锂离子电池用聚烯烃隔膜检测的重要性
锂离子电池作为新能源领域的核心部件,其性能与安全性高度依赖于关键材料的质量。聚烯烃隔膜作为电池内部正负极间的物理屏障,承担着防止短路、调控离子传输及保障热稳定性的多重功能。随着新能源汽车、储能系统等行业的快速发展,隔膜的质量检测成为产业链中不可或缺的环节。通过系统性检测,可有效避免因隔膜缺陷引发的电池失效、热失控等风险,同时提升电池的能量密度和循环寿命。
核心检测项目及技术要求
1. 物理性能检测
• 厚度与均匀性:采用高精度测厚仪检测隔膜厚度(通常10-25μm),确保厚度波动≤±0.5μm,直接影响电池内阻和能量密度;
• 透气性(Gurley值):通过气体透过率测试评估隔膜孔隙结构,标准范围100-400s/100ml,过高影响离子传输效率,过低增加短路风险;
• 拉伸强度与穿刺强度:纵向/横向拉伸强度需≥100MPa,穿刺强度≥300g,防止组装或使用过程中机械损伤。
2. 化学稳定性检测
• 耐电解液腐蚀性:浸泡于EC/DMC电解液中168小时后,观察溶胀率(≤5%)和抗拉强度保持率(≥90%);
• 热收缩率:90℃下30分钟热收缩率需≤5%(纵向)和≤3%(横向),避免高温环境隔膜收缩导致内部短路;
• 闭孔温度与破膜温度:通过DSC分析闭孔温度(130-140℃)和破膜温度(≥160℃),确保热关闭保护功能有效性。
3. 电化学性能检测
• 离子电导率:采用交流阻抗法测试,要求≥0.8mS/cm(25℃电解液浸润后);
• 循环稳定性:模拟电池循环充放电1000次后,隔膜厚度变化需<10%,孔隙率维持初始值的85%以上。
齐全检测技术与标准体系
行业广泛采用扫描电镜(SEM)分析孔径分布(目标0.03-0.1μm)、原子力显微镜(AFM)检测表面粗糙度(Ra<50nm)。国际标准包括UL 2580、IEC 62660,国内则遵循GB/T 36363-2018《锂离子电池用聚烯烃隔膜》要求。企业还需建立动态穿刺测试、高温高湿老化试验等定制化检测方案,以适应不同应用场景需求。
结语
通过多维度的检测体系,聚烯烃隔膜可满足高安全性、高能量密度电池的开发需求。随着固态电解质、涂覆隔膜等新技术的发展,检测方法将持续迭代,为锂电池行业的创新发展提供坚实保障。
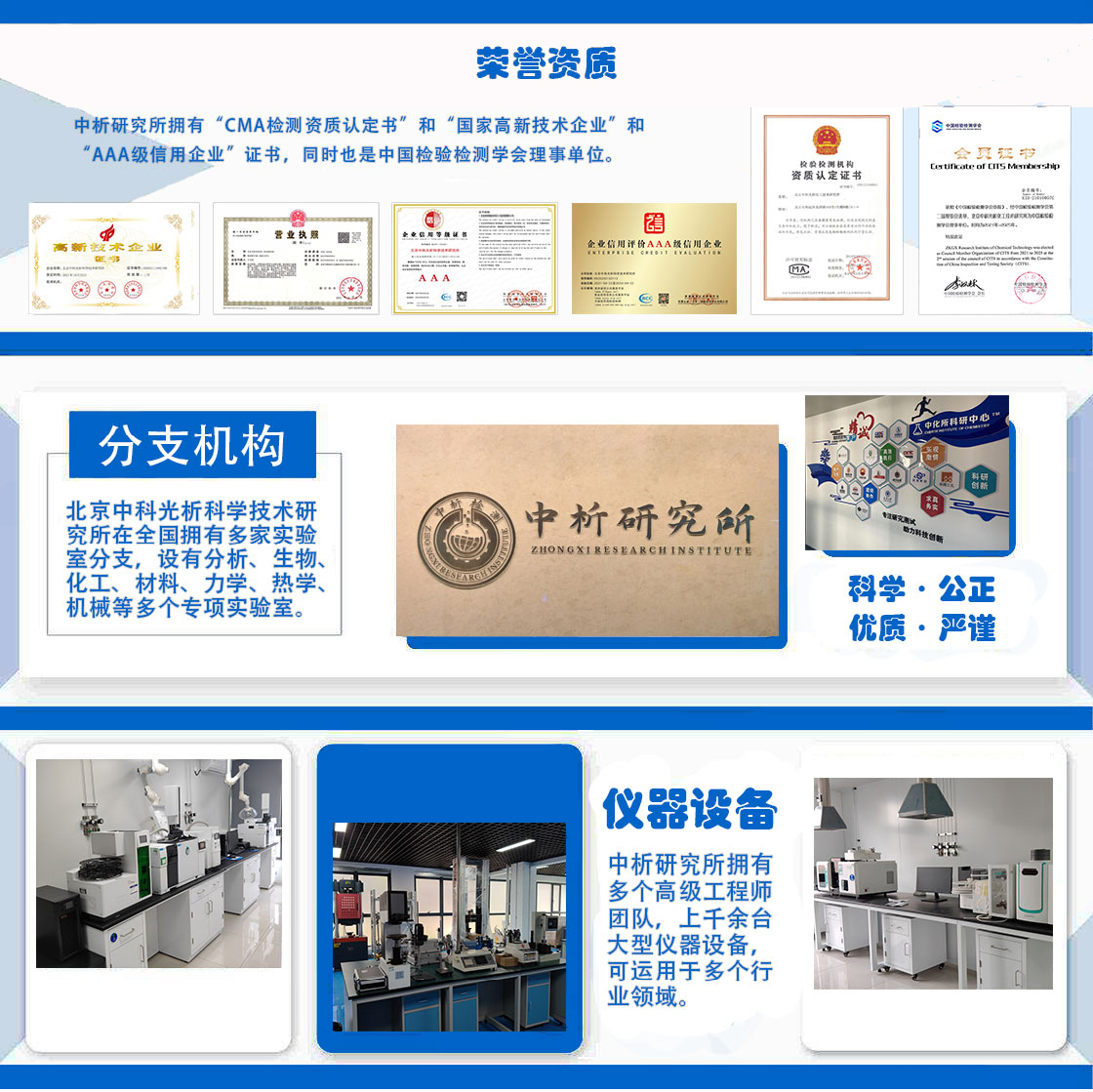
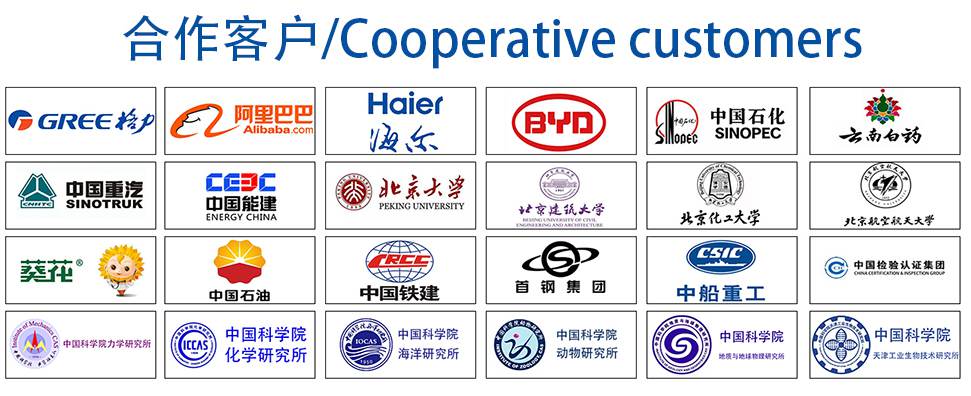