钢塑复合压力管用双热熔管件检测的重要性
钢塑复合压力管作为一种结合金属与塑料优势的新型管材,广泛应用于市政供水、燃气输送、工业流体运输等领域。其核心连接部件——双热熔管件,通过热熔技术实现管道系统的密封与承压功能,直接影响整个工程的安全性和耐久性。随着行业标准(如GB/T 19472、CJ/T 253等)的不断完善,对双热熔管件的检测要求日益严格。通过对关键项目的科学检测,能够有效避免因管件质量问题导致的泄漏、爆管等事故,保障工程长期稳定运行。
核心检测项目及方法
1. 外观与尺寸精度检测
通过目视检查和精密测量工具,评估管件表面是否光滑无裂纹、气泡或杂质,内外壁厚度均匀性是否符合标准。同时测量管件的内径、外径、椭圆度等尺寸参数,确保其与管材的匹配性。
2. 热熔性能测试
使用专用热熔设备模拟实际施工条件,检测熔接温度、时间参数的稳定性,并通过拉伸试验机验证熔接部位的抗拉强度。要求熔接面均匀无虚焊,拉伸强度需达到管材本体强度的90%以上。
3. 耐压与密封性检测
通过静液压试验和爆破压力测试,验证管件在持续压力(通常为1.5倍工作压力)和极端压力(3-5倍工作压力)下的承压能力。同时采用气压或水压法检测密封性,确保无渗漏现象。
4. 耐腐蚀与环境适应性测试
通过盐雾试验、酸碱浸泡试验评估管件金属层的抗腐蚀能力,并在高低温循环(-20℃~60℃)及紫外线老化条件下测试其性能稳定性,确保长期使用中无分层、脆化等问题。
5. 材料成分与兼容性分析
利用光谱仪、色谱仪等设备检测钢塑复合层材料的化学成分,确保聚乙烯(PE)与钢层的黏结强度符合标准。同时验证管件与输送介质的化学兼容性,防止因材料反应导致的性能退化。
结论
钢塑复合压力管用双热熔管件的系统化检测是保障工程质量的关键环节。通过覆盖外观、力学性能、环境适应性等多维度的检测项目,能够全面评估管件的可靠性,为工程安全提供科学依据,同时推动行业技术标准的持续优化。
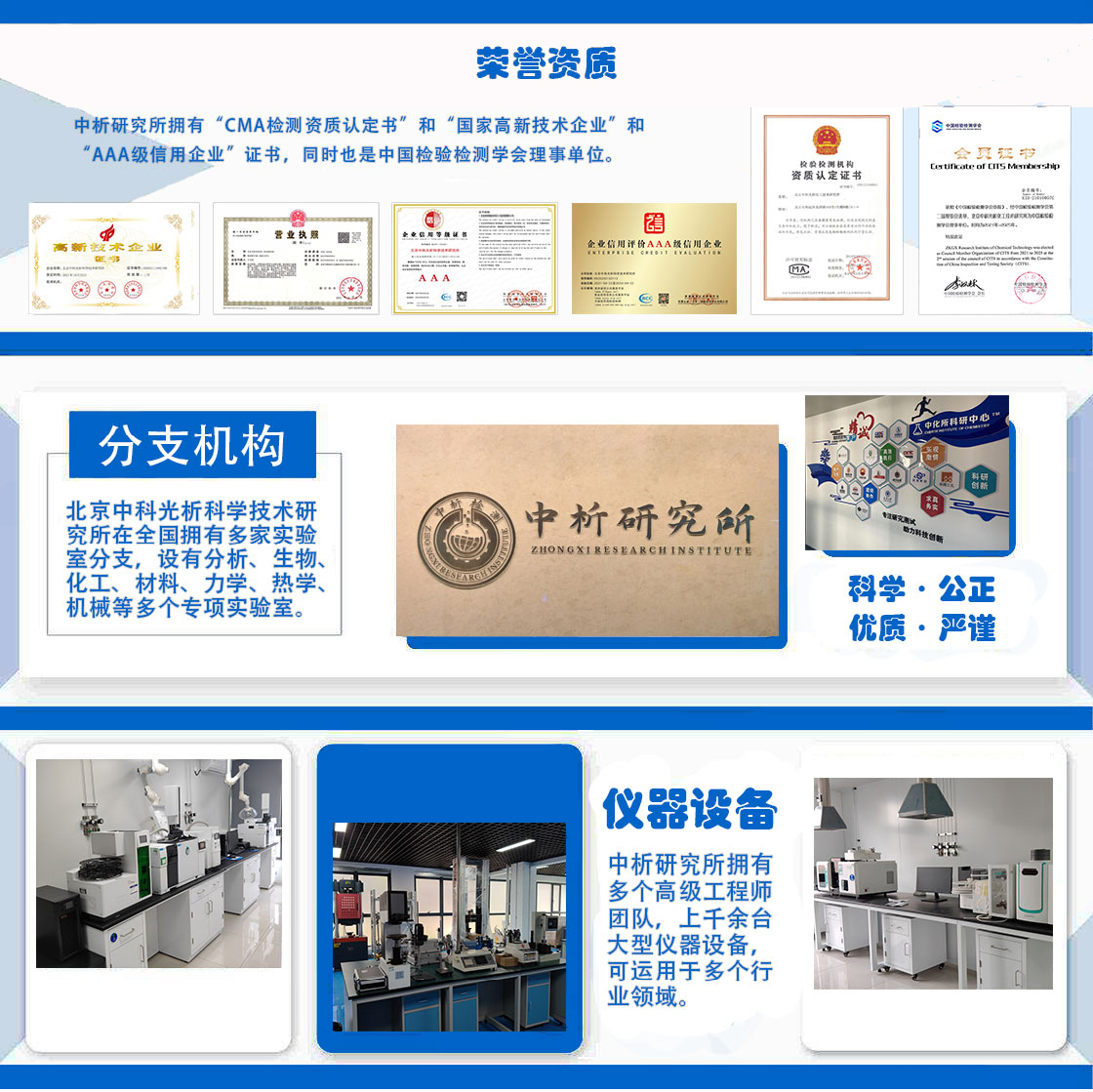
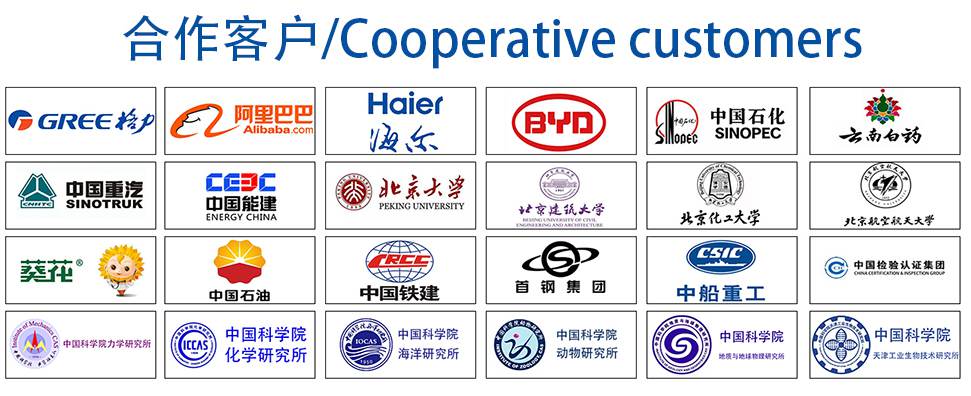