机车车辆电气设备-电工器件-交流断路器检测的重要性
交流断路器作为机车车辆电气系统的核心保护装置,承担着过载、短路故障时的快速分断电流功能,其性能直接影响机车运行安全与供电可靠性。随着现代铁路运输对高速度、大功率需求的提升,交流断路器的检测已成为机车维护和检修中的关键环节。通过系统化检测,可确保断路器在高压、振动、温变等复杂工况下的动作精度、绝缘性能及机械寿命满足标准,从而保障机车牵引系统、辅助电路及控制回路的稳定运行。
交流断路器检测的核心项目
1. 外观与结构完整性检测
首先需进行目视检查,确认断路器外壳无变形、裂纹或锈蚀,灭弧室、触头系统等关键部件无烧损痕迹。重点检查接线端子紧固状态,确保无松动或氧化现象。同时验证操作机构(如弹簧储能机构)的运动灵活性及标识清晰度,确保分合闸指示与实际状态一致。
2. 机械性能测试
通过专用试验台模拟断路器分合闸操作,检测其机械特性参数:
- 分闸时间与合闸时间:需符合设计值(通常≤60ms)
- 同期性偏差:三相触头动作时间差不超过2ms
- 机械寿命试验:连续完成额定操作次数(如5000次)后,机构无卡滞、零件磨损量在允许范围内
3. 电气性能检测
包含以下关键测试项:
绝缘电阻测试:使用2500V兆欧表测量主回路对地及相间绝缘电阻,要求≥100MΩ(常温干燥条件下)
工频耐压试验:施加额定电压1.5倍的交流电压(如42kV/1min),无闪络或击穿现象
温升试验:在1.1倍额定电流下持续运行至稳定,触头温升不超过标准限值(通常≤65K)
4. 分断能力验证
通过大电流试验装置模拟短路条件,测试断路器在额定短路开断电流(如25kA)下的表现:
- 燃弧时间与全分断时间是否符合设计要求
- 分断后触头烧蚀情况评估
- 重击穿率检测(需≤3次/100次操作)
5. 环境适应性检测
针对机车特殊工况开展:
- 振动试验:模拟列车运行时的轴向振动(频率5-150Hz,加速度3g)
- 湿热循环试验:验证在高湿度(95%RH)及温度交变(-40℃~+70℃)下的绝缘性能
- 盐雾试验:评估沿海线路环境下金属部件的耐腐蚀能力
检测标准与设备要求
检测过程需严格遵循TB/T 2764《机车车辆用断路器技术条件》、IEC 62271系列标准。主要设备包括:
- 断路器特性测试仪(如TIM系列)
- 高压绝缘测试系统
- 瞬态记录仪(用于捕捉分断过程的电流/电压波形)
- 环境试验箱与振动台
检测结果分析与处理
对测试数据进行横向对比与趋势分析,重点关注:
- 分闸速度下降是否超过初始值的20%
- 接触电阻的增量是否高于标准阈值
- 绝缘材料的老化迹象判断
发现异常时需进行解体检查,及时更换磨损的触头弹簧、清理灭弧室积碳,并对灭弧介质(如SF6气体)进行纯度检测和补充。
结语
系统化的交流断路器检测不仅是预防机车电气故障的重要手段,更是实现状态修、预测性维护的基础。通过建立完整的检测数据库与寿命预测模型,可显著提升检修效率,降低因断路器失效导致的运营风险,为现代轨道交通的安全高效运行提供坚实保障。
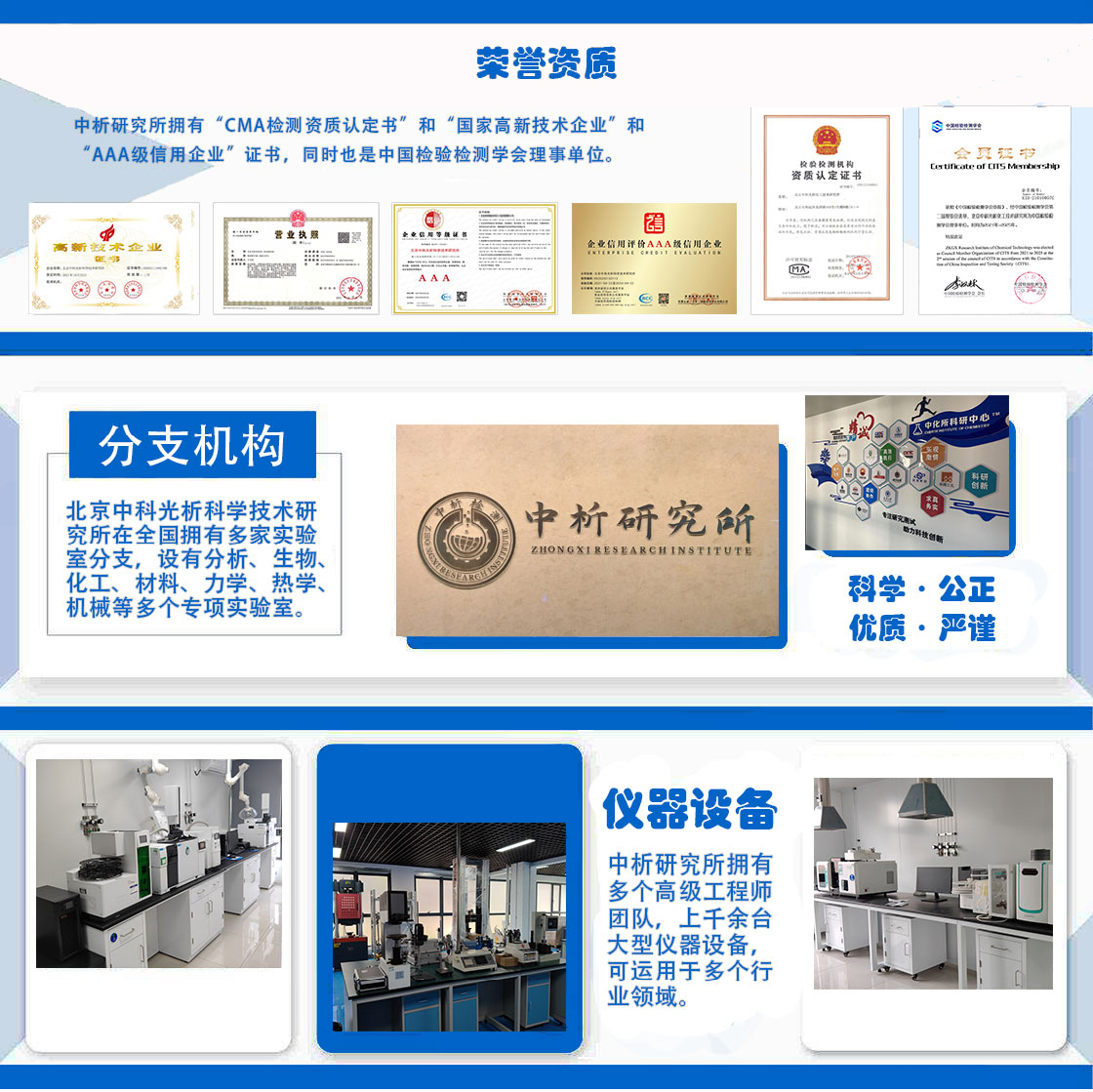
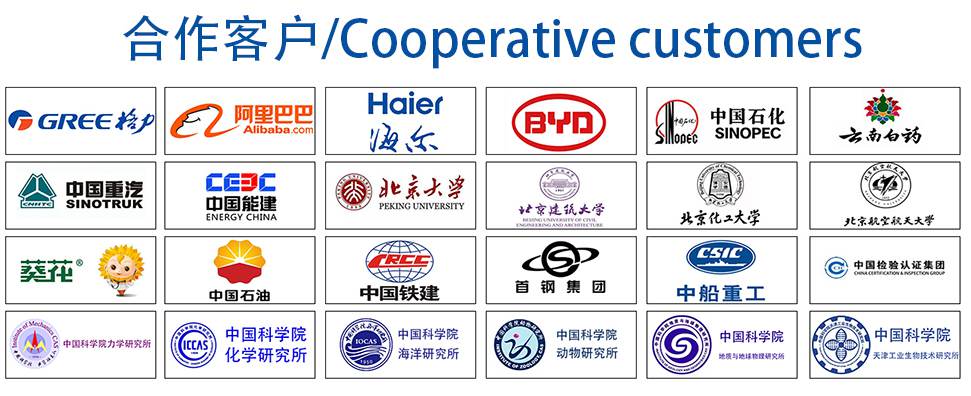