公路交通工程钢构件防腐检测的重要性
公路交通工程中的钢构件(如桥梁、护栏、立柱、支撑架等)长期暴露在复杂的环境条件下,面临雨水、盐雾、紫外线、温差变化及空气污染物等多重腐蚀威胁。防腐性能的优劣直接关系到钢构件的使用寿命、结构安全性和维护成本。若防腐措施失效,不仅会导致钢材强度下降,还可能引发安全隐患,甚至造成重大交通事故。因此,通过科学的防腐检测手段评估钢构件的涂层质量及材料耐久性,是确保公路设施长期稳定运行的核心环节。
防腐检测的主要项目及方法
1. 涂层厚度检测
涂层厚度是衡量防腐效果的基础指标。检测时需使用磁性测厚仪或涡流测厚仪,依据国家标准(如GB/T 4956)对钢构件表面的涂层进行多点测量,确保厚度均匀且符合设计要求。若涂层过薄,可能导致局部腐蚀加速;过厚则可能影响附着力或引发开裂。
2. 涂层附着力测试
附着力决定了涂层与基材的结合强度。常用方法包括划格法(GB/T 9286)和拉开法(GB/T 5210)。划格法通过切割涂层网格观察脱落情况,快速评估附着力等级;拉开法则通过施加垂直拉力精确测量破坏强度。检测需覆盖不同区域,尤其关注焊缝和边缘等易失效部位。
3. 耐盐雾腐蚀性能检测
盐雾试验(GB/T 10125)模拟沿海或融雪剂环境下的腐蚀情况。将试样置于盐雾箱中,按设定周期(如500小时、1000小时)观察涂层起泡、剥落或基材锈蚀程度。该测试能有效验证涂层的长期防护能力,并为材料选型提供依据。
4. 环境适应性测试
包括耐湿热循环(GB/T 1740)、耐紫外线老化(GB/T 23987)等专项检测。湿热试验通过高温高湿环境加速涂层老化,评估其在潮湿气候下的稳定性;紫外线老化测试则模拟日光辐照,分析涂层的耐候性和颜色保持能力。
5. 焊缝及隐蔽部位检测
钢构件的焊缝、连接螺栓及内部腔体是防腐薄弱环节。需采用内窥镜、磁粉探伤(MT)或渗透探伤(PT)技术检查是否存在未封闭气孔、裂纹或涂层漏涂问题,避免因工艺缺陷导致局部腐蚀扩散。
防腐检测的关键标准与验收要求
公路钢构件的防腐检测需遵循JT/T 722《公路桥梁钢结构防腐涂装技术条件》、GB/T 30790《防护涂料体系对钢结构的防腐蚀保护》等行业标准。验收时需综合涂层外观(无流挂、针孔等缺陷)、厚度偏差(≤±10%)、附着力(≥5MPa)及耐腐蚀试验结果,确保防腐体系满足设计寿命(通常≥15年)。
结语
钢构件防腐检测是公路工程质量管理的重要环节,需结合材料特性、环境条件及施工工艺,建立全周期检测机制。通过科学的检测技术与严格的标准执行,可有效延长设施服役周期,降低运维成本,为公路交通安全提供可靠保障。未来,随着智能传感与无损检测技术的发展,防腐状态的实时监测与预警将成为行业新趋势。
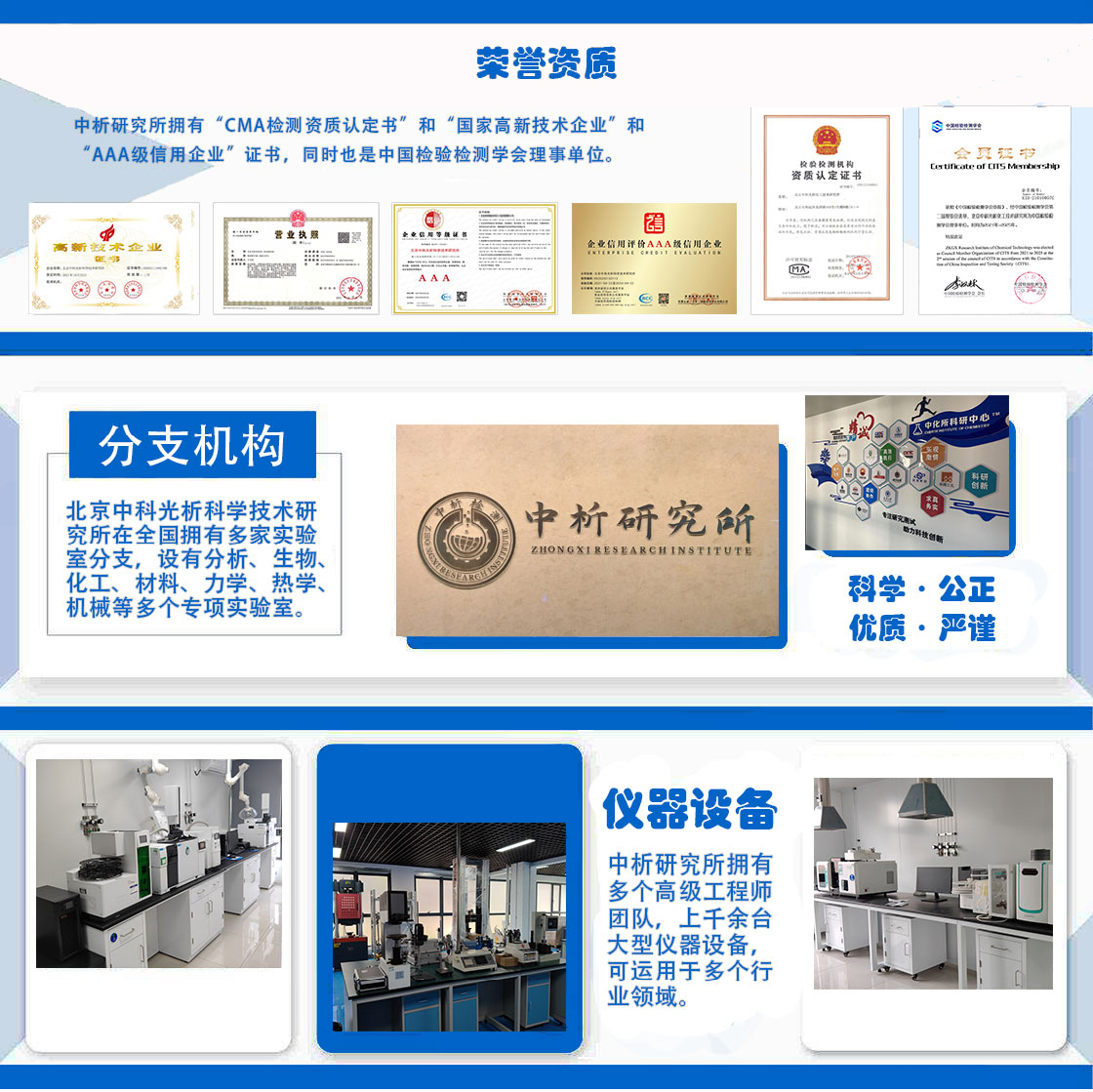
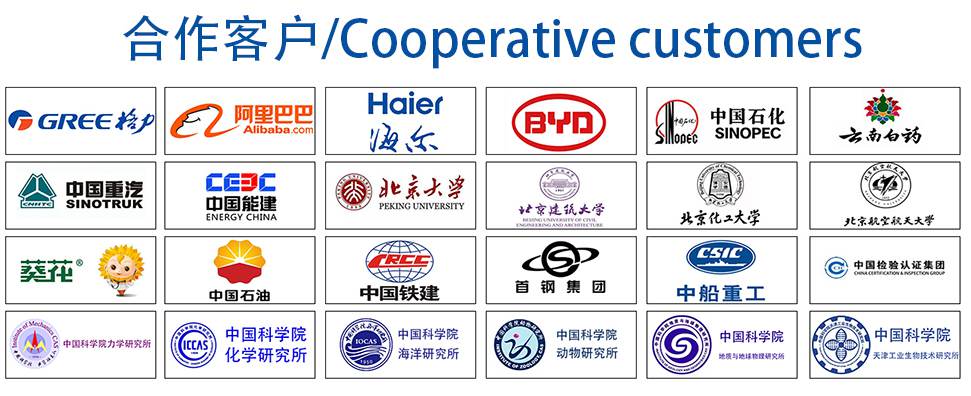