耐火泥浆检测技术规范与应用要点解析
耐火泥浆作为高温工业设备砌筑的核心材料,其性能直接关系到窑炉、锅炉等设备的使用寿命与安全运行。该材料由耐火骨料、结合剂及添加剂组成,在冶金、电力、建材等行业广泛应用。其检测工作贯穿原材料筛选、生产质量控制和施工验收全过程,通过系统化的检测项目可有效评估材料的耐火度、粘结强度、热稳定性等关键指标,为工程质量的可靠性提供科学依据。
核心检测项目体系
1. 化学成分分析:采用X射线荧光光谱仪测定Al₂O₃、SiO₂、Fe₂O₃等主成分含量,同时检测Na₂O+K₂O等熔剂物质比例,确保符合GB/T 14982-2020标准要求。
2. 耐火度测试:通过高温锥形量热法在标准升温条件下测定材料软化温度,常规产品耐火度需达到1580-1770℃区间,满足不同工况需求。
3. 常温抗压强度:依据YB/T 5201规范制备标准试样,使用万能试验机检测养护后的抗压强度值,重要工程要求≥10MPa。
4. 高温粘结强度:模拟实际工况,在800-1200℃下测试泥浆与耐火砖的粘结性能,确保高温环境下的结构稳定性。
5. 热震稳定性:将试样经历30次1100℃⇄水冷的急冷急热循环,计算强度保持率,优异产品残余强度应>70%。
扩展检测指标
体积密度与显气孔率检测采用阿基米德法,控制范围2.0-2.5g/cm³;粒度分布使用激光衍射仪分析,确保施工和易性;线膨胀系数测定匹配耐火砖的热膨胀特性;施工性能评估涵盖稠度、保水率等现场作业参数。
检测流程标准化
完整检测流程包含代表性取样(GB/T 17617)、实验室预处理、分项检测、数据比对、出具 认证报告等环节。重点管控试样养护环境(温度20±2℃,湿度≥90%)和检测设备校准,确保结果准确性。
质量控制关键点
检测过程需特别注意:原料批次差异带来的检测波动、不同施工工艺对检测标准的适配性、国际标准(ASTM C862、ISO 1927)与国标的对照应用。建议生产企业建立原料-半成品-成品的三级检测体系,工程项目实施进场复检与施工过程抽检相结合的双重管控。
通过完善的检测体系实施,可有效降低耐火构筑物开裂、剥落等质量风险,据行业统计数据显示,系统化检测可使工业窑炉使用寿命平均延长30%以上,具有显著的经济效益与安全保障价值。
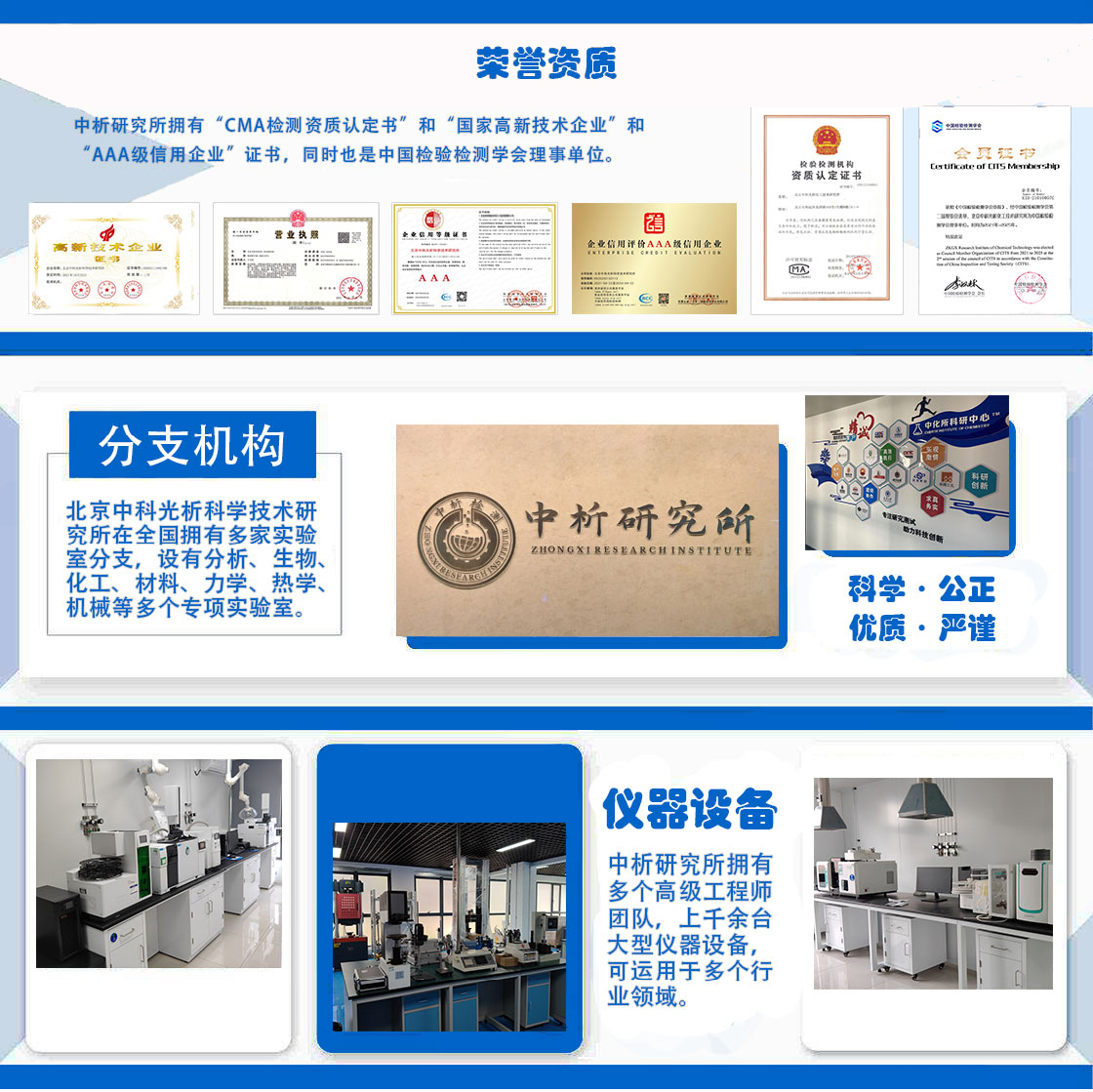
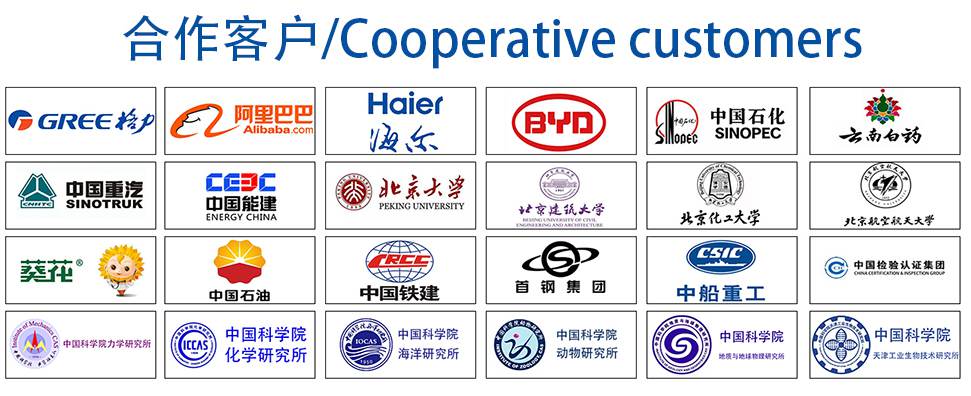