通过多维度数据分析实现风险预判。
核心检测项目与技术要点
1. 耐压性能测试
采用液压/气压试验法,按额定压力的1.5倍进行分级保压测试,监测承压部件(套管头、油管头、主阀)的形变量与渗漏情况。需特别注意高温循环后的残余应力变化,结合应变片数据评估材料抗蠕变能力。
2. 密封系统检测
运用氦质谱检漏仪对法兰连接处、阀门填料函等关键密封点进行定量检测,泄漏率需≤1×10⁻⁶Pa·m³/s。针对金属-石墨缠绕垫片等高温密封件,需进行热态密封试验,模拟实际工况下的热膨胀匹配性。
3. 材料性能评估
通过金相分析、硬度测试(布氏/洛氏)及夏比冲击试验,判断主体材料(如25CrMo、Inconel合金)在长期高温下的组织稳定性。重点检测热影响区是否存在σ相析出、晶间腐蚀等缺陷。
4. 阀门功能性验证
针对注汽主阀、安全阀进行动作响应测试,包括开启/关闭时间、复位精度及高温卡阻现象分析。采用红外热成像技术监测阀杆与阀座的温度分布均匀性,排查局部过热风险。
5. 腐蚀与冲蚀监测
使用超声波测厚仪对装置内壁进行网格化壁厚测量,结合涡流检测定位点蚀缺陷。对于蒸汽注入管段,需通过高速摄像记录两相流冲蚀形态,评估弯头部位的冲蚀速率。
检测周期与风险防控
常规检测周期为12个月,但高温蒸汽吞吐井需缩短至6个月。检测数据应建立全生命周期数据库,通过趋势分析预测密封圈老化、螺栓预紧力衰减等潜在故障。对于检测中发现的法兰平面度超差(>0.05mm/m)等缺陷,需采用激光熔覆或冷喷涂工艺进行再制造修复。
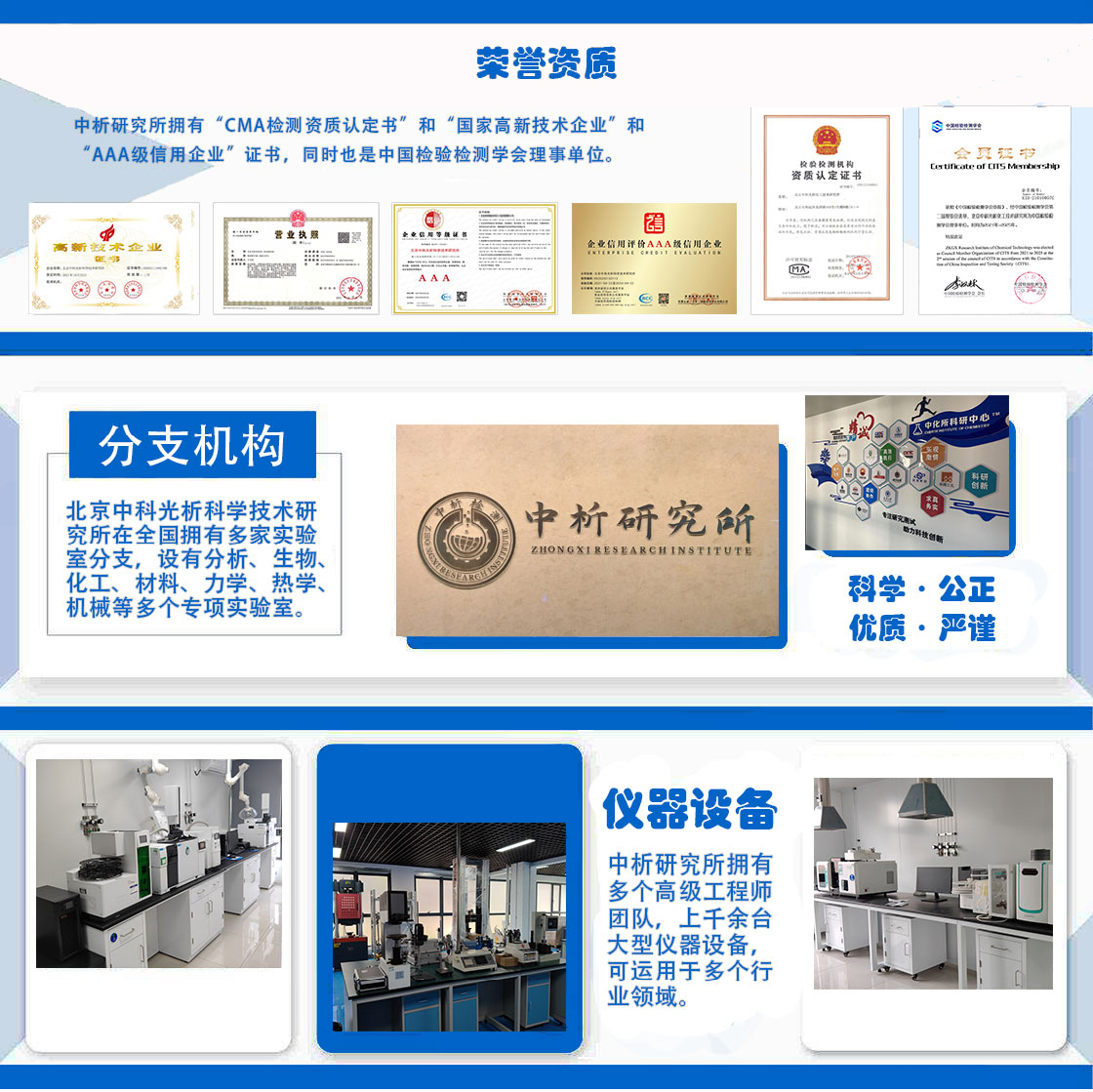
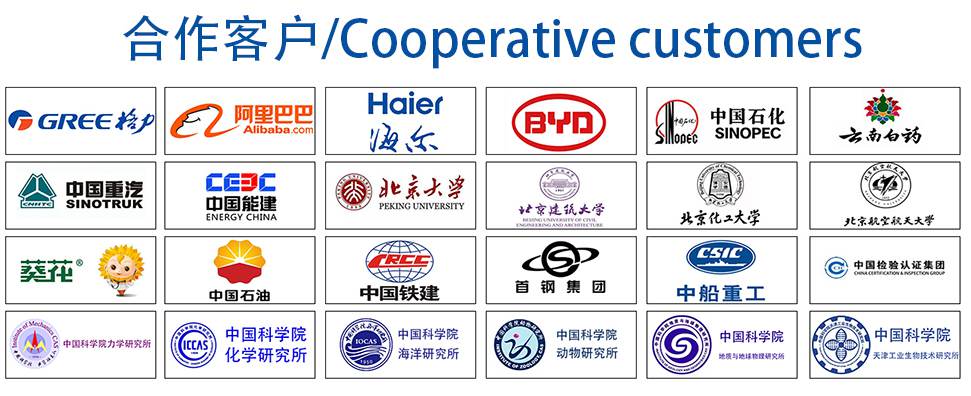